Как варить проволокой
В этой статье мы немного расскажем о методе, но в основном сконцентрируемся на проволоке. Что собой представляет, какая выпускается, как с помощью нее происходит процесс сваривания, выбор этого материала.
Содержание статьи:
Под сваркой проволокой подразумевается полуавтоматический метод, когда вместо традиционного электродного стержня – плавящаяся проволока, а зону сварки защищает инертный или активный газ. Сварщик ведет шов вручную, а проволока подается специальным устройством автоматически по мере плавления и формирования шва. Поэтому такое название – “полуавтоматическая сварка”. MIG – в среде инертного газа, MAG – в среде активного.
Проволока в полуавтоматической сварке выступает не просто расходником, а полноценной частью сварочного процесса, определяя его эффективность, качество шва и прочность соединения. При этом от ее правильного выбора и применения зависят такие факторы, как стабильность дуги, скорость выполнения работ, а также возможность сварки в различных условиях и на различных металлах. Качественная сварка нержавеющей стали или алюминия? Подготовьте проволоку!
Что такое сварочная проволока
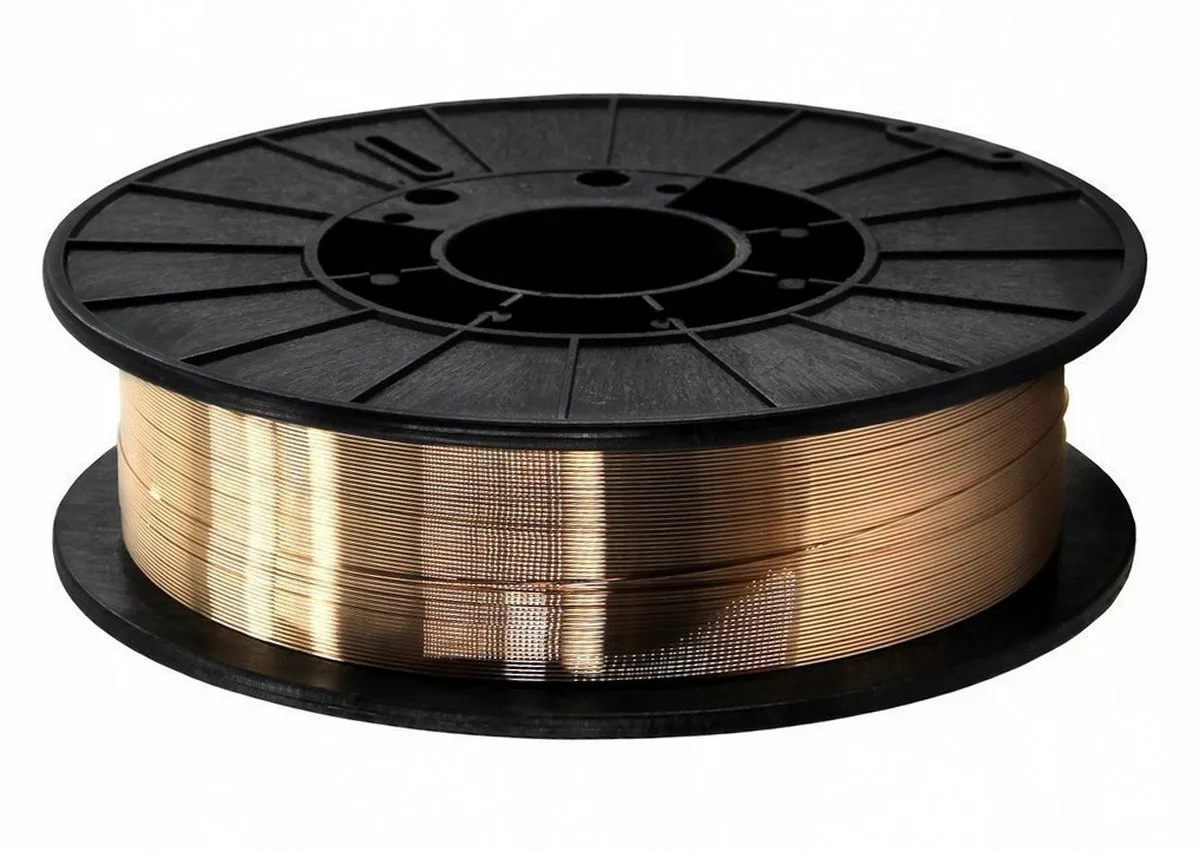
Один из ключевых элементов, применяемых в сварочных работах. Проволока в данном случае представляет собой металлическую нить различного диаметра и состава, которая используется как присадочный материал и одновременно электрод для соединения металлических деталей. Подается в зону сварки, где плавится под воздействием высокой температуры и образует сварочный шов. Обязательная при полуавтоматической сварке в среде инертного или активного газа.
Среди ее основных функций:
- Формирование сварного шва. Плавясь, проволока заполняет зазор между свариваемыми деталями, образуя прочное соединение.
- Увеличение прочности соединения. Правильный выбор проволоки, соответствующий типу основного металла, позволяет повысить прочность шва и его устойчивость к внешним воздействиям.
- Стабилизация дуги. Проволока обеспечивает постоянный поток металла в зону сварки, что способствует стабильности сварочной дуги и качественному выполнению шва.
Проволока поддерживает непрерывность процесса и стабильность дуги, помогает выполнять сварку с высокой скоростью и точностью. Будь то ремонт или крупномасштабное производство, правильно подобранная присадка – залог надежного и долговечного соединения!
Как работает
Электрический ток от источника передается через кабель на токосъемный наконечник горелки, откуда поступает на проволоку. Дуга, возникающая между концом проволоки и изделием, плавит металл, создавая сварочную ванну, которая, застывая, образует прочный сварной шов. Благодаря тому, что проволока подается непрерывно с катушки, сварщик может выполнять длинные и ровные швы, что особенно выгодно при производстве конструкций с большой протяженностью сварных соединений. В отличие от сварки покрытыми электродами, где каждый стержень необходимо менять вручную, сварочная проволока на катушках значительно ускоряет процесс работы, повышая общую производительность.
Формы выпуска и типы катушек
Сварочная проволока для полуавтоматической сварки поставляется на катушках различных типов и размеров. Основные формы выпуска – это пластиковые катушки и металлические каркасные кассеты.
Пластиковые катушки используются для сварочной проволоки весом от 1 до 5 кг, а также бывают увеличенного объема на 12–22 кг. Обозначаются, как правило, диаметром: например, D200 и D300, где 200 или 300 мм – это внешний диаметр катушки. Катушки меньшего размера применяются на маломощных или портативных сварочных аппаратах, где важна компактность и удобство при частых заменах.
Металлические кассеты, в свою очередь, служат для более крупных катушек, предназначенных для промышленного использования, с весом проволоки от 12 до 30 кг. Стандартные обозначения металлических катушек – К300 и К415, где цифры также указывают на внешний диаметр кассеты. Кассеты такого типа широко применяются на производстве – сварщики выполняют большие объемы работ без необходимости часто менять проволоку.
Преимущества крупных катушек
В производственных условиях использование катушек большого объема значительно экономит время. Крупные кассеты особенно удобны для многочасовой сварки, так как не требуется останавливать процесс для замены расходника. В противном случае, при использовании малых катушек, приходится чаще менять кассеты, тратить время на заправку проволоки и установку новой катушки. Таким образом, для задач с большим объемом сварочных работ более крупные катушки предпочтительны, так как они минимизируют простой оборудования и сокращают время, затрачиваемое на обслуживание.
Маркировка
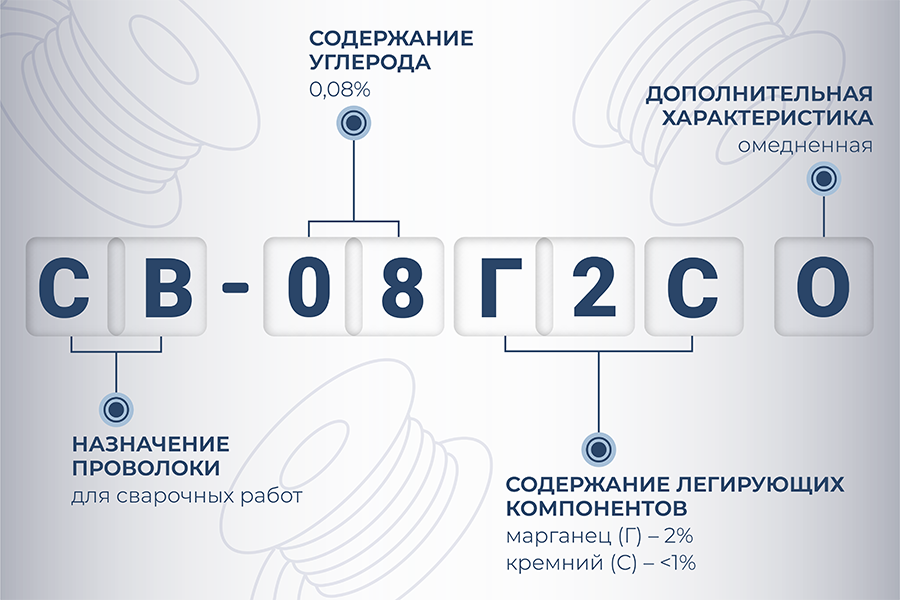
В России сварочная проволока маркируется по ГОСТу, чтобы сварщик мог быстро определить ее состав и основные свойства, ориентируясь на буквенно-цифровое обозначение. Каждая комбинация символов несет информацию о назначении и химическом составе, помогая правильно выбрать расходник для конкретных задач.
Например, Св-08Г2С-О ГОСТ 2246-70. Вот расшифровка:
- Св – указывает на предназначение проволоки – сварочные работы.
- 08 – обозначает содержание углерода в составе на уровне 0,08%.
- Г2 – присутствие марганца в количестве 2%.
- С – содержание кремния менее 1%.
- О – свидетельствует о наличии омедненного покрытия, защищающего от коррозии и улучшающего проводимость.
ГОСТ, указанный в конце маркировки, подтверждает, что проволока произведена по определенному стандарту, в данном случае ГОСТ 2246-70.
Проволока Св-08Г2С занимает около 95% рынка и считается универсальной для сварки различных металлоконструкций из низкоуглеродистой стали, таких как трубы, уголки и швеллеры.
Дополнительные химические элементы, входящие в состав присадки, также обозначаются буквами:
- Ц – цирконий.
- А – азот.
- Ф – ванадий.
- Б – ниобий.
- Ю – алюминий.
- В – вольфрам.
- Х – хром.
- Д – медь.
- Н – никель.
- Т – титан.
- С –кремний.
Кроме того, если в конце присутствует буква А, это означает, что проволока изготовлена из стали с пониженным содержанием примесей. Двойная АА указывает на еще более высокую степень очистки материала.
Благодаря системе маркировки по ГОСТу сварщики могут легко ориентироваться в составе и характеристиках сварочной проволоки, выбирая подходящий вариант для каждого конкретного типа работ.
Виды присадки
Сварочная проволока – важнейший расходный материал, незаменимый в сварочном процессе. Ее широко применяют в полуавтоматических сварочных аппаратах, где выполняет функцию присадочного элемента и электрода, объединяющего металлические детали в единое прочное соединение. От грамотного выбора проволоки напрямую зависят качество, надежность и долговечность сварного шва. Сегодня существует множество разновидностей данной составляющей полуавтоматической сварки, каждая из которых имеет свои особенности и предназначена для конкретных задач и условий. Рассмотрим основные типы и их характеристики.
Сплошная
Стандартный вид проволоки, не имеющий пустот или наполнителей внутри. Сплошная присадка используется в основном для сварки низкоуглеродистых и нержавеющих сталей. Ценится за высокую прочность шва, простоту в использовании и широкий ассортимент марок и диаметров. Доступна от 0,6 до 1,6 мм, легко найти подходящий вариант в зависимости от толщины свариваемых материалов и особенностей процесса. Задействуется как в среде активных (MAG), так и в среде инертных газов (MIG) – универсальный выбор для различных условий сварки.
Порошковая
Отличается от сплошной наличием наполнителя в виде порошка внутри металлической оболочки. Наполнитель порошковой проволоки может содержать флюсы, защитные газы или легирующие элементы, улучшающие свойства сварочного шва. Материал применяется для сварки низкоуглеродистых сталей, а также при повышенных требованиях к прочности шва.
Виды такой проволоки:
- С самозащитой – применяется без защитного газа благодаря флюсу, находящемуся внутри прутка. Позволяет проводить сварку в сложных условиях, например, на открытом воздухе, где присутствует ветер.
- С газовой защитой. Используется в сочетании с защитным газом, обычно углекислым, с помощью нее получают высококачественные швы с отличной прочностью и стойкостью к внешним воздействиям.
Металлические порошки в составе обычно используются из стали, но также добавляют алюминий, никель или медь в зависимости от требований к сварному шву.
Легирующие элементы – улучшают механические свойства шва. Например, хром, молибден или ванадий.
Флюсы, в свою очередь, снижают температуру плавления, улучшают защиту шва от окисления и повышают качество сварного соединения.
Благодаря составу достигается высокая однородность и прочность шва, а также его отличные эксплуатационные характеристики.
Омедненная
Омедненная проволока покрыта слоем меди, который предотвращает коррозию, улучшает электрическую проводимость и снижает износ оборудования. Подходит для сварки углеродистых и низколегированных сталей и широко используется на производственных предприятиях.
Ее плюсы:
- Устойчивость к окислению – увеличивает срок хранения.
- Улучшенное прохождение тока – снижает нагрев сварочного оборудования.
- Повышенная стабильность дуги и уменьшение разбрызгивания металла.
Медь защищает от коррозии, увеличивая срок службы как самой проволоки, так и сварного шва.
Благодаря хорошей текучести и способности легко проходить через сопло сварочного аппарата омедненная проволока снижает риск засорения оборудования. Устойчивость к коррозии, хорошая электропроводность и прочность делают ее прекрасным выбором для специалистов, желающих добиться высокого качества и надежности сварных соединений!
Нержавеющая
Нержавеющая сварочная проволока – незаменимый компонент в арсенале сварщиков, который работает на надежное и прочное соединение металлических деталей. Благодаря своим уникальным свойствам и разнообразию применения стала важной составляющей в различных отраслях, от строительства до судостроения и автомобилестроения.
Основное назначение заключается в сварке нержавеющих сталей, которые используются в производстве оборудования для пищевой, химической и фармацевтической промышленности. Проволока гарантирует создание прочных соединений, способных выдерживать нагрузки и воздействия, которые часто встречаются в этих сферах.
Одним из ключевых преимуществ нержавеющей присадки является способность создавать антикоррозионные соединения. Это особенно важно в условиях высокой влажности или в средах, содержащих агрессивные химические вещества.
Кроме того, используется в сварке в сложных условиях – высокая температура и давление. В таких отраслях, как энергетика, где всегда в приоритете надежность и долговечность соединений.
Нержавеющая проволока выпускается разная, и дело не только в диаметре, но и в конкретных задачах. Например:
- ER308L – для сварки аустенитных нержавеющих сталей, обладает хорошей коррозионной стойкостью. Применяется в судостроении и пищевой промышленности, где важно сохранять высокие стандарты безопасности.
- ER316L – благодаря добавлению молибдена эта проволока значительно повышает устойчивость к коррозии, особенно в средах с высоким содержанием хлоридов. Востребована в химической и нефтехимической промышленности, где условия работы крайне агрессивные.
- ER2209 – этот тип служит для сварки дуплексной нержавейки, которая сочетает свойства аустенитных и ферритных сталей. Используется в тех случаях, когда требуется высокая прочность соединений и стойкость к коррозии.
Использование нержавеющей сварочной проволоки связано со множеством преимуществ. Прежде всего она отличается высокой коррозионной стойкостью, значительно увеличивает срок службы сварных соединений. Снижает затраты на обслуживание и ремонт – важный фактор в современных производственных условиях.
Кроме того, соединения, выполненные с использованием нержавеющей проволоки, характеризуются высокой прочностью и долговечностью. Это делает их идеальными для эксплуатации в самых разных условиях – от строительных объектов до высокотехнологичного оборудования.
Не стоит забывать и о термостойкости. Проволока сохраняет свои свойства даже при экстремальных температурах, востребована в сварке трубопроводов и оборудования энергетических систем.
Представляет собой многофункциональный материал, с помощью которого реализуют надежные и долговечные соединения в различных сферах деятельности. Правильный выбор типа проволоки в зависимости от специфики работы не только гарантирует высокое качество сварки, но и обеспечивает долговечность соединений. Использование такой присадки – залог успеха в любом производственном процессе, где требуется надежность, прочность и коррозионная стойкость.
Алюминиевая
Алюминиевая сварочная проволока – расходный материал, используемый в процессе сварки алюминия и его сплавов. Благодаря своим уникальным свойствам обеспечивает высокое качество соединений и широко применяется в различных отраслях.
Представляет собой тонкую проволоку, предназначенную для использования в сварочных процессах MIG/MAG и TIG. Задействуется как в ручной, так и в автоматизированной сварке. В отличие от стальной проволоки, алюминиевая легкая, высокой коррозионной стойкости и с отличной проводимостью электричества.
Среди ее особенностей:
- Низкая плотность – алюминий значительно легче стали, упрощает работу и уменьшает нагрузку на оборудование.
- Коррозионная стойкость – алюминий не ржавеет, подходит для использования в условиях, где требуется долговечность.
- Проводимость – имеет высокую электропроводность, улучшая сваривание алюминия и сплавов.
Проволока обычно изготавливается из алюминиевых сплавов, которые включают различные легирующие добавки – магний (Mg), кремний (Si) и медь (Cu). Добавки улучшают механические свойства и свариваемость материала. Наиболее распространенные марки проволоки:
- AlMg5 – содержит магний, ценится за высокую коррозионную стойкость.
- AlSi5 – с кремнием, используется для сварки легированных алюминиевых сплавов.
Материал доступен разного диаметра, выбирается в зависимости от толщины свариваемых заготовок.
Наиболее распространенные:
- 0,8 мм – для сварки тонких алюминиевых листов, применяется в электронике и автомобилестроении.
- 1,0 мм – универсальный диаметр, подходит как для тонких, так и для средних толщин материалов.
- 1,2 мм – используется для сварки более толстых заготовок, применяется в строительстве и тяжелом машиностроении.
- 1,6 мм и больше – для промышленных процессов, где требуется высокая производительность и толстые соединения.
Алюминиевая проволока – один из ключевых материалов, который занимает важное место в современных производственных процессах. Благодаря своим уникальным свойствам находит широкое применение в самых различных отраслях, от автомобилестроения до аэрокосмической промышленности. Представлена в большом разнообразии, позволяет находить оптимальные решения для различных сварочных задач. Понимание особенностей, состава и различных видов алюминиевой сварочной проволоки – аспект, который помогает специалистам сделать осознанный выбор. Это, в свою очередь, гарантирует высокое качество сварочных соединений и долговечность конечной продукции.
Специальная
Специальная сварочная проволока – никелевая, медная, титановая и термостойкая.
Никелевая – для сварки конструкций, требующих высокой коррозионной стойкости и устойчивости к высоким температурам. Подходит для соединения сталей, содержащих никель, а также для нержавеющих сталей. Неплохо защищает от коррозии, созраняет механические свойства при значительных температурах. Используется в химической, пищевой и нефтяной промышленности, а также в производстве оборудования для атомной энергетики.
Медные сварочные проволоки также находят широкое применение благодаря своей высокой проводимости и коррозионной стойкости. Они часто используются для сварки меди и медных сплавов, а также в электротехнических сферах.
Титановые присадки применяются для сварки титана и его сплавов. Титан известен высокой прочностью и легкостью, а также хорошей коррозионной стойкостью. Проволоки используются в авиации, космической отрасли, а также в производстве медицинского оборудования и имплантатов.
Термостойкие – предназначены для соединения материалов, которые подвержены воздействию высоких температур. Они часто используются для сварки жаропрочных сталей и других сплавов. Сохраняют свои механические свойства и прочность при высоких температурах, идеальны для сварки в условиях термических нагрузок. В состав могут входить специальные легирующие элементы, которые улучшают свойства при высоких температурах. Широко применяются в энергетике, металлургии и в производстве оборудования для высокотемпературных процессов.
Как выбрать
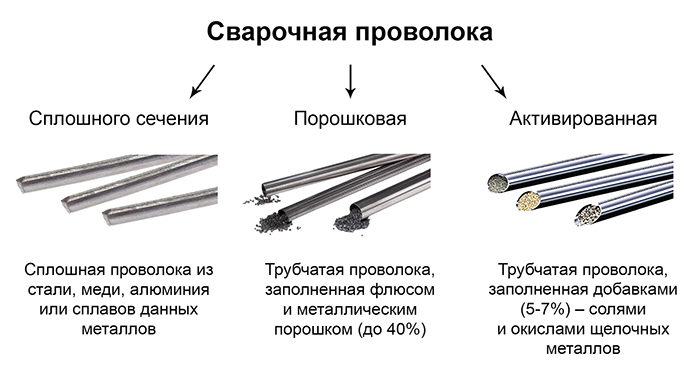
Варить полуавтоматом – уметь выбирать проволоку, без этого в процессах MIG/MAG никак. И здесь учитываем целый ряд параметров:
- Назначение;
- Структура;
- Легирующие элементы;
- Диаметр;
- Поверхность;
- Свариваемые металлы;
- Состав.
Итак, назначение – на рынке сварочных материалов можно найти проволоку общего и специального назначения. Первая подходит для сварки стали автоматизированными и полуавтоматическими методами. Показывает эффективность в наплавке и ремонте стандартных стальных конструкций.
Специальная – востребована в сложных условиях – например, под водой или на высоте. Ее используют при соединении различных металлов и сплавов – алюминий, медь, чугун, никель и титан. Чтобы швы были более устойчивыми и предотвращали межкристаллитную коррозию, в металл добавляют специальные модифицирующие вещества.
Структура – по этому параметру выделяют три вида присадки: сплошная, порошковая, активированная.
Сплошная проволока представляет собой металлический сердечник без полостей, выполненный из стали, меди, алюминия или титановых сплавов. Она применяется для изготовления электродов и как присадочный материал в механизированной сварке с защитой газами – аргон, азот, или углекислота, либо под слоем флюса.
Порошковая (самозащитная) проволока состоит из тонкой трубки, заполненной флюсом или смесью порошков, ферросплавов и оксидов, выполняющих защитную функцию сварочной ванны, как и покрытие электродов. Этот тип присадки универсален, подходит для промышленной и бытовой сварки.
Активированная проволока также имеет трубчатую форму, однако в ее составе содержится 5-7% флюса и стержень из прессованного порошка, выступающий в роли фитиля. В композитном покрытии присутствуют активаторы – оксиды кремния, титана, магния и карбонаты, отвечающие за быстрый розжиг дуги и стабильное горение с минимальным разбрызгиванием металла.
Другой параметр – легирующие элементы. Ими выступают хром, никель, марганец, молибден, кремний, а также тугоплавкие сплавы на основе вольфрама. По процентному содержанию легирующих добавок выделяют следующие виды проволоки:
- Низколегированная – до 2,5% легирующих элементов.
- Среднелегированная – от 2,5% до 10%.
- Высоколегированная – более 10%.
Добавляя в состав легирующие элементы, создают проволоку с улучшенными техническими характеристиками. Например, сплав с 20% меди и ниобием характеризуется высокой прочностью, а ниобий в сочетании с алюминием защищает сплав от воздействия щелочей. В сочетании со сталями он повышает устойчивость к окислению.
Легирующие добавки повышают коррозийную стойкость, ударную вязкость и жаропрочность, делают сварочную проволоку пригодной для различных условий эксплуатации.
Один из ключевых параметров присадки – диаметр. Сварочная проволока выпускается в 17 стандартных диаметрах, согласно ГОСТ, от 0,3 до 12 мм. Выбор здесь зависит от толщины свариваемого металла: чем толще заготовка, тем больший диаметр присадки требуется, чтобы получить надежное соединение.
Тонкая проволока имеет преимущества в точности процесса: быстрый поджиг, стабильное горение дуги и минимальное разбрызгивание металла, что особенно важно при деликатных работах. При использовании присадочного материала с большим диаметром необходимо повышать силу тока, чтобы поддерживать оптимальные условия сварки.
Помимо диаметра нельзя не учитывать поверхность проволоки. Омедненная, обозначаемая буквой «О», и неомедненная, не имеющая покрытия. Вид поверхности определяет многие свойства готового шва. Неомедненная проволока предназначена для общих сварочных задач – наплавка и производство электродов.
Покрытие медью предоставляет ряд преимуществ: снижает разбрызгивание металла на 40%, уменьшает усилия при подаче проволоки и улучшает ее коррозийную стойкость. Благодаря низкому контактному сопротивлению омедненная проволока отличается высокой проводимостью тока, способствует быстрому поджигу, устойчивому горению дуги и минимальному разбрызгиванию. Также формирует швы с меньшим количеством вредных примесей, повышая качество сварки.
Далее смотрим на свариваемые металлы. Для сварки углеродистой стали рекомендуются омедненные и порошковые присадочные проволоки:
- Св-08Г2С – идеальна для тонкостенной стали и сварки под высоким давлением (емкости, трубы), зарубежный аналог – ER70S-6.
- Св-09Г2С – легированная, для низкоуглеродистых сталей.
- Св-10ГА – низкоуглеродистая, подходит для аргонодуговой сварки.
- Св-08ГСМТ – для конструкционной стали типа 15Г2СФ.
- Св-01Х17Н14М – дает устойчивость к межкристаллитной коррозии.
Для алюминия применяют проволоку из чистого алюминия или его сплавов:
- Св-АК5, Св-АК6 – термоустойчивые, пластичные сплавы.
- Св-1201 – соединение алюминия с высокими требованиями к качеству шва.
- Св-А85, Св-А97, Св-АМЦ – чистый алюминий и сплавы, устойчивые к химическим и атмосферным воздействиям.
Сварка аустенитных и коррозионностойких сталей требует защитной газовой среды и специальных добавок:
- Св-06Х19Н9Т, Св-06Х21Н7БТ, Св-01Х19Н9 – жаропрочные и коррозионностойкие стали.
- Св-08Х19Н10М3Б, Св-06Х20Н11М3ТБ – стали с никелем, хромом и молибденом.
Эти присадки содержат углерод, предотвращающий коррозию, и кремний, увеличивающий прочность шва.
При сварке меди, подверженной окислению, используют медноникелевую или меднокремниевую проволоку в среде аргона или гелия.
Чугун и никель СВ08Г2 и СВ08Г2С варят ПП АНЧ-1 – холодный и полугорячий метод (подогрев до 350 °С). ПП АНЧ-3 – горячий метод с подогревом до 600 °С.
Сварка чугуна проводится полуавтоматами на постоянном токе обратной полярности.
И, наконец, состав. Стальная проволока – одна из самых распространенных. Задействуется в строительстве, машиностроении, коммунальном хозяйстве и энергетике. Ею варят, наплавляют, режут низкоуглеродистые, средне- и высоколегированные стали в среде защитных газов или под флюсом. Наиболее популярные марки:
- Св-08, Св-10Г2, Св-ЮГЛ – для конструкций из низкоуглеродистых сталей.
- Св-08ГС, Св-08Г2С, Св-18ХС – низколегированные и среднелегированные стали;
- Св-08Х14ГНТ, Св-12Х13 – высоколегированные стали.
Легирование хромом, никелем и марганцем позволяет использовать стальную проволоку для сварки высокоуглеродистых нержавеющих сталей.
Другой вариант – алюминиевая проволока. Предназначена для полуавтоматической сварки алюминия и его сплавов, особенно с добавлением магния, кремния или меди, формирует прочные, коррозионно устойчивые соединения, сохраняющие цвет заготовки. Такая проволока востребована в автомобилестроении и судостроении, где требуется высокая устойчивость металла к воздействию воды.
Омедненная проволока – производится из низколегированных и низкоуглеродистых сталей, покрытых медью, она улучшает проводимость и антикоррозийные свойства. Преимущества омедненной присадки:
- Минимальное разбрызгивание металла;
- Экологическая безопасность за счет малого количества примесей;
- Скорость подачи и производительность.
Эта проволока идеально подходит для аргонодуговой сварки и используется при производстве резервуаров, трубопроводов, судов и железнодорожных вагонов. Процесс проводится в атмосфере углекислого газа или смеси аргона и CO₂, так как защитные компоненты не входят в состав самой проволоки.
В магазине найдете еще трубчатую самозащищенную проволоку, заполненную порошковым наполнителем, который играет роль флюса, заменяя газ. Присадки составляют 14–40% и защищают сварочную ванну от атмосферных воздействий. Такая проволока удобна для работы на высоте и в условиях, где газовые баллоны доставить невозможно. Марка ПП2ДС подходит для сварки нержавеющей стали, оцинкованного железа и углеродистых сталей.
Важно, чтобы состав проволоки соответствовал составу соединяемых металлов, так получится сформировать прочный и качественный сварной шов!
Техника безопасности при сварке проволокой
Полуавтоматическая сварка присадочной проволокой – современная техника, широко применяемая в строительстве, автомобильной и судостроительной отраслях, а также в бытовом ремонте. Несмотря на свою универсальность и эффективность, сварка MIG/MAG потенциально опасная, поскольку сопряжена с рядом рисков для здоровья и безопасности. Поэтому соблюдение техники безопасности – первостепенная обязанность любого сварщика.
Опасности, возникающие при сварке проволокой
Сварочные работы, особенно с использованием MIG/MAG технологии, связаны со следующими рисками:
- Ультрафиолетовое и инфракрасное излучение. Сварочная дуга испускает интенсивное излучение, способное повредить кожу и глаза. Если не использовать специальную защиту, можно получить серьезные ожоги и травмы роговицы.
- Высокая температура. При сварке образуется очень высокая температура, она создает риск получения ожогов даже на расстоянии от дуги.
- Вредные газы и пары. В процессе сварки выделяются вредные вещества: озон, окислы азота и металлы – марганец и хром. Эти вещества опасны для дыхательной системы.
- Риск поражения электрическим током. Сварочные аппараты работают при высоком токе, поэтому даже небольшая ошибка может привести к серьезнейшему поражению организма.
- Металлические брызги и искры. Брызги расплавленного металла и искры могут попасть на кожу или на воспламеняющиеся материалы, увеличивают вероятность ожогов и возникновения пожара.
Правильная подготовка значительно снижает риски. Основные меры предосторожности предполагают использование средств индивидуальной защиты, организацию рабочего пространства и проверку оборудования.
Средства индивидуальной защиты
Конечно, не обойтись без сварочной маски. Современная, удобная и эффективная – с автоматическим затемнением. Защищает глаза и лицо от вредного излучения, а автоматическое затемнение упрощает контроль процесса сварки, так как затемнение увеличивается только при образовании дуги. Дополнительные защитные очки могут потребоваться для операций, предшествующих сварке, например, зачистки или шлифовки металла.
Обязательно подготовьте еще:
- Кожаные перчатки и рукава. Кожаные изделия надежно защищают руки и предплечья от высоких температур и металлических брызг.
- Защитную одежду. Важно выбирать огнеупорную, которая полностью закрывает кожу, предпочтительно из плотного хлопка или других негорючих материалов. Одежда из синтетики опасна, так как может легко расплавиться при контакте с искрами.
- Респиратор или маска с фильтром. Респиратор защитит органы дыхания от ядовитых паров и частиц.
Все готово, кроме респиратора? Ни в коем случае не варите без него! Во-первых, предотвращает попадание в легкие мелких частиц оксидов металлов, содержащихся в сварочном дыме. Во-вторых, защищает от вредных газов – озон, инертные газы, выделяющиеся при сварочной дуге. Особенно важен при сварке нержавеющей стали, которая содержит токсичные соединения – оксиды никеля и хрома VI, представляющие серьезную угрозу для здоровья.
Организация рабочего пространства
Безопасность рабочего пространства также имеет значение. Сварка проволокой сопровождается выделением токсичных газов, поэтому зона работы должна быть оснащена мощной вентиляцией для защиты от вредных веществ.
Все горючие вещества (бумага, дерево, ткань) необходимо удалить из зоны сварки.
Электрооборудование должно быть заземлено, чтобы предотвратить удар током. Поверхность пола в рабочей зоне – диэлектрическая.
Рабочее пространство – с идеальным освещением, чтобы сварщик мог контролировать процесс и своевременно заметить потенциальные опасности.
Проверка оборудования
Перед началом сварочных работ необходимо провести тщательную проверку сварочного аппарата – безопасность превыше всего, ну, и не стоит забывать об эффективности процесса.
В первую очередь выполняется визуальный осмотр, чтобы выявить возможные повреждения. Затем проверяется заземление источника питания для предотвращения поражения электрическим током.
Необходимо измерить сопротивление изоляции, чтобы убедиться в отсутствии утечек. Следующий этап – контрольное включение аппарата в режиме холостого хода на 5 минут и более, что позволяет оценить его работу. Также нужно контролировать исправность цепей защитного заземления и провести испытания повышенным напряжением для выявления скрытых дефектов.
После этого очищаются поверхности от пыли и грязи, а также проверяются винтовые соединения на надежность. Завершает процедуру смазка трущихся частей, это необходимо для бесперебойной работы оборудования. Тщательная подготовка минимизирует риски и повышает надежность сварочного процесса!
Вентиляция
Вентиляция играет ключевую роль в безопасности и здоровья при сварке проволокой в среде инертного или активного газа, ее значение нельзя переоценить. Процесс MIG/MAG, хотя и высокоэффективный и универсальный, сопровождается выделением различных вредных веществ, которые оказывают негативное влияние на здоровье сварщика и окружающих.
- Дуга возбуждена, проволока плавится, как и заготовки – образуется сварочный дым, содержащий мелкие частицы оксидов металлов и различные химические соединения. К числу наиболее опасных веществ относятся:
- Озон. Этот газ образуется в результате разряда электрической дуги и может вызывать раздражение дыхательных путей, а в больших концентрациях – серьезные проблемы со здоровьем.
- Окислы азота. Они формируются в процессе горения и вызывают аллергические реакции, а также влияют на функции легких.
- Металлические пары. При сварке выделяются токсичные металлы – никель и хром, особенно при работе с нержавеющей сталью. Эти соединения становятся причиной долгосрочных проблем со здоровьем, обостряются заболевания дыхательной системы.
Правильная организация вентиляции в сварочной зоне – это не просто рекомендация, а обязательное условие для здоровья сварщиков. Эффективная вентсистема решает несколько задач:
- Удаление вредных газов и частиц. Вытяжные устройства помогают быстро и эффективно удалять сварочные пары и газы, снижая их концентрацию в воздухе. Предотвращают накопление токсичных веществ, что критично при длительных сварочных работах.
- Постоянный приток свежего воздуха. Правильная вентиляция обеспечивает приток свежего воздуха, помогая поддерживать комфортные условия труда.
- Снижение температуры и влажности. При сварке выделяется много тепла, из-за этого условия работы часто становятся некомфортными. Вентиляция регулирует температуру и влажность, поддерживая более благоприятную рабочую атмосферу.
Перед свариванием обязательно включите вытяжку! Удаляет загрязненный воздух непосредственно из зоны работы.
Даже с установленными вытяжными системами дополнительно проветривайте помещение. Стабильный подпор и усиленная циркуляция воздуха не помешают!
Не забывайте проверять состояние вытяжных и приточных вентиляторов. При необходимости обслужите вентсистему!
Организация надлежащей вентиляции – один из основных элементов обеспечения безопасности на рабочем месте. Она не только защищает здоровье сварщика, снижая риски, связанные с вредными выбросами, но и способствует повышению общей эффективности работы. Важно понимать, что безопасность – не только личная ответственность каждого сварщика, но и обязанность работодателя создавать безопасные условия труда. Забота о вентиляции – шаг к здоровью, безопасности и комфорту всех, кто работает в этой опасной, но важной профессии!
Контроль положения и осанки
Правильная поза сварщика снижает физическую нагрузку, уменьшает вероятность случайных движений и ошибок. Всегда старайтесь занимать устойчивое положение, чтобы вам было легко удерживать контроль горелки!
Правила безопасности во время сварки
При работе с аппаратом необходимо следить за всеми аспектами его эксплуатации.
Не прикасайтесь к горелке, проволоке или сварочному аппарату мокрыми руками.
Обязательно держите руки и другие части тела на безопасном расстоянии от сварочной дуги и горячего металла.
Используйте только проверенные и качественные расходники. Некачественная проволока может привести к образованию пор и других дефектов шва, а также вызвать дополнительное выделение вредных веществ.
Металлические капли и искры, возникающие при сварке, опасны для кожи и окружающих предметов.
Старайтесь работать с дугой таким образом, чтобы брызги и искры были направлены от вас.
Используйте защитные экраны или щиты, чтобы предотвратить попадание искр на близлежащие материалы или других людей в рабочей зоне.
Следите за тем, чтобы поверхность под ногами была чистой и свободной от скользких или горючих веществ.
Меры безопасности после завершения сварки
После завершения сварки сразу выключите аппарат и отсоедините его от сети. Осмотрите горелку, кабели и провода на предмет повреждений. Это поможет избежать неожиданных поломок в будущем.
Соберите металлические отходы и другой мусор, чтобы избежать травм и создать чистоту для последующих работ.
После сварки не отключайте сразу вытяжку, еще важно оставить рабочее помещение открытым, чтобы усилить проветривание, быстро устранить вредные газы.
Еще обратите внимание вот на что:
- Обучение и сертификация сварщиков. Все, кто занимается сваркой, должны пройти соответствующее обучение и сертификацию по технике безопасности.
- Пожарная безопасность. В зоне сварки всегда должен быть огнетушитель или другой инструмент пожаротушения – песок или огнестойкое покрывало.
- Регулярная проверка и обслуживание оборудования. Все элементы сварки нуждаются в регулярном осмотре и чистке.
- Медицинский осмотр. Для сварщиков рекомендуется проходить периодические обследования контроля состояния здоровья, особенно органов дыхания и зрения.
Сварка проволокой предполагает неукоснительное соблюдение техники безопасности, поскольку игнорирование этого может привести к серьезным травмам и долгосрочным проблемам со здоровьем. Следование всем рекомендациям по подготовке, защите и организации рабочего пространства поможет минимизировать риски и создать условия безопасной и эффективной работы!
Оборудование и расходники
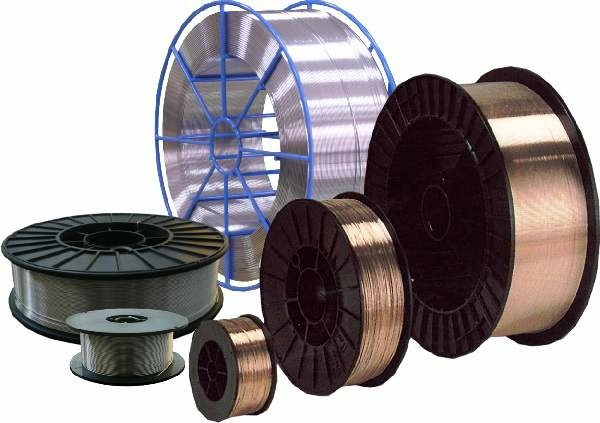
Один из наиболее востребованных и эффективных методов соединения металлических материалов, особенно стали и алюминия, – сварка проволокой в среде защитного газа. Какое оборудование для этого потребуется? Источником тока и присадкой не обойтись.
Инверторный аппарат
Безусловно, ключевым элементом сварки проволокой выступает источник тока сварочной дуги. В него также встроен механизм подачи проволоки, есть система управления сварочным процессом.
Сегодня наиболее распространены аппараты инверторного типа. В отличие от устаревших трансформаторов потребляют меньше электроэнергии, с высоким КПД, более стабильны при перепадах напряжения, поддерживают широкий функционал, упрощающий сварочный процесс. Например, синергетика – автоматическая настройка параметров в несколько нажатий.
Итак, для сварки проволокой в среде газа нужен сварочный аппарат, поддерживающий режимы работы MIG/MAG.
Что касается механизма подачи сварочной проволоки, служит для непрерывного и стабильного введения присадочного материала в зону сварки. Он может быть как встроенным в корпус аппарата, так и выполненным в виде отдельного блока. Чтобы процесс проходил плавно и стабильно, механизм подачи должен обладать высокой мощностью и точной регулировкой скорости подачи проволоки.
Проволока
О проволоке мы говорили выше. Это основной материал, используемый для создания сварочного шва. Подается в автоматическом режиме и плавится под воздействием дуги, образуя соединение между свариваемыми деталями.
Выбор проволоки зависит от материала сварки: выпускаются специальные проволоки для углеродистой и нержавеющей стали, алюминия и других металлов.
Порошковая проволока используется в тех случаях, когда нет возможности или необходимости использовать защитный газ. Она содержит внутри флюс, который, плавясь, образует защитную атмосферу вокруг сварочной ванны, предотвращая окисление металла. С помощью нее сварочные работы возможны на открытом воздухе и в сложных условиях. Но при этом дороже, чем обычная присадка.
Горелка
Предназначена для передачи тока к сварочной проволоке, подачи защитного газа и направления дуги на рабочую поверхность.
Стандартная горелка состоит из следующих элементов:
- Корпус и рукоятка – удобный и устойчивый к нагреву корпус, оснащенный защитой от перегрева. Рукоятка часто имеет эргономичную форму для комфортного удержания.
- Токоподводящий канал – через него к проволоке поступает электрический ток, обеспечивая формирование сварочной дуги.
- Сопло – направляет поток защитного газа к сварочной ванне, предотвращая попадание кислорода и образование пор. Сопло также помогает направлять дугу.
- Контактный наконечник – проводит ток к сварочной проволоке и поддерживает надежный контакт, от него зависит стабильность дуги.
- Система подачи защитного газа – подает газ к сварочной зоне для создания защитной среды.
- Система охлаждения – защищает горелку от перегрева, особенно при интенсивной или долгой сварке.
Горелка подключается к сварочному аппарату с помощью гибкого шланга, через который подаются ток, проволока и газ.
Доступны сегодня несколько видов горелок, которые отличаются в зависимости от условий и типа сварки:
- С воздушным охлаждением – используют естественное охлаждение воздуха и подходят для работ с небольшой интенсивностью и на тонких материалах. Они проще в обслуживании, но имеют ограничения по продолжительности действия.
- С водяным охлаждением – оснащены системой циркуляции охлаждающей жидкости, которая предотвращает перегрев при продолжительной работе. Такие горелки используют при интенсивной эксплуатации и на толстых металлах, где требуется высокая температура дуги.
Горелка полуавтоматической сварки требует регулярной замены и обслуживания ряда расходных материалов, от которых зависит качество сварочного процесса и долговечность самого устройства.
Контактный наконечник – элемент горелки, через который проходит сварочная проволока. Передает ток на проволоку и отвечает за стабильность дуги. В процессе сварки контактный наконечник постепенно изнашивается и загрязняется, снижая качество процесса. Его меняют по мере износа, особенно при интенсивной эксплуатации. Выбор зависит от диаметра используемой проволоки. Обычно используется медь, так как она обладает хорошей проводимостью и термостойкостью, но для определенных задач применяются и сплавы с улучшенной износостойкостью.
Другая расходная часть горелки – сопло. Направляет защитный газ к сварочной ванне, предотвращая попадание кислорода и защиту зоны сварки. Неправильно подобранное или загрязненное, способно привести к нарушению подачи газа и снижению качества шва.
Обычно используют сопла из меди или латунных сплавов, устойчивые к нагреву. Также применяют керамические сопла, особенно при высоких температурах и интенсивных работах.
Данные элементы подвержены загрязнению брызгами металла и шлака, поэтому их нужно регулярно чистить с помощью специальных аэрозолей и щеток.
Также внимание на ролики подачи проволоки – отвечают за равномерное движение проволоки через горелку. Качество работы роликов напрямую влияет на стабильность подачи и, соответственно, на стабильность дуги.
Ролики подбираются в зависимости от диаметра и типа используемой проволоки. При изменении диаметра проволоки следует заменить и ролики. Они также загрязняются и изнашиваются, из-за чего ухудшается подача присадки. Регулярная чистка и своевременная замена в данном случае помогают поддерживать стабильную работу.
Еще важная составляющая – диффузор, отвечает за равномерное распределение защитного газа по всей площади сварочной ванны. От правильной работы диффузора зависит качество защиты сварного шва от окружающего воздуха.
Данный компонент со временем засоряется и изнашивается, потому нуждается в периодической проверке и замене. Диффузоры нужно очищать от брызг металла и других загрязнений, чтобы поток газа был равномерным.
Горелка полуавтоматической сварки и ее расходные материалы – составляющие, от которых зависит качество и эффективность сварочного процесса. Контактные наконечники, сопла, ролики подачи проволоки и диффузоры требуют регулярной замены и обслуживания, чтобы обеспечить стабильную работу горелки и качество сварных швов. Внимательное отношение к выбору и состоянию расходников позволяет снизить риск неисправностей, упростить процесс работы и повысить результативность сварки.
Защитный газ
В полуавтоматической сварке дуга плавит металл и сварочную проволоку, создавая сварочную ванну. Открытый воздух содержит кислород и водяной пар, которые окисляют металл и ухудшают качество соединения. Защитный газ, подаваемый через сопло, создает барьер между сварочной ванной и воздухом, минимизируя контакт металла с кислородом и азотом. Это позволяет:
- Предотвратить образование пор и окислов, ослабляющих сварной шов.
- Поддерживать стабильность сварочной дуги и защищать от вредных воздействий атмосферы.
- Уменьшить разбрызгивание металла и, следовательно, необходимость последующей обработки шва.
Углекислый газ – наиболее распространенный для стали и низколегированных сплавов. Хорошо себя зарекомендовал для сварки черных металлов и менее требовательных задач, где важна экономичность, а не высочайшая прочность шва.
Аргон – инертный газ, создающий отличную защиту сварочной ванны. Он не вступает в химические реакции с металлом и широко применяется для сварки легированных сталей, алюминия и меди.
Комбинация аргона с CO₂ популярна для сварки сталей и низколегированных металлов. Смесь помогает сбалансировать преимущества обоих сред. Наиболее распространенные пропорции – 80% аргона и 20% CO₂ или 90% аргона и 10% CO₂. Такие смеси используют для сварки черных металлов и низколегированных сталей, где на первом месте качество шва и скорость работы.
В некоторых случаях к смеси аргона и CO₂ добавляют небольшое количество кислорода, обычно 1-5%, чтобы улучшить качество и стабильность дуги.
Оптимальный расход газа зависит от диаметра проволоки, скорости подачи и типа используемого газа. Чаще всего расход регулируется в пределах 10-20 л/мин, но может быть выше или ниже в зависимости от конкретных условий сварки.
Кабель-шланговый пакет
Соединяет сварочный аппарат с горелкой и служит для передачи всех необходимых для сварки элементов. В одном пакете объединены сразу несколько важных функций:
- Передача электрического тока – для создания сварочной дуги, благодаря которой происходит расплавление металла и сварочной проволоки.
- Подача защитного газа – для защиты сварочной ванны от воздействия кислорода и образования окислов.
- Подача сварочной проволоки – проволока движется по специальному каналу внутри кабельного пакета и подается к контактному наконечнику горелки.
- Система охлаждения (при наличии водяного охлаждения) – некоторые пакеты имеют шланги для подачи и отвода охлаждающей жидкости, предотвращающие перегрев горелки при интенсивных сварочных работах.
Все эти функции объединены в один гибкий кабель, что облегчает использование аппарата и делает процесс надежным.
Стандартный кабель-шланговый пакет включает несколько элементов, каждый из которых выполняет свою функцию. Вот основные из них:
- Токопроводящий кабель – проводит электрический ток от источника к горелке. Этот кабель должен обладать хорошей токопроводимостью и быть надежно изолирован.
- Шланг для подачи газа – канал подачи защитного газа, обычно выполнен из износостойкого материала, устойчивого к воздействию сварочной температуры.
- Подающий канал для сварочной проволоки – канал, по которому проволока движется к горелке. В зависимости от модели аппарата и типа проволоки, канал может быть гибким или жестким.
- Шланги для охлаждающей жидкости – для систем с водяным охлаждением предусмотрены отдельные шланги для подачи и отвода охлаждающей жидкости. Такая система сохраняет стабильность температуры горелки при интенсивных сварочных работах.
- Оболочка – внешний слой, защищающий внутренние элементы пакета от механических повреждений, влаги и перегрева.
Кабель-шланговые пакеты с воздушным охлаждением – наиболее распространенный тип кабелей, предназначенный для сварочных работ средней интенсивности. Охлаждение осуществляется за счет окружающего воздуха, поэтому они обычно имеют меньшую массу и более простую конструкцию.
Для интенсивных и продолжительных сварочных работ используются кабели с водяным охлаждением. Они оснащены каналами циркуляции охлаждающей жидкости, поддерживающими постоянную температуру, не допускают перегрева горелки.
Выбор кабель-шлангового пакета зависит от условий эксплуатации и типа сварочного оборудования. Вот несколько ключевых факторов, которые следует учитывать:
- Интенсивность и продолжительность работы – для длительных и интенсивных сварок лучше выбрать пакеты с водяным охлаждением, тогда как для менее нагруженных работ подойдут кабели с воздушным охлаждением.
- Тип металла и сварочного тока – чем толще металл и выше ток, тем больше нагрузка на пакет, особенно на токопроводящий кабель.
- Диаметр сварочной проволоки – пакет должен поддерживать нужный диаметр канала для плавной подачи проволоки без застреваний.
- Длина пакета – подбирается с учетом расстояния между сварочным аппаратом и рабочей зоной, при этом не стоит выбирать слишком длинный кабель, так как это увеличивает сопротивление и снижает токопроводимость.
Кабель-шланговый пакет – многофункциональный элемент, от которого зависит стабильность подачи тока, газа и проволоки к горелке. Правильный выбор с учетом условий эксплуатации, регулярное обслуживание и своевременная замена изношенных элементов позволяют продлить срок службы пакета и обеспечить высокое качество сварочных работ. Внимание к состоянию способствует минимизации простоя и повышению эффективности сварочного процесса.
Что еще понадобится
Средства очистки – сварочное оборудование нуждается в регулярной очистке, чтобы предотвратить скопления брызг и загрязнений, которые ухудшают качество сварки и уменьшают срок службы всех компонентов. Сюда относятся специальные аэрозоли и пасты для очистки горелок и сопел от металлических отложений.
Конечно же, понадобятся сварочные маски и щитки для защиты глаз и лица от яркой дуги и раскаленных брызг; перчатки и спецодежда – защита кожи от ожогов и других повреждений. Сварочные магниты и зажимы – применяются для удобной фиксации деталей перед процессом, особенно при работе с крупногабаритными конструкциями. Подставки для сварочной проволоки – обеспечивают удобное размещение и подачу проволоки, особенно при использовании крупных катушек.
Полуавтоматическая сварка требует надежного и качественного оборудования, а также своевременной замены расходных материалов для стабильности и качества сварочного процесса. Выбор правильного оборудования и расходных материалов – увеличение производительности, улучшение качество шва и сокращение затрат на обслуживание. Также безопасность процесса. Точно не стоит этим пренебрегать!
Подготовка
Подготовка к сварке проволокой – это важный этап, от которого во многом зависит качество сварочного шва, стабильность процесса и долговечность готового соединения.
Полуавтоматическая сварка выполняется с помощью аппаратов MIG/MAG, работающих в среде защитных газов. Важно подобрать аппарат, соответствующий требованиям конкретного сварочного задания: его мощность и диапазон настроек должны быть достаточными для работы с материалом нужной толщины и типа. Современные аппараты позволяют точно регулировать основные параметры – ток, напряжение и скорость подачи проволоки, гибко настраивать процесс.
Выбор защитного газа зависит от материала, с которым предстоит работать. Для сварки стали часто используется углекислый газ (CO₂) или его смесь с аргоном. Для алюминия и других цветных металлов лучше подходит чистый аргон. Газ подается из баллона с редуктором, который регулирует давление и расход. Перед началом сварки важно проверить целостность шлангов и всех соединений, чтобы избежать утечки и сохранить стабильность газовой защиты.
Сварочная проволока также подбирается в зависимости от материала свариваемых деталей. Для работы с нержавеющей, углеродистой сталью и алюминием нужны разные типы присадки, каждая из которых обладает своими характеристиками по составу и диаметру. Проволоку лучше заправлять перед началом работы, следя за тем, чтобы катушка была установлена ровно, а натяжение проволоки соответствовало требованиям аппарата.
Организация пространства
Рабочая зона должна быть безопасной, чистой и хорошо освещенной. Уберите из зоны сварки все легковоспламеняющиеся материалы и предметы, чтобы минимизировать риск пожара. Важно, чтобы рабочее место было оборудовано вытяжкой или хорошо вентилируемым, так как во время сварки выделяются дым и газовые пары.
Инструменты
Для полуавтоматической сварки потребуется ряд вспомогательных инструментов, среди которых:
- Зажимы и струбцины для надежной фиксации деталей.
- Сварочные магниты для правильного позиционирования заготовок.
- Металлические щетки и абразивы для очистки поверхности перед сваркой.
Стоит подготовить сварочную маску, защитные перчатки и спецодежду. Сварочная маска защищает глаза и лицо от яркой дуги, а перчатки и одежда – от искр и высоких температур.
Заготовки
Перед сваркой детали необходимо тщательно очистить. Наличие ржавчины, масла, краски или грязи на поверхности металла приводит к ухудшению качества шва и дефектам в виде пор и трещин. Для очистки можно использовать металлические щетки, абразивные круги или растворители. Особое внимание стоит уделить краям и зонам, где будет происходить соединение, так как именно там проходит основная часть сварочного процесса.
После механической очистки поверхности рекомендуется дополнительно обезжирить, чтобы убрать остатки масел и других загрязнений. Для этого можно использовать ацетон или специальные обезжиривающие средства. Это особенно важно при работе с цветными металлами, алюминием, который сильно подвержен окислению.
Подгонка и фиксация
Перед началом сварки заготовки нужно правильно позиционировать и зафиксировать. Это можно сделать с помощью зажимов, магнитов или струбцин, они предотвратят смещение деталей во время процесса. Края заготовок следует расположить так, чтобы между ними был зазор, соответствующий требованиям для выбранного типа сварки. Это даст лучшее проплавление и качественный шов.
Настройка сварочных параметров
Настройка параметров сварки – один из важнейших этапов, так как от него зависит качество и надежность соединения.
Сила тока и напряжение – это базовые параметры, от которых зависит плавление проволоки и формирование сварочной ванны. Правильно подобранные значения позволяют получить ровный шов без прожогов и пор. Настройка зависит от таких факторов, как толщина металла, его тип и диаметр используемой проволоки.
Вот основные рекомендации по их настройке:
- Толщина металла – чем толще металл, тем выше должно быть значение тока и напряжения. Для тонких листов обычно требуется низкий ток, чтобы избежать прожогов, а для более толстых – повышенный.
- Диаметр проволоки – увеличенный диаметр требует повышения силы тока для стабильного плавления. Например, для проволоки диаметром 0,8 мм требуется меньший ток, чем для проволоки диаметром 1,2 мм.
- Тип материала – разные материалы – сталь, алюминий или нержавеющая сталь – имеют разную теплопроводность. Например, алюминий быстрее рассеивает тепло, поэтому при его сварке требуется больший ток по сравнению со сталью той же толщины.
Для сварки стали толщиной 3 мм с использованием проволоки диаметром 0,8 мм сила тока обычно составляет около 100-120 ампер, напряжение – 18-20 вольт.
Для алюминия того же диаметра проволоки и толщины металла может потребоваться сила тока около 140-160 ампер и напряжение около 20-22 вольт.
Настройки можно постепенно корректировать, наблюдая за сварочной ванной: слишком низкие значения приведут к недостаточному проплавлению, а слишком высокие вызовут прожоги и разбрызгивание металла.
Скорость подачи проволоки должна синхронизироваться с силой тока. Если скорость подачи слишком низкая для заданного тока, проволока будет плавиться слишком быстро, что приведет к нестабильности дуги. При избыточной скорости подачи проволока будет «давить» на шов, и сварка станет прерывистой.
Для тонких материалов требуется меньшая скорость подачи, чтобы проволока успевала плавиться, не вызывая прожогов.
Некоторые аппараты имеют режимы автоматической синхронизации подачи проволоки с током. В этом случае скорость подачи настраивается автоматически в зависимости от установленного тока.
При ручной настройке важно следить за звуком и визуальными характеристиками дуги. Если сварка идет с правильной скоростью подачи, звук будет похож на ровное шипение без «прострелов».
Для проволоки диаметром 0,8 мм и тока 100-120 ампер скорость подачи обычно составляет 3-5 метров в минуту. Для проволоки диаметром 1,2 мм и тока 150-200 ампер скорость подачи может быть увеличена до 7-10 метров в минуту.
Расход защитного газа зависит от условий сварки и внешних факторов: ветер или наличие сквозняков. Неправильная подача может привести к появлению пор и дефектов на шве.
Углекислый газ (CO₂) обычно подается с расходом 10-12 л/мин, а смеси аргона с CO₂ – около 15-20 л/мин, так как аргон более легкий и требует немного большего потока для создания эффективной защиты.
Если сварка выполняется на открытом воздухе или в условиях сильного сквозняка, расход газа увеличивается для создания стабильного потока, защищающего сварочную ванну от воздуха.
Больший диаметр сопла требует большего расхода газа для полного покрытия зоны сварки.
Для сварки углеродистой стали с использованием углекислого газа обычно устанавливают расход 12-15 л/мин. При сварке в смеси аргона и CO₂ расход может достигать 15-20 л/мин. На открытом воздухе этот параметр иногда увеличивают до 20-25 л/мин для предотвращения выдувания газа.
Дополнительные рекомендации по настройке
Современные сварочные аппараты часто оснащены таблицами или встроенными рекомендациями, которые помогают подобрать оптимальные параметры сварки в зависимости от толщины металла и типа проволоки. Эти таблицы обычно располагаются на корпусе аппарата или в его инструкции и позволяют быстро сориентироваться с выбором настроек.
Перед началом основной сварки рекомендуется сделать тестовый шов на образце материала. Это помогает не только проверить точность настройки, но и убедиться в стабильности подачи проволоки, достаточном расходе газа и отсутствии дефектов на поверхности.
Иногда в процессе сварки приходится корректировать параметры в зависимости от изменений толщины металла, типа соединения или положения шва. Если шов становится слишком выпуклым или пористым, стоит проверить настройки газа и снизить ток, а если шов недостаточно проплавлен – увеличить напряжение и подачу проволоки.
Правильная настройка параметров сварки – основа успешного сварочного процесса. Оптимальные значения тока, напряжения, скорости подачи проволоки и расхода защитного газа помогают достичь прочного, ровного и бездефектного шва. Точная настройка этих параметров требует не только знания материала и оборудования, но и практического опыта, тогда работа будет максимально качественной и безопасной.
Проверка оборудования
Проверка сварочного полуавтомата перед началом работы – это обязательный этап, который позволяет предотвратить возможные проблемы, обеспечить стабильность сварочного процесса и качество шва.
Первый шаг здесь – это визуальный осмотр. Внешние признаки неисправности могут указывать на необходимость ремонта или замены некоторых компонентов.
Корпус аппарата и кабели должны быть целыми, без повреждений, которые могут вызвать короткое замыкание или ухудшить качество подачи тока. Особое внимание стоит уделить изоляции проводов, так как нарушение может привести к поражению электрическим током.
Осмотр вентиляционных отверстий – они должны быть свободными от пыли и загрязнений, так как вентилятор защищает аппарат от перегрева. Забитая вентиляция снижает производительность и приводит к перегреву.
Контроль соединений и креплений – нужно убедиться, что все элементы аппарата надежно закреплены, особенно при работе на строительных площадках или в условиях, где оборудование часто транспортируется.
Другая составляющая, требующая контроля, – механизм подачи проволоки. Важнейший элемент полуавтомата, от которого зависит стабильность подачи присадочного материала и качество сварочного шва. Вот основные шаги его проверки:
- Осмотр катушки с проволокой – катушка должна быть правильно установлена, без излишнего натяжения или перекоса. Неправильно установленная, может привести к перебоям в подаче.
- Проверка подачи присадки – включите аппарат на короткое время и проверьте, как подается проволока в горелку. Если подача происходит рывками или проволока застревает, возможно, требуется очистить или заменить ролики.
- Регулировка прижима роликов – проволока должна подаваться плавно, без проскальзывания и рывков. Слишком сильный прижим может привести к деформации проволоки, а слишком слабый – к ее пробуксовке.
Регулярная проверка подачи проволоки помогает избежать сбоев, особенно при работе с тонкими материалами, где критична стабильность движения.
Проверка горелки
Горелка и сопла играют важную роль в подаче защитного газа и правильном формирования дуги. Основные шаги для их проверки:
- Контактный наконечник – его нужно осмотреть на предмет износа или загрязнений, так как от него зависит качество передачи тока на проволоку. При необходимости контактный наконечник меняют на новый.
- Сопло – убедитесь, что сопло чистое и не забито шлаком или металлическими брызгами, так как нарушается подача защитного газа. Для очистки сопла используют специальные аэрозоли или щетки.
- Проверка целостности кабеля горелки – на кабеле не должно быть трещин или заломов. Поврежденный кабель способен нарушить подачу газа или вызвать перебои в передаче тока.
Регулярная очистка и контроль состояния горелки помогают реализовать равномерную подачу газа и защиту зоны сварки от окружающей среды.
Система подачи защитного газа
Инертный или активный газ защищает сварочную ванну от кислорода, предотвращая образование оксидов и пор.
Убедитесь, что газовый баллон зафиксирован надежно и находится в вертикальном положении. Проверьте, что на баллоне достаточно газа для выполнения задачи.
Проверьте, чтобы регулятор давления был исправен и правильно настроен. Показатели давления должны соответствовать параметрам, указанным для конкретного газа (обычно 10-20 л/мин).
Осмотрите шланги на предмет возможных утечек. Для этого можно нанести мыльный раствор на соединения – появление пузырьков укажет на утечку, которую следует устранить.
Правильно настроенный расход газа – надежная защита сварочной ванны, предотвращение дефектов шва.
Тестовый шов
Перед началом основной сварки рекомендуется сделать тестовый шов на образце материала. Чтобы выявить возможные проблемы с настройкой и убедиться в правильности параметров. Обратите внимание на звук дуги. При правильной настройке сварка идет плавно, без «прострелов» и перебоев.
Качественный шов должен быть ровным, без пор, прожогов или пропусков. Если заметны дефекты, скорректируйте параметры и повторите тест.
Формирование шва
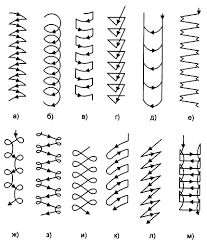
Сварка металлов при помощи проволоки и в среде защитных газов стала одной из самых популярных в различных отраслях благодаря своей производительности, возможности выполнять длинные соединения без частых прерываний, скорости и высокой прочности соединений. Реализуется путем подачи электрода в виде проволоки и защиты сварочной ванны с помощью инертного или активного газа. MIG-сварка используется для материалов, склонных к окислению, и предполагает использование инертных газов (например, аргона), в то время как MAG применяется в работе с углеродистыми сталями и использует активные газы (углекислота или смесь углекислоты и аргона).
Очистка поверхности и настройка
Перед тем как приступить к выполнению шва, необходимо провести подготовительные работы.
Убедитесь в чистоте и безопасности рабочего места. Удалите все воспламеняющиеся материалы и предметы, которые могут мешать процессу.
Проверьте вентиляцию. Поскольку сварка сопровождается выделением вредных газов и дыма, необходимо наладить хорошую вентиляцию или использовать вытяжное оборудование.
Подготовьте защитные средства. Используйте сварочную маску с подходящим уровнем затемнения, огнеупорную одежду, перчатки и обувь с металлическими вставками для защиты от искр.
Очистка поверхности – удалите ржавчину, грязь, краску и масло с кромок и вокруг места сварки.
Правильная настройка оборудования – выберите подходящий режим тока, тип и диаметр проволоки, исходя из толщины металла и типа соединения.
Настройка подачи проволоки и газа – оптимальные параметры подачи зависят от толщины проволоки и характеристик металла, а также типа защитной среды. Об этом мы говорили выше.
Прежде чем включить сварочный аппарат, важно убедиться в наличии и правильной установке расходных материалов.
Проверьте тип проволоки. Выберите проволоку, подходящую для материала, с которым вы будете работать. Например, для стали используется углеродистая проволока, а для алюминия – алюминиевая.
Установите катушку с проволокой. Катушку нужно вставить в аппарат и закрепить, чтобы предотвратить случайное раскручивание.
Настройте систему подачи присадки. Протяните проволоку через рукав до сопла горелки, отрегулируйте механизм подачи, чтобы он работал плавно и без рывков.
Включение аппарата
После установки проволоки можно подключить аппарат к источнику питания и газовому баллону.
Подключите аппарат к сети. Убедитесь, что напряжение сети соответствует параметрам источника электродуги.
Подключите газовый баллон. Присоедините редуктор к баллону и подключите газовый шланг от аппарата к редуктору.
Откройте вентиль баллона и отрегулируйте давление газа на редукторе. Оптимальный расход газа зависит от толщины металла, скорости сварки и типа используемой среды. Обычно составляет от 8 до 15 литров в минуту.
Перед началом рекомендуется проверить работу подачи проволоки и системы защиты газом.
Нажмите на курок горелки и убедитесь, что проволока выходит стабильно, без рывков.
При нажатии курка газа должно быть достаточно для формирования защитного облака вокруг сварочной ванны.
Перед началом основной сварки рекомендуется провести пробный шов на тестовом образце того же материала, чтобы оценить, подходят ли параметры.
Техника ведения шва
Когда все проверки пройдены и параметры настроены, можно начинать сварку.
Займите удобное положение и удерживайте горелку под углом 10–20 градусов к поверхности металла.
Сформируйте сварочную ванну. Нажмите на курок, чтобы зажечь дугу и сформировать сварочную ванну.
Перемещайте горелку вдоль шва. Постепенно двигайте горелку вдоль линии шва, стараясь поддерживать равномерное расстояние между соплом и металлом и контролировать ширину сварочной ванны.
Скорость перемещения горелки должна быть стабильной. Слишком медленное движение приведет к перегреву и разбрызгиванию металла, слишком быстрое – к недостаточному проплавлению и слабому шву.
Основные направления, по которым может выполняться шов, включают:
- Прямолинейное движение. Используется для создания ровных и аккуратных швов. Сварщик ведет сварочную горелку равномерно, прямо вдоль линии шва. Эта техника предпочтительна для сварки металлов средней и большой толщины, когда требуется глубокое проплавление.
- Зигзагообразное движение. Применяется для более равномерного распределения тепла, улучшения качества соединения и предотвращения прожогов. В этом случае сварщик движется зигзагами или полукругами, так снижается концентрация тепла и улучшается контроль процесса.
- Круговое движение. Сварщик ведет горелку круговыми движениями. Эта техника помогает создать более широкий шов и применяется при работе с толщинами от 3 мм, когда требуется хорошая заполняемость и качественное соединение.
Угол наклона сварочной горелки является одним из важнейших факторов при ведении шва. Оптимальный – 10–20 градусов к направлению шва. В зависимости от типа соединения и толщины металла угол может варьироваться, чтобы улучшить контроль над формой и глубиной шва.
Для начала сформируйте сварочную ванну, создав стабильную дугу.
Постепенно перемещайте сварочную горелку по линии шва, поддерживая равномерное расстояние между соплом и металлом.
Скорость перемещения горелки должна быть стабильной, поскольку она влияет на ширину и высоту шва.
Регулируйте расстояние между наконечником и поверхностью металла, чтобы избежать «разрывов» дуги или перегрева материала.
Заканчивайте шов аккуратно, избегая резких остановок, чтобы предотвратить образование кратеров и слабых точек.
Завершение
Завершение сварки проволокой – один из ключевых этапов, который влияет на качество шва и устойчивость сварочной конструкции. Ошибки в данном случае могут привести к дефектам, например, пористости, трещинам, недоплавам и прочим проблемам, которые снижают прочность и долговечность сварного соединения.
Завершение процесса должно выполняться максимально аккуратно, так как на финальном этапе металл часто подвержен неравномерному остыванию. Это может привести к кратерам и, как следствие, к дальнейшему образованию микротрещин. Остановка должна происходить плавно, без резких прекращений подачи тока и движений проволоки. Основной принцип – контроль подачи проволоки и удержание стабильной дуги до момента полного закрытия сварочной ванны.
Типичные ошибки при завершении шва
Резкое прекращение подачи проволоки – приводит к образованию полостей и снижению прочности соединения.
Недостаточная температура сварочной ванны – быстрое охлаждение может вызвать напряжение в зоне окончания сварки.
Недостаточная защита газом – особенно актуально при работе с нержавеющей сталью, алюминием и другими материалами, склонными к окислению.
Для предотвращения возникновения кратера в конце шва рекомендуется снижать подачу тока перед полным окончанием сварки. Это можно сделать либо вручную, либо при помощи автоматических настроек, если ваш сварочный аппарат имеет такую функцию. Постепенное снижение тока позволяет избежать образования кратера и более гладко перейти на окончание шва.
Закрытие сварочной ванны
Закрытие сварочной ванны подразумевает плавное завершение процесса, при котором сварочная проволока продолжает подачу в кратер, образующийся в конце шва. Для этого:
- Слегка отведите горелку назад – поможет плавно уменьшить температуру и скорость подачи проволоки.
- Прекратите подачу присадки, когда ванна полностью затекла. Важно, чтобы в кратере не оставалось пустот или воздушных пузырей, так как это может ослабить шов.
Следите за длиной дуги. Она должна быть чуть короче, чем при основной сварке, чтобы гарантировать стабильное плавление и меньшую подверженность кратеров образованию трещин. Оптимальная длина – равномерное расплавление металла на последнем этапе.
Метод обратного движения подразумевает временное возвращение назад по шву перед завершением сварки. Чтобы распределить тепло и уменьшить напряжение на финишном участке шва. Полезен для толстых металлов, где тепловые напряжения более выражены.
Газовая защита играет ключевую роль в предотвращении окисления и загрязнений. На финальном этапе, когда уменьшается скорость подачи тока, нужно сохранить подачу газа, чтобы шов не подвергался воздействию кислорода. Актуально при сварке алюминия и нержавеющей стали.
Убедитесь, что вы выбрали оптимальные параметры сварки – ток, скорость подачи проволоки и тип защитного газа. Оцените толщину и тип металла, так как для более толстых материалов может потребоваться увеличенный расход газа на окончание.
Значимость правильного завершения
Качественное завершение сварочного процесса влияет на целостность и долговечность шва. Соблюдение техник плавного снижения тока, правильное закрытие сварочной ванны, поддержание оптимальной длины дуги, отвод горелки назад и контроль газовой защиты – все это обеспечивает отсутствие дефектов и высокое качество соединения. Завершая шов правильно, сварщик добивается более устойчивой конструкции и предотвращает образование дефектов, которые могут повлиять на срок службы изделия.
Правильное завершение сварки – это не только вопрос техники, но и опыта, знания особенностей оборудования и материалов, с которыми идет работа.
Роль проволоки в полуавтоматическом процессе
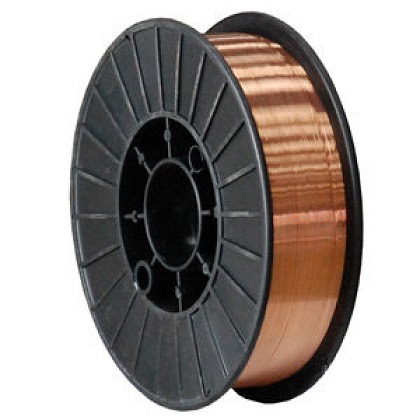
Подводя итог, проволока выступает электродом при полуавтоматической сварке. От нее напрямую зависят качество и долговечность сварного шва, устойчивость соединения к коррозии, механическая прочность и общая надежность конструкции. Таким образом, выполняет сразу несколько функций:
- Подача тока. Проволока – электропроводный элемент, по которому подается ток от сварочного аппарата к зоне соединения. Прокладывая путь для электрического разряда, проволока способствует образованию сварочной дуги и дает необходимую температуру плавления металла.
- Образование сварочного шва – проволока плавится под воздействием электрической дуги, превращаясь в жидкий металл. Создает прочное соединение с основным металлом, формируя целостный сварной шов. Не просто выступает связующим элементом, но и гарантирует высокую прочность полученного соединения.
- Стабилизация дуги. Правильно подобранная проволока помогает удерживать устойчивое горение дуги, минимизирует разбрызгивание металла, улучшает качество шва и сокращает последующую обработку. От стабильности дуги зависит точность сварного соединения и аккуратность работы.
- Предотвращение окисления. При сварке порошковой проволокой металл защищает от окисления флюс в сердечнике присадки, который не дает кислороду и другим газам взаимодействовать с расплавленным металлом. При использовании обычной проволоки защитная функция выполняется газовой средой, подаваемой из внешнего источника, – чаще всего это инертные или активные газы (аргон, углекислый газ и их смеси).
Качественное соединение деталей из алюминия, нержавейки, меди или чугуна – без проволоки не обойтись. Играет важнейшую роль в полуавтоматической сварке, работая на качество и надежность соединений. Выбрав подходящую присадку, не только улучшают качество шва, но и снижают затраты на сварку за счет снижение количества брака и уменьшения трудозатрат. Каждая деталь – тип, состав и диаметр проволоки – имеет значение, и грамотное их сочетание дает отличные результаты даже при сложных сварочных операциях!
Заключение
Сварочная проволока играет центральную роль в процессе полуавтоматической сварки, обеспечивая плавное и равномерное соединение металлов. Грамотный выбор марки и типа, а также соблюдение рекомендаций по подготовке и технике безопасности, помогают добиться качественного, прочного и долговечного шва. Разные виды присадок позволяют адаптировать сварку под конкретные требования – от свойств материала до условий эксплуатации готового изделия.
Каждый аспект сварочного процесса, будь то выбор расходных материалов или настройка оборудования, влияет на конечный результат. Правильная подготовка поверхностей, выбор оборудования и техники выполнения шва сокращают риск дефектов и повышают прочность соединений. Сварочная проволока выступает не только связующим материалом, но и фактором, влияющим на точность и производительность.
Сварка проволокой – универсальный и эффективный метод, который становится основой для надежных конструкций в различных отраслях. Благодаря своим особенностям – качественное соединение нержавейки и алюминия, продолжительность, точность, удобство – продолжает оставаться востребованной и выступает важным инструментом в арсенале профессионалов. Там, где обычная РДС не даст результат, всегда поможет проволока!