Режимы сварки
Без металла не обходится наша жизнь, а соответственно, в производственных процессах активно задействуется сварка. Это сложный технологическая операция, требующая точного контроля параметров – сила тока, напряжения, скорости и других факторов, которые напрямую влияют на качество соединения. Для достижения оптимального результата необходимо соблюдать определенные режимы, которые варьируются в зависимости от типа металла, метода и условий работы. Рассмотрим основные режимы сварки металла и их влияние на сварочный процесс в целом.
Содержание:
Что такое сварочный режим
Сварка металлов – это один из ключевых процессов в машиностроении, строительстве, производстве и других отраслях, где требуется надежное и прочное соединение деталей. Успешное выполнение работ в данном случае зависит не только от мастерства сварщика, но и от правильного выбора режима, который напрямую влияет на результат. Различные металлы, методы и условия работы требуют индивидуальной настройки оборудования. Понимание того, как правильно настроить параметры режима сварки, становится критически важным для получения качественного шва и долговечности соединения.
Таким образом, сварочный режим – совокупность параметров, определяющих процесс сварки металла. Эти параметры напрямую влияют на качество, прочность и внешний вид сварного шва. Каждый сварочный режим подбирается индивидуально в зависимости от типа металла, метода сварки, толщины деталей и других условий. Грамотный выбор режимов сварки – залог успешного проведения работ и получения качественного соединения!
Основные режимы
Технологический процесс, при котором происходит соединение металлов посредством их нагрева и плавления. Чтобы успешно выполнять сварку, требуется точная настройка режима, который включает в себя различные параметры. Они разделяются на основные и второстепенные.
Основные режимы определяют ключевые характеристики сварочного процесса, тогда как второстепенные влияют на дополнительные аспекты: удобство выполнения работы или улучшение эстетических качеств шва.
Итак, основными режимами выступают:
- Сила тока. Основной параметр, влияющий на качество и скорость сварки.
- Диаметр электрода или проволоки. Подбирается в зависимости от толщины металла и типа сварки.
- Род тока. Используется постоянный или переменный ток, в зависимости от условий и типа сварочного аппарата.
- Полярность. Прямой или обратной полярности, в зависимости от требований сварочного процесса.
- Напряжение сварочной дуги и ее длина. Влияет на стабильность дуги и качество шва.
- Скорость сварки. Определяет производительность и влияет на качество сварочного соединения.
Сила тока, установленная на сварочном аппарате, напрямую влияет на температуру сварочной дуги и глубину проплавления. Слишком высокий ток может вызвать прожоги или избыточное расплавление металла, тогда как слишком низкий приведет к неполному проплавлению и слабому соединению.
Пример выбора режима сварки в данном случае:
- Для стали толщиной 3 мм оптимальный ток составляет 65-100 ампер.
- Для более толстых материалов ток увеличивается до 150-200 ампер.
Диаметр электрода (при РДС) или проволоки (использование защитных газов) также влияет на глубину проплавления и качество шва. Чем больше диаметр, тем больше должен быть сварочный ток, чтобы соединение получилось надежным.
Пример:
- Для электродов диаметром 3 мм используют ток в пределах 50-100 ампер.
- Для проволоки диаметром 1,2 мм при MIG-сварке требуется ток около 150-200 ампер.
Род тока – еще один важный параметр. В сварке используют два типа тока: постоянный и переменный. Постоянный (DC) дает более стабильное горение дуги и лучшее проплавление, тогда как переменный (AC) часто используется для алюминия и других цветных металлов, поскольку он предотвращает образование оксидных пленок.
Полярность – влияет на распределение тепла между электродом и свариваемой деталью при использовании постоянного тока. При прямой полярности (когда минус подключен к электроду) большая часть тепла сосредоточена на металле, что способствует лучшему проплавлению. При обратной – тепло концентрируется на электроде, помогая избежать перегрева детали, особенно при соединении тонких материалов.
Далее напряжение сварочной дуги. Этот режим влияет на стабильность электродуги и форму шва. Длина дуги должна быть оптимальной: слишком короткая может привести к нестабильному процессу и неравномерному шву, а слишком длинная – к разбрызгиванию металла и ухудшению качества соединения.
Скорость перемещения электрода вдоль свариваемого шва также выступает важным фактором. Медленная сварка может привести к перегреву металла и его деформации, а слишком быстрая – к недостаточному проплавлению. Оптимальная скорость способствует формированию равномерного шва с правильной глубиной проплавления и минимальными дефектами.
Второстепенные
Это параметры, которые не напрямую определяют физические характеристики сварки, но оказывают существенное влияние на удобство работы, внешний вид и долговечность сварного соединения. Их правильная настройка помогает предотвратить дефекты и улучшить эстетическое качество шва.
Итак, второстепенные режимы следующие:
- Чистота кромок свариваемых заготовок.
- Подготовка и разделка кромок.
- Расположение стыка.
- Вид электрода: марка, тип покрытия, толщина обмазки.
- Угол наклона электрода относительно сварочной поверхности.
- Положение электрода.
Чистота поверхности кромок свариваемых деталей играет важную роль в процессе сварки. Загрязнения – ржавчина, окалина, масло или грязь – вызывают дефекты шва, например, поры или включения. Поэтому важно тщательно очищать кромки перед сваркой, чтобы избежать снижения прочности соединения.
Подготовка кромок включает такие операции, как скос, притупление или ус соединяемых деталей. Это необходимо для достаточной глубины проплавления и улучшения качества шва. Разделка кромок особенно важна при сварке толстых металлов, так как она открывает доступ дуги к глубине соединения.
Положение стыка или свариваемого шва в пространстве – важный фактор, влияющий на удобство выполнения работы. Например, сварка в вертикальном или потолочном положении требует специальной настройки сварочного режима и более тщательной техники выполнения, чтобы избежать стекания расплавленного металла и образования дефектов.
Тип электрода, его марка и покрытие также влияют на характеристики сварочного процесса. Например, плавящиеся – состоят из металла (стали, чугуна, меди, бронзы, алюминия и т. д.) и могут быть катодом или анодом. Они одновременно проводят ток и заполняют место соединения материалом.
Неплавящиеся – изготовлены из неметаллического тугоплавкого материала – графита или вольфрама. Требуют подачи припоя в виде проволоки.
Электроды с покрытием – используются в ручной сварке и имеют покрытие, которое обеспечивает защитную среду, стабилизирует горение дуги и улучшает качество соединения.
Без покрытия – применяются в полуавтоматической и автоматической сварке в виде проволоки в среде защитной атмосферы.
Угол наклона электрода относительно свариваемой поверхности влияет на форму шва и равномерность его проплавления. Оптимальный угол – равномерное распределение тепла и металла вдоль шва. При неправильном угле возможно образование дефектов – выпуклые или вогнутые швы.
Положение электрода (верхнее, нижнее или боковое) определяет, как металл будет распределяться в сварочной ванне. Например, при нижнем положении сварка обычно проходит легче, а шов получается более аккуратным и ровным, тогда как при боковом или потолочном положении могут возникнуть сложности из-за стекания металла.
Основные и второстепенные режимы тесно взаимосвязаны и в совокупности определяют качество, прочность и долговечность сварного соединения. Основные параметры – сила тока, диаметр электрода, напряжение и скорость сварки – задают физические характеристики процесса, обеспечивая прочное и надежное соединение. Второстепенные параметры, в свою очередь, влияют на подготовку и удобство выполнения сварочных работ, а также на внешний вид шва. Для получения качественного сварного соединения важно учитывать оба типа параметров и тщательно настраивать режим сварки в зависимости от условий работы и типа металла.
Ручная дуговая сварка
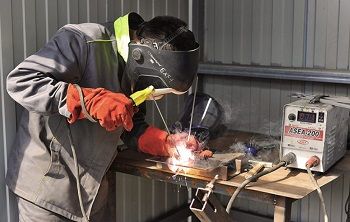
Пожалуй, самая распространенная и доступная – РДС, ручная дуговая сварка. Требует настройки ряда параметров, которые определяют, как именно будет проходить процесс. Эти параметры:
- Сила тока и тип тока.
- Полярность.
- Скорость движения электрода.
- Размер электрода.
- Напряжение дуги.
Кроме того, есть дополнительные режимы дуговой сварки, что также влияют на процесс. Это толщина материала, особенности разделки кромок, количество сварочных проходов и положение деталей в пространстве. Если неправильно установить режим сварки, возможны дефекты: слабый провар, прожог, неравномерность шва, снижение прочности и герметичности соединения.
Мы об этих параметрах сказали выше, здесь же подробнее разберем выбор диаметра электрода.
Классические с покрытием выпускаются диаметром 1,6, 2, 3, 4, 5 и 6 мм. Для более толстых заготовок следует использовать электроды с большим диаметром. Если пытаться сваривать массивные детали тонкими стержнями, они будут перегреваться и разрушатся еще до того, как произойдет формирование шва. Также может перегреться и осыпаться покрытие электрода, что приведет к тому, что сварочная ванна останется незащищенной, и в шве появятся поры.
Слишком толстые стержни, наоборот, могут мешать нормальной работе дуги, снижая ее стабильность. В таком случае сварщику будет сложно управлять процессом из-за маленького зазора, что приведет к частому прилипанию электрода к металлу.
Для успешной ручной дуговой сварки важно правильно подбирать диаметр электрода и силу тока в зависимости от толщины свариваемых заготовок. Например, для тонких изделий толщиной 1 мм подойдет электрод диаметром 1,5 мм при силе тока 25-40 А.
Для более толстого материала в 2 мм используют электрод 2 мм и силу тока 60-80 А.
Когда толщина достигает 3 мм, рекомендуется электрод диаметром 3 мм и ток в пределах 100-140 А.
Для заготовок толщиной 4 мм используют тот же диаметр электрода (3 мм), но увеличивают ток до 120-150 А.
Если толщина составляет 5 мм, то электрод выбирается 4 мм с силой тока 150-200 А.
А для сварки деталей толщиной 6-10 мм подойдет электрод диаметром 5 мм, при этом ток должен находиться в диапазоне 230-300 А.
Сварка проволокой
Это полуавтоматическая сварка, когда вместо электрода с покрытием – проволока, а зону электродуги и расплава металла защищает газовый купол. Проволока подается автоматически, а управляет дугой и формирует шов сварщик вручную. Поэтому и процесс так назвали – полуавтоматический.
В зависимости от типа защитного газа, различают два режима: MIG (с использованием инертных газов, например, аргона) и MAG (с активными газами, например, углекислым или смесями). Эти режимы позволяют эффективно соединять различные материалы – сталь, алюминий, нержавейку, а также отличаются точностью и высоким качеством швов.
Для понимания режимов MIG/MAG важно разобраться с ключевыми параметрами, которые определяют процесс:
- Сила тока – количество тепла, выделяемого дугой. Чем выше ток, тем больше тепловой энергии, что влияет на скорость плавления электродной проволоки и глубину провара.
- Напряжение дуги – регулирует длину дуги, которая оказывает влияние на стабильность процесса и ширину шва.
- Скорость подачи проволоки – один из ключевых параметров, влияющих на характер формирования шва и производительность процесса.
- Скорость сварки – определяет качество и размер шва, а также контролирует риск перегрева материала.
- Выбор защитного газа – в зависимости от того, используется инертный или активный газ, режимы сварки могут существенно отличаться по своим характеристикам.
Есть разные режимы сварки полуавтоматом, которые относятся к переносу металла через электродугу.
Представим следующие:
- Капельный перенос (Spray Transfer) – характерен для средних и высоких токов, когда жидкий металл переносится в виде мелких капель. Этот режим используется для толстых материалов и обеспечивает хорошее качество шва, но требует высоких энергозатрат и сильного нагрева детали.
- Шариковый перенос (Globular Transfer) – металл переносится через дугу в виде крупных капель. Этот режим менее стабильный и чаще используется при сварке с углекислым газом (MAG). Качество шва обычно ниже, и наблюдается повышенное разбрызгивание металла.
- Короткая дуга (Short Circuit Transfer) – происходит, когда проволока кратковременно касается поверхности материала, образуя короткое замыкание. Это один из наиболее экономичных режимов, который выделяется малой глубиной провара, подходит для тонких материалов и работы в различных пространственных положениях.
- Импульсный перенос (Pulsed Transfer) – задействуется при переменном токе, когда ток импульсно увеличивается, позволяя управлять процессом переноса металла с минимальными потерями на разбрызгивание. Результат – высокое качество швов даже на тонких материалах и управляемость процесса.
MIG-сварка применяется для работы с цветными металлами: алюминий, медь и магний. Использование инертных газов предотвращает окисление металла, что важно для работы с материалами, чувствительными к воздействию кислорода.
MAG-сварка широко используется для сварки углеродистых и низколегированных сталей, где за защиту сварочной ванны отвечает углекислый газ или его смеси с аргоном. Режим отличается высокой скоростью и экономичностью, но требует более тщательного контроля из-за возможности образования дефектов при неправильной настройке параметров.
Выбор газа играет ключевую роль в процессе MIG/MAG. Например, аргон обеспечивает стабильную дугу и высокое качество швов, но хуже подходит для толстых материалов, где требуется более глубокий провар. Углекислый газ или его смеси с аргоном (MAG-сварка) дают лучшую проникающую способность дуги, что важно для сварки стали, однако активные газы могут оказывать влияние на химический состав металла и вызывать образование пор или дефектов.
Режимы сварки MIG/MAG позволяют гибко настраивать процесс под конкретные задачи, что делает этот метод одним из наиболее универсальных и востребованных в промышленности. От выбора режима, параметров и типа защитного газа зависит не только качество шва, но и производительность процесса в целом. Важно правильно подобрать параметры для конкретного материала и условий работы, так удастся достичь стабильности процесса и долговечности сварных соединений.
Аргонодуговая
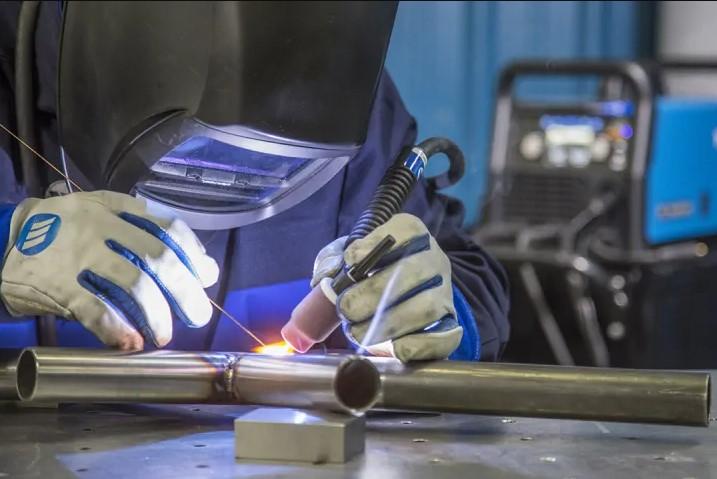
TIG-сварка (Tungsten Inert Gas) – аргонодуговая, представляет собой один из видов дуговой сварки, при котором используется неплавящийся вольфрамовый электрод и инертный газ – аргон – для защиты сварочной зоны от воздействия воздуха. Преимущества метода – высокая точность и качество сварки, потому популярен в авиационной, автомобильной и других отраслях, требующих соединения тонких и ответственных конструкций.
Суть процесса TIG заключается в создании электрической дуги между неплавящимся вольфрамовым электродом и свариваемым изделием. Для защиты сварочной зоны используется инертный газ (аргон или его смеси), который предотвращает окисление металла при высоких температурах. В некоторых случаях в процесс может вводиться присадочный материал (проволока), который добавляется для заполнения шва.
Основными параметрами режимов TIG выступают:
- Ток. Выбор между постоянным током (DC) и переменным (AC) является ключевым параметром, влияющим на процесс соединения различных металлов. DC используется при сварке большинства металлов: углеродистая и нержавеющая сталь, медь, титан. Дает стабильную дугу и глубокий провар. Переменный ток применяется для алюминия и его сплавов. В режиме переменного тока происходит очистка поверхности от оксидной пленки, что улучшает качество соединения.
- Сила тока. Интенсивность теплового воздействия на металл. Чем выше ток, тем глубже провар и быстрее плавление металла. Однако при работе с тонкими изделиями важно избегать слишком высокой силы тока, чтобы предотвратить прожог.
- Выбор диаметра электрода. Диаметр вольфрамового электрода зависит от силы тока и толщины свариваемого материала. Чем больше ток, тем больший диаметр электрода требуется для обеспечения стабильности дуги.
- Расход защитного газа. Оптимальный расход аргона зависит от толщины свариваемого материала и диаметра электрода. Обычно варьируется в пределах от 5 до 15 литров в минуту. Слишком малый расход газа может привести к окислению шва, а слишком большой – к турбулентности и загрязнению сварочной зоны.
- Полярность тока. В аргоновой сварке на постоянном токе используется отрицательная полярность (DCEN – Direct Current Electrode Negative), при которой дуга стабильнее, а провар глубже. На переменном токе используется чередование полярностей, что способствует эффективной очистке поверхности алюминия от оксидной пленки.
Для сварки алюминия и его сплавов применяется переменный ток, который позволяет очищать оксидную пленку, образующуюся на поверхности металла. Благодаря режиму AC дуга стабильная, слияние металла качественное. Важно правильно настроить соотношение между фазами тока, чтобы добиться оптимального баланса между очисткой поверхности и плавлением металла.
Для работы с нержавеющей сталью обычно используется постоянный ток (DC) с отрицательной полярностью (DCEN). Этот режим позволяет достичь хорошего провара и минимизировать термическое воздействие на зону сварки, снижает риск коробления и деформации материала. Важно контролировать процесс, чтобы избежать перегрева и изменения структуры заготовки.
Титан требует работы с высокой степенью защиты от кислорода, так как этот металл активно реагирует с воздухом при высоких температурах. Режим TIG-сварки на постоянном токе с использованием аргоном и минимальным подогревом идеален для титана. При сварке необходимо использовать специальные защитные экраны или камеры, чтобы исключить контакт металла с воздухом.
Аргоновая сварка может осуществляться с или без использования присадочного материала, и это напрямую влияет на режим переноса металла:
- Без присадочного материала. Этот метод используется при сварке тонких материалов и небольших соединений. Дуга плавит кромки свариваемых деталей, образуя шов без добавления дополнительного материала. Это позволяет добиться очень точных и аккуратных соединений.
- С присадочным материалом. Присадочная проволока вводится вручную или автоматически в зону сварки. Этот метод необходим при соединении толстых материалов или когда требуется заполнить зазор между деталями. Выбор присадочного материала должен соответствовать основному металлу для надежности соединения.
Аргоновая сварка – высокотехнологичный и точный метод соединения металлов, который позволяет получать высококачественные сварные швы на самых разных материалах. Тонкая настройка режимов, выбор тока, диаметра электрода и расхода защитного газа дают отличные результаты при работе с ответственными конструкциями, где важны прочность и долговечность соединений. Однако данный метод требует высокой квалификации сварщика и тщательного контроля параметров процесса.
Сварка газом
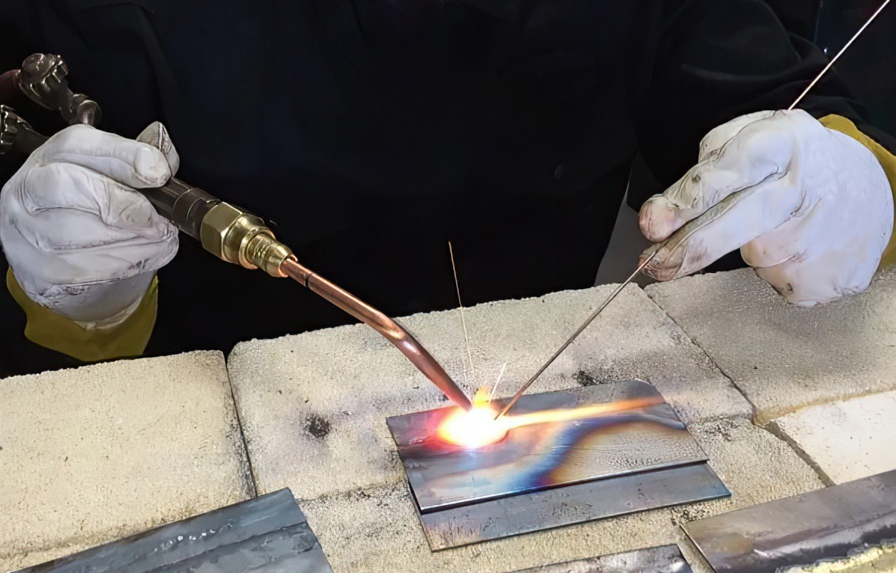
Один из старейших и наиболее универсальных методов соединения металлов, который используется в различных отраслях промышленности и строительства. Основным источником тепла в этом процессе является газовая горелка, которая генерирует пламя за счет сгорания горючего газа, обычно ацетилена, в смеси с кислородом. Для достижения качественного результата важно правильно подобрать режимы работы, включающие параметры: давление газа, температура пламени, скорость сварки и расстояние от горелки до металла.
При сварке газом важен комплексный подход к выбору рабочих параметров. Они включают:
- Давление кислорода и горючего газа. Основные газы, применяемые в сварке, – это ацетилен и кислород. Для правильного функционирования горелки необходимо точно регулировать подачу газа, так как от этого зависит интенсивность пламени и его температура. Обычно давление ацетилена варьируется от 0,5 до 1,5 атмосфер, в зависимости от толщины свариваемого материала. Давление кислорода, как правило, выше, достигая 2-4 атмосфер.
- Состав пламени. Пламя газовой горелки может быть трех видов: окислительным, восстановительным и нормальным (нейтральным). Окислительное пламя характеризуется избытком кислорода. Его используют для работы с металлами, требующими интенсивного окисления, например, для сварки бронзы или латуни. Восстановительное содержит больше ацетилена, чем кислорода. Подходит для пайки и сварки цветных металлов, где важно избегать окисления. Нормальное пламя имеет равное соотношение кислорода и ацетилена и является универсальным для большинства сварочных операций.
- Скорость подачи газа и движения горелки. Эти параметры влияют на стабильность сварки и качество шва. При слишком медленном движении горелки металл может перегреваться и деформироваться, тогда как слишком быстрая работа может привести к недостаточному провару и образованию дефектов шва.
- Температура пламени. Максимальная температура пламени при горении ацетилена в кислороде достигает 3200°C. Однако для большинства сварочных операций достаточно температур в диапазоне 2500–3000°C. Температура регулируется соотношением газа и кислорода, что позволяет контролировать процесс нагрева металла.
- Одноимпульсная. В этом режиме на протяжении одного цикла подается только один импульс тока. Чаще всего используется для тонкостенных металлов, где важно минимизировать тепловое воздействие и избежать перегрева. Характеризуется относительно низкой скоростью процесса, однако поддерживает высокую точность и минимальные деформации.
- Многоимпульсная. Этот режим предполагает серию импульсов в течение одного цикла. Применяется для более толстых материалов, глубоко проплавляет, сохраняя при этом все преимущества импульсного режима – снижение теплового воздействия и улучшенный контроль процесса.
- Двойная импульсная. В данном режиме применяются два разных импульса тока с различной амплитудой и частотой в одном цикле. Это улучшает контроль плавления и снижает количество брызг, помогая сформировать высококачественное соединение даже трудносвариваемых материалов – алюминия или магниевых сплавов. Востребован режим в автомобильной и авиационной промышленности, где часто имеют дело со сложными сплавами, требующими точного контроля за тепловым воздействием.
- Модулированная – изменяются параметры импульсов в процессе: длительность, частота и амплитуда тока. Позволяет гибко адаптировать сварку в зависимости от толщины материала или его химического состава. Часто используется для сложных металлов, где важно достичь равномерного распределения тепла.
- Сварочный ток;
- Напряжение дуги;
- Скорость подачи сварочной проволоки;
- Скорость сварки;
- Диаметр электрода (сварочной проволоки);
- Толщина и тип флюса.
- Прочность и долговечность;
- Отсутствие дефектов (например, пор, трещин, непроваров);
- Однородность металла шва и основного металла;
- Сопротивление коррозии.
- Сила сварочного тока. Должна быть достаточно высокой для необходимого прогрева свариваемых поверхностей до температуры плавления. Недостаточная сила приводит к слабому нагреву, может стать причиной непрочного соединения, а чрезмерная – к перегреву металла и образованию дефектов (например, пор или наплывов).
- Время нагрева (продолжительность сварки). Время нагрева непосредственно влияет на степень оплавления деталей. Чем дольше осуществляется сварка, тем сильнее прогреваются края заготовок. Слишком продолжительный процесс может вызвать перегрев металла и его деформацию, а слишком короткий – недостаточную прочность сварочного шва.
- Давление сжатия (сила сжатия). Важным условием качественной стыковой сварки является правильное давление между свариваемыми заготовками. Давление оказывает воздействие на плотность соединения и формирование сварочного шва. Должно быть достаточным для удаления оксидной пленки и предотвращения образования пор, но не чрезмерным, чтобы не вызвать механических деформаций и ухудшения качества шва.
- Скорость охлаждения. После завершения процесса металл должен остыть. Скорость охлаждения влияет на структуру шва и его механические свойства. Быстрое охлаждение может привести к образованию хрупкой структуры (особенно в углеродистых сталях), а медленное способствует улучшению пластичности, но может ослабить соединение.
- Прогрев и постнагрев. В некоторых случаях используется предварительный или последующий нагрев для предотвращения образования трещин и деформаций в сварочном шве. Параметр особенно важен при сварке высокоуглеродистых или легированных сталей, которые склонны к образованию закалочных структур при быстром охлаждении.
- Сила тока – зависит от толщины и материала свариваемых деталей.
- Давление – регулирует плотность соединения и предотвращает образование пор.
- Время сварки – контролирует степень прогрева и плавления металла.
- Ток – должен обеспечить равномерный нагрев заготовок.
- Давление при оплавлении – позволяет сформировать качественный сварной шов.
- Время нагрева – зависит от толщины и материала заготовок.
- Температура и продолжительность подогрева.
- Сила тока и время выдержки.
- Сила сжатия во время сварки.
- Сила сварочного тока – электрический ток, подаваемый через детали, нагревает их до температуры плавления в месте контакта.
- Продолжительность сварки – время, в течение которого ток воздействует на детали.
- Сила прижима – давление, которое прикладывается к свариваемым деталям для их соединения.
- Точечная сварка;
- Шовная;
- Рельефная.
- Импульсный режим – короткий, но мощный импульс тока подается на свариваемые детали, быстрое нагревание и соединение в месте контакта.
- Многоимпульсный режим – для более толстых материалов применяется серия импульсов тока, что позволяет предотвратить перегрев и лучше контролировать процесс нагрева.
- Кратковременные импульсы. Для нагрева рельефных выступов используется короткая подача тока, быстрый локальный нагрев и плавление.
- Увеличенное давление. После нагрева рельефные выступы расплавляются и сплющиваются под действием высоко
- Высокая производительность;
- Глубокое проплавление и прочный шов;
- Отсутствие брызг и выбросов газов.
- Ограничение использования на открытых участках из-за необходимости закрытия зоны сварки флюсом;
- Применение в основном для сварки горизонтальных и вертикальных швов.
- Универсальность (можно сваривать различные типы металлов);
- Возможность работы в разных положениях;
- Высокая скорость и автоматизация процесса.
- Высокие требования к защите зоны сварки от ветра при работе на открытом воздухе;
- Возможность пор при недостаточной защите газом.
- Точная регулировка процесса;
- Возможность сварки тонких материалов;
- Высокая стабильность дуги.
- Сложность оборудования и необходимость квалифицированного персонала;
- Высокая стоимость применения.
- Высокая скорость выполнения;
- Минимальное тепловое воздействие на материал;
- Низкие затраты на расходные материалы.
- Ограниченная толщина свариваемых изделий;
- Необходимость точного контроля давления и тока.
- Минимальные тепловые деформации;
- Возможность сварки на большой скорости;
- Высокая точность и контроль процесса.
- Высокая стоимость оборудования;
- Ограничение по толщине материалов.
- Возможность сварки толстых материалов;
- Высокая производительность на длинных швах.
- Использование только в ограниченных положениях (обычно вертикальные швы);
- Сложность контроля процесса.
- Независимость от источников электроэнергии;
- Применение в полевых условиях.
- Ограниченное применение;
- Трудоемкость и сложность выполнения.
- При выполнении многослойных стыковых швов первый слой сваривают электродом диаметром 3–4 мм, а последующие слои – электродами большего диаметра.
- Для вертикальных швов применяют стержни диаметром не более 5 мм. Потолочные швы выполняются изделиями до 4 мм.
- При наплавке изношенных поверхностей необходимо восстановить толщину изношенного слоя и добавить 1–1,5 мм для последующей обработки поверхности.
- Сила тока;
- Напряжение дуги;
- Скорость сварки;
- Диаметр электрода (или проволоки);
- Тип и состав защитного газа (при сварке в среде газа).
- Защищает зону сварки от воздействия кислорода и азота, предотвращая образование оксидов и пористости в металле.
- Способствует стабилизации дуги.
- Глубокий провар. CO₂ обеспечивает отличное проплавление металла, это важно при сварке толстых листов стали.
- Низкая стоимость. По сравнению с другими защитными газами углекислый газ экономически выгодное решение.
- Стабильная дуга – аргон способствует созданию более устойчивой дуги, упрощает процесс сварки.
- Лучший внешний вид шва – шов получается более гладким и с меньшим количеством дефектов.
- Меньшее разбрызгивание – в сравнении с использованием чистого CO₂, смеси создают меньшее количество брызг, что снижает затраты на очистку.
- Стенка толщиной до 3 мм сваривается за один проход;
- При толщине от 3 до 6 мм требуется два прохода;
- Трубы с толщиной стенки 6-12 мм свариваются в три слоя;
- При толщине свыше 12 мм выполняется четыре и более прохода по мере необходимости.
- Снижение температурных градиентов – быстрое охлаждение сварного шва и зон вокруг него может привести к возникновению термических напряжений, что, в свою очередь, увеличивает риск появления трещин. Предварительный нагрев снижает разницу температур между основным металлом и сварным швом, создавая условия более плавного охлаждения.
- Уменьшение скорости охлаждения. Когда металл остывает слишком быстро, особенно в высокоуглеродистых и низколегированных сталях, это может привести к образованию закаленных структур – мартенсит. Мартенситная структура хрупка и чувствительна к трещинам. Нагрев перед сваркой дает возможность контролировать скорость охлаждения и предотвратить образование нежелательных структур.
- Снижение водородных трещин. Водородные трещины – тип дефекта, который возникает из-за содержания водорода в сварочном шве или околошовной зоне. При нагреве металла водород быстрее диффундирует и выходит из материала, минимизируя риск образования водородных трещин.
- Повышение пластичности. Предварительный нагрев улучшает пластичность металла, за счет чего сварное соединение лучше выдерживает деформации при термическом воздействии, особенно в условиях повышенных нагрузок.
- Газовые горелки. Один из самых распространенных методов. Горелки сжигают природный газ или пропан, нагревая металл. Распространены при сварке на открытом воздухе и на производственных площадках.
- Электрические нагревательные элементы. Для более точного и равномерного нагрева применяют электрические печи или гибкие нагреватели, которые оборачиваются вокруг свариваемого участка.
- Индукционный нагрев. Метод высокочастотного индукционного нагрева создает тепловую энергию в металле за счет электромагнитного поля. Этот способ наиболее эффективен для крупных производственных объектов.
- Инфракрасные нагреватели. Применяются для поверхностей, равномерно нагревают на больших площадях.
Сварка на пониженных режимах – используется при работе с тонкими металлами или деталями, требующими аккуратной обработки. В этом режиме снижается давление горючего газа и кислорода, уменьшается интенсивность пламени. Скорость перемещения горелки также снижается, позволяя лучше контролировать процесс плавления и избегать прожогов.
На нормальных режимах – применяется для стандартных задач, когда необходима высокая скорость и достаточная прочность сварочного шва. Давление кислорода и ацетилена в этом соответствует средним значениям, что позволяет достичь стабильного и равномерного пламени. Такой режим чаще всего используется для работы с углеродистыми сталями и конструкционными материалами.
На повышенных режимах – предназначена для толстых металлов или деталей, требующих быстрого выполнения сварочных операций. В этом режиме увеличивается давление газов, повышается температура пламени и скорость плавления металла. Однако такой режим требует опыта, так как при неправильной настройке можно перегреть металл и нарушить целостность конструкции.
Импульсная
Метод дуговой сварки, при котором подача тока осуществляется в виде кратковременных импульсов с переменным значением силы. В отличие от традиционных решений сварки, где ток подается на постоянном уровне, импульсная использует чередование пиковых и низких значений тока, позволяя добиться большей точности и контроля процесса. Широко используется в промышленности для соединения алюминия, нержавеющей стали и титана, которые труднее сваривать с использованием обычных методов.
Режимы импульсной сварки играют ключевую роль в оптимизации процесса, влияя на качество шва, тепловое воздействие на металл, а также на скорость и экономичность сварки.
Процесс основан на циклическом изменении тока между пиковыми и базовыми значениями. Пиковый ток отвечает за плавление сварочного материала и формирование капли, а базовый – поддерживает дугу и обеспечивает минимальное нагревание заготовки, уменьшает термическое воздействие на металл. Таким образом, в процессе сварки возникает чередование фаз нагрева и охлаждения, аккумулируются преимущества как высокой, так и низкой плотности тока.
Есть следующие режимы импульсной сварки:
Импульсная сварка – высокоэффективная технология, которая сочетает точность, контроль и качество. Выбор правильного режима здесь играет ключевую роль в достижении результата и зависит от материала, толщины изделия и конкретных требований ко шву. Современные разработки и автоматизированные системы управления адаптируют импульсные режимы для широкого спектра материалов и задач, поэтому метод – универсальный инструмент в арсенале современной промышленности.
Под флюсом
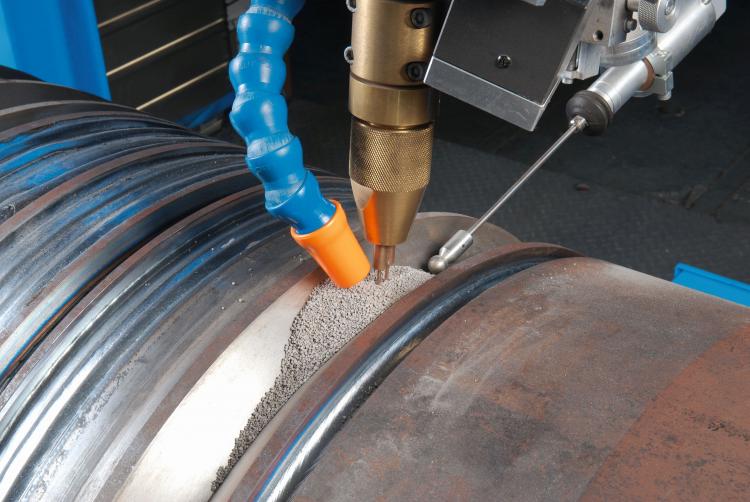
Сварка под флюсом (или дуговая сварка под слоем флюса, сварка SAW — Submerged Arc Welding) – один из высокоэффективных методов, используемый для соединения металлических изделий. Активно применяется в тяжелой промышленности, производстве трубопроводов, судостроении и других областях, где необходимы прочные и долговечные сварные соединения. Основное преимущество этого метода заключается в высокой производительности и качестве сварного шва. Ключевую роль в достижении нужного результата играют правильно подобранные режимы сварки – совокупность параметров, которые влияют на процесс формирования шва.Основные из них:
От выбора этих параметров зависит качество шва, производительность процесса и его экономичность.
Сварочный ток – важнейший параметр, влияющий на глубину проплавления и стабильность дуги. Чем больше сварочный ток, тем выше тепловая мощность электродуги, что увеличивает глубину проплавления металла. Слишком высокий ток может привести к чрезмерному проплавлению и деформациям, в то время как недостаточный – даст плохое сцепление металла, и тогда возможны дефекты.
Напряжение дуги, в свою очередь, влияет на форму шва и длину дуги. При низком напряжении электродуга становится короткой и концентрированной, способствует глубокому проплавлению. Высокое напряжение увеличивает ширину шва, но снижает глубину проплавления.
Оптимальные значения тока и напряжения зависят от толщины свариваемого металла, типа флюса и других факторов.
Скорость подачи сварочной проволоки влияет на скорость плавления электродного материала и тем самым – на производительность сварочного процесса. При слишком низкой скорости может не хватить металла для образования шва, что приводит к образованию дефектов. В то же время высокая скорость может привести к перенасыщению зоны сварки материалом и образованию выступов или наплывов.
Скорость перемещения сварочной горелки по поверхности свариваемого изделия определяет ширину и высоту шва, а также глубину проплавления. Более высокая скорость сварки уменьшает количество тепла, передаваемого на металл, снижает глубину проплавления. Может повысить риск появления непроваров. Слишком низкая, наоборот, увеличивает количество тепла, но может привести к деформациям и перегреву металла.
Диаметр сварочной проволоки также оказывает влияние на процесс сварки. Более тонкая проволока требует меньшего сварочного тока и способствует формированию узкого, но глубокого шва. Толстая проволока используется для более мощных сварочных процессов, так как она способна выдерживать большие токи и формировать широкий шов.
Флюс играет важную роль в процессе работы. Он защищает зону сварки от атмосферных загрязнений, стабилизирует дугу и способствует формированию качественного шва. Тип и толщина флюса выбираются в зависимости от свариваемого материала и требуемых свойств соединения.
Активные флюсы взаимодействуют с расплавленным металлом, изменяя его химический состав, улучшают механические свойства шва.
Пассивные флюсы используются для минимизации химического взаимодействия с металлом, их применяют, когда важен контроль над чистотой шва.
Правильный выбор режима сварки под флюсом позволяет достичь важных характеристик сварного соединения:
Например, слишком высокий сварочный ток может вызвать появление горячих трещин в шве, а слишком низкий ток – недостаточное проплавление, что снизит прочность соединения. Правильно подобранная скорость сварки позволяет избежать деформаций и перегрева металла.
Тщательная настройка параметров позволяет адаптировать процесс к специфике свариваемого материала и задачам производства. Оптимальные режимы обеспечивают надежность и долговечность готовых конструкций, минимизируют вероятность появления дефектов и способствуют повышению экономической эффективности всего процесса.
Стыковая

Стыковая сварка – вид контактной сварки, при котором соединяемые детали располагаются торцами друг к другу, а соединение осуществляется за счет теплового воздействия, возникающего при прохождении электрического тока через места их контакта. Этот метод широко используется в машиностроении, металлообработке и строительстве.
Основой эффективного проведения стыковой сварки выступает правильный выбор и настройка сварочного режима.
Основные параметры режимов здесь следующие:
В зависимости от применяемой технологии и типа соединяемых материалов выделяют несколько основных режимов стыковой сварки.
Сварка сопротивлением. Этот метод основан на тепловом эффекте Джоуля, когда электрический ток, проходящий через места контакта заготовок, вызывает их нагрев до температуры плавления. Соединение происходит под действием сжимающего усилия.
Параметры режима:
Далее стыковая сварка оплавлением. Концы свариваемых деталей сначала разогреваются до температуры плавления, а затем под давлением соединяются. Этот метод широко применяется для сварки труб, рельсов и других длинных заготовок.
Параметры режима стыковой сварки оплавлением:
Применяют также термическую стыковую сварку.
Режим предполагает использование не только электрического тока, но и дополнительного источника тепла (например, газовой горелки). Метод применяется при сварке толстостенных деталей или деталей из различных по составу металлов.
Основные параметры:
Режимы стыковой сварки играют решающую роль в качественном и надежном сварочном соединении. Оптимальный выбор параметров зависит от свойств материалов, толщины деталей и требований к прочности соединения. Понимание и правильная настройка всех режимов процесса способствует повышению производительности и долговечности конструкций.
Контактная
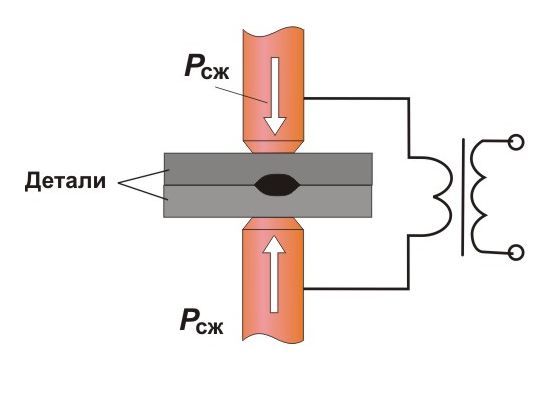
Способ соединения металлических деталей посредством электрического тока и сжатия. Процесс широко используется в автомобилестроении, авиации, строительстве и производстве техники. Эффективность и качество здесь во многом зависят от правильного выбора режима сварки.
В свою очередь, режимы определяются рядом параметров:
Эти параметры находятся в тесной взаимосвязи: изменение одного из них требует корректировки других для качественного соединения.
Контактную сварку можно разделить на несколько типов в зависимости от метода передачи тепла и способа применения давления. Основные виды:
Точечная сварка – один из самых распространенных видов контактной сварки. Соединение металлов происходит в отдельных точках при кратковременной подаче тока и высоком давлении.
В данном случае ключевые параметры:
Режимы зависят от толщины и типа свариваемых материалов. Чем больше толщина, тем больше требуется силы тока и времени для образования качественного сварного соединения.
Другое решение – шовная сварка. Используется для создания непрерывного соединения путем подачи тока через вращающиеся электроды. Такой метод особенно эффективен для герметичных соединений, например, в производстве топливных баков или контейнеров.
Постоянный режим – постоянная подача тока через электроды в течение всего процесса сварки.
Импульсный – ток подается в виде серии импульсов, позволяет добиться равномерного нагрева и избежать перегрева или деформации деталей.
Продолжительность импульсов и сила тока варьируются в зависимости от толщины металла и требуемой прочности соединения.
Также рельефная сварка. Основана на предварительной подготовке деталей, на которых создаются рельефные выступы. Эти выступы локально концентрируют электрический ток, позволяя добиться точного и контролируемого соединения.
Основные режимы рельефной сварки:
Этот вид сварки часто используется для соединения материалов с различной толщиной или формой.
Качество сварки во многом зависит от правильной настройки всех параметров процесса. Например:
Если ток слишком мал, металл может не достичь температуры плавления, что приведет к слабому соединению. Слишком высокий ток, наоборот, может вызвать перегрев и прожог деталей.
Недостаточное давление приводит к неполному соединению деталей, тогда как чрезмерное давление может вызвать деформацию и ухудшение прочностных характеристик сварного шва.
Слишком короткая подача тока не даст достаточного нагрева, тогда как чрезмерное время нагрева может вызвать перегрев и ухудшение качества соединения.
Современные системы контактной сварки оснащаются программным обеспечением, которое автоматически регулирует параметры режима в зависимости от типа и толщины материала. Такие системы значительно повышают точность и качество сварки, сводя к минимуму влияние человеческого фактора.
Автоматическая
Процесс соединения материалов с использованием специального оборудования, которое автоматически контролирует и выполняет сварочные операции. Автоматический метод дает стабильное качество сварных швов, высокую производительность и минимизацию влияния человеческого фактора. Применяют несколько режимов автоматической сварки, каждый из которых предназначен для выполнения определенных задач и условий работы. Рассмотрим основные из них.
Автоматическая сварка под флюсом (Submerged Arc Welding, SAW) – характеризуется высокой производительностью и качеством шва. В этом процессе электродный проводник подается автоматически в зону сварки, которая покрыта флюсом, предотвращающим доступ кислорода и других атмосферных газов. Позволяет избежать окисления металла и получить качественный шов с минимальным количеством пор и трещин.
Преимущества:
Недостатки:
Другой вариант – автоматическая дуговая сварка в среде защитных газов (MIG/MAG). Этот метод широко используется в промышленности благодаря высокой универсальности и эффективности. В данном случае зона сварки защищена инертным (MIG) или активным (MAG) газом, предотвращающим попадание воздуха в область дуги. В процессе происходит плавление присадочного материала, который подается автоматически.
Преимущества:
Недостатки:
Применяют еще плазменную сварку – высокотемпературный процесс, при котором используется плазменная дуга для плавления металлов. Метод позволяет получить высокую точность и чистоту сварного шва, что делает его востребованным в таких областях, как авиастроение и микроэлектроника. Плазма образуется за счет ионизации газа, который подается в зону дуги.
Преимущества:
Недостатки:
Это один из видов контактной сварки – точечная, при которой соединение происходит за счет приложения высокого давления и электрического тока через контактные электроды. Метод особенно эффективен при массовом производстве, например, в автомобильной промышленности для соединения листовых материалов.
Преимущества:
Недостатки:
Передовая – лазерная автоматическая сварка, основана на использовании концентрированного лазерного луча, который направляется на свариваемые поверхности, вызывая их плавление и соединение. Метод известен высокой точностью и возможностью сварки в труднодоступных местах.
Преимущества:
Недостатки:
Отметим также электрошлаковую сварку, применяется для соединения толстостенных металлоконструкций. В этом процессе соединение происходит за счет проплавления металла в жидком шлаке, который выполняет роль защитной среды. Данный метод хорошо подходит для вертикальных швов.
Преимущества:
Недостатки:
Нельзя не сказать о термитной сварке. Использует тепло, выделяемое при химической реакции между алюминием и оксидом железа (термитом), для расплавления и соединения металлов. Этот метод часто применяется при ремонте и соединении рельсов на железных дорогах.
Преимущества:
Недостатки:
Каждый из перечисленных режимов имеет свои особенности, преимущества и ограничения. Выбор подходящего зависит от конкретных задач, материала, условий работы и экономической целесообразности. В промышленности важно учитывать все эти факторы для достижения оптимального качества швов и производительности процесса. Автоматизация позволяет существенно повысить эффективность производства, сократить затраты и минимизировать вероятность дефектов, что делает ее неотъемлемой частью современной индустрии.
Расчет режима
При РДС расчет режимов сварки относится к силе тока, напряжению, скорости перемещения электрода вдоль шва (скорость сварки), типа тока, полярности и другим факторам.
Диаметр электрода подбирается с учетом толщины свариваемого металла, типа сварного соединения и пространственного расположения шва. Здесь можно ориентироваться на следующие рекомендации:
Сила сварочного тока, выраженная в амперах, рассчитывается по формуле:
где K — коэффициент, варьирующийся от 25 до 60 А/мм, а dЭ — диаметр электрода в миллиметрах.
Значение коэффициента K зависит от диаметра электрода.
Полученную формуле силу сварочного тока необходимо скорректировать с учетом следующих факторов: толщины свариваемого металла, типа сварного соединения и положения шва.
Если толщина металла S≥3dЭS≥3dЭ, силу тока увеличивают на 10–15%.
Если S≤1,5dЭS≤1,5dЭ, ток уменьшают на 10–15%.
Для угловых швов и наплавки ток увеличивают на 10–15%.
При сварке в вертикальном или потолочном положении ток снижают на 10–15%.
Напряжение дуги для большинства марок электродов, применяемых для сварки углеродистых и легированных сталей, обычно составляет 22–28 В.
Скорость сварки, выраженная в метрах в час, рассчитывается по следующей формуле:
где:
αH — коэффициент наплавки (г/А·ч), значение которого берется из характеристик выбранного электрода (согласно таблице 9 приложения),
FШВ — площадь поперечного сечения шва при однопроходной сварке или одного слоя валика при многослойной сварке, см²,
ρ — плотность металла электрода, г/см³ (для стали ρ=7,8ρ=7,8 г/см³).
Масса наплавленного металла, выраженная в граммах, при ручной дуговой сварке рассчитывается по формуле:
l — длина шва, см,
FШВ — площадь поперечного сечения шва, см²,
ρ — плотность наплавленного металла (для стали ρ=7,8ρ=7,8 г/см³).
Для ручной дуговой наплавки масса наплавленного металла определяется по следующей формуле:
где:
FНП — площадь наплавляемой поверхности, см²,
hН — требуемая высота наплавленного слоя, см.
Время горения дуги, или основное время сварки, рассчитывается по формуле:
Полное время сварки или наплавки можно приблизительно вычислить по формуле:
где:
tO— время горения дуги, ч,
kP — коэффициент использования сварочного поста, который для ручной сварки составляет 0,5–0,55.
Расход электродов ручной дуговой сварки или наплавки определяется по следующей формуле:
В данном случае kЭ – коэффициент, учитывающий расход электродов на 1 кг наплавленного металла.
Сколько потребуется электроэнергии – такая формула:
где UД – напряжение дуги; η– КПД источника питания сварочной дуги; WO – мощность, расходуемая источником питания сварочной дуги при холостом ходе, кВт; Т– полное время сварки или наплавки.
Сварка стали
Сварка стали – важнейший процесс в машиностроении, строительстве и металлургии, используемый для надежных и долговечных соединений. Но чтобы успешно выполнить сварочные работы, нужно правильно выбрать режимы, особенно при работе со сталью, так как различные параметры могут значительно повлиять на качество сварного шва.
Основные параметры, которые учитываются при выборе режима сварки:
Параметры непосредственно влияют на форму, прочность и качество сварного шва, а также на скорость выполнения работ.
Сила сварочного тока – один из важнейших параметров, влияющий на глубину провара и стабильность сварочной дуги. Чем больше сила тока, тем глубже будет провар материала, что особенно важно при работе с толстыми стальными изделиями. Однако слишком высокий ток может вызвать прожоги, деформации и повышенное разбрызгивание металла.
Для разных типов сварки (например, ручная дуговая сварка, аргонодуговая сварка или полуавтоматическая сварка) значения тока могут значительно различаться. Например:
При ручной дуговой сварке электродом сила тока обычно варьируется от 70 до 150 А для стали толщиной 2-5 мм.
Для полуавтоматической сварки в среде защитных газов параметры тока могут быть выше, особенно при работе с массивными деталями.
Напряжение дуги – влияет на длину дуги и, как следствие, на ширину и форму сварного шва. Чем выше напряжение, тем длиннее дуга, приводит к более широкому шву с меньшей глубиной провара. При низком напряжении шов получается узким, но с глубокой зоной проплавления.
При работе со сталью важно подобрать оптимальное напряжение в зависимости от типа сварочного оборудования и толщины свариваемых деталей.
Скорость сварки – оказывает существенное влияние на качество шва. При слишком высокой скорости шов может оказаться неполным или с недостаточным проплавлением, что негативно скажется на прочности соединения. Слишком низкая скорость, в свою очередь, приведет к избыточному нагреву металла, его деформации и появлению дефектов – наплывы или прожоги.
В среднем, для сварки стали толщиной 3-6 мм скорость сварки обычно составляет 20-40 см/мин, но этот параметр сильно зависит от способа сварки и оборудования.
Выбор диаметра электрода или сварочной проволоки зависит от толщины свариваемой стали. Чем толще сталь, тем больший диаметр электрода следует использовать. Например:
Для стали толщиной 1-2 мм обычно применяют электроды диаметром 1,6-2 мм.
Для более толстого материала – от 4 мм и выше – используют электроды диаметром 3-5 мм.
Правильный выбор диаметра – равномерное распределение тепла и проплавление металла.
При сварке в среде защитного газа (MIG/MAG или TIG сварка) важно правильно подобрать газ или смесь газов. Чаще всего для сварки углеродистой и низколегированной стали используют углекислый газ (CO₂) или смесь аргона с CO₂.
Защитный газ выполняет функции:
При выборе газа важно учитывать особенности металла и тип сварочного процесса.
Углекислый газ – один из самых популярных для сварки углеродистой стали, особенно в полуавтоматическом режиме (MIG/MAG). Он активно используется как в чистом виде, так и в смесях. Основные преимущества:
Однако есть и некоторые недостатки. При использовании чистого CO₂ дуга может быть менее стабильной, а шов – иметь больше разбрызгивания металла. Поэтому его часто комбинируют с аргоном (смесь аргона и CO₂).
Аргон сам по себе инертный газ и не вступает в химические реакции с металлом. Смеси аргона и углекислого газа (например, 80% аргона и 20% CO₂) позволяют улучшить стабильность дуги и уменьшить разбрызгивание. Преимущества в данном случае:
Такие смеси часто используют для сварки конструкционных сталей и металлов средней толщины.
Что касается нержавеющей стали, требует особого подхода к выбору газа, так как защитный газ должен не только предотвращать окисление, но и сохранять коррозионные свойства материала.
Чистый аргон чаще всего используется для сварки нержавеющей стали, особенно в процессе TIG.
Предотвращает окисление – благодаря инертности аргона сварочная ванна надежно защищена от воздействия окружающей среды, что предотвращает образование оксидов.
Поддерживает стабильную дугу – сварка в аргоне характеризуется мягкой и устойчивой электродугой, она необходима при работе с тонкими нержавеющими материалами.
Для повышения производительности могут использоваться смеси аргона с добавлением небольших количеств CO₂ или кислорода (до 5%). Смеси помогают улучшить провар и стабилизировать дугу.
Аргон + CO₂ – добавление CO₂ (обычно 1-2%) улучшает глубину провара и способствует более стабильному процессу сварки.
Аргон + кислород (O₂) – включение кислорода (1-2%) способствует улучшению смачивания сварочной ванны, делая шов более ровным и эстетически привлекательным.
Однако важно не допускать избыточного содержания активных газов, чтобы не ухудшить коррозионную стойкость нержавеющей стали.
Сварка труб
Выбор подходящего режима сварки труб зависит от множества факторов: тип трубы, толщина металла, условия работы и т.д.
Для стальных трубопроводов чаще всего применяются газовая или электросварка. В случае если трубопроводы будут эксплуатироваться под высоким давлением, к электродам и присадочной проволоке предъявляются повышенные требования.
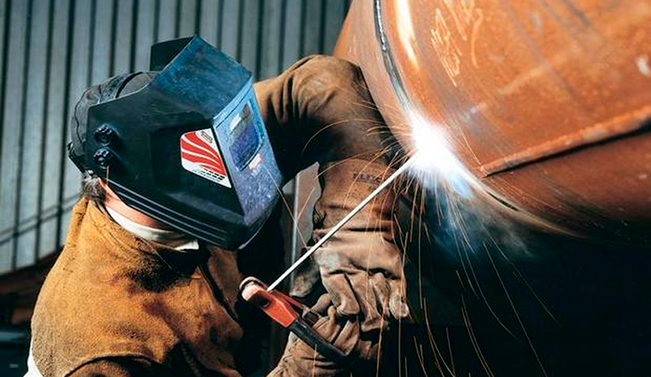
Количество слоев сварных соединений зависит от толщины стенки трубы:
Выбор силы тока для дуговой сварки труб также подчиняется определенным правилам: сила тока рассчитывается по диаметру электрода, умножая его на 35. Например, для электрода диаметром 3 мм устанавливают ток 105 А, а для 4 мм — 140 А.
Для труб с толщиной стенки менее 4 мм оптимальным является ток в 150 А, превышать это значение не рекомендуется.
Расстояние между электродом и металлом должно составлять толщину электрода плюс 1 мм.
Тонкостенные трубы свариваются одной сплошной проходкой, вращая их по мере работы, а толстостенные можно варить участками по 15 см.
Неповоротные или вертикальные стыки свариваются в два этапа.
Угол наклона расплавленной сварочной ванны должен составлять 30° от верхней точки.
Допустимый выступ валика финишного слоя над поверхностью металла не должен превышать 3 мм. После каждого прохода необходимо снимать окалину и проверять качество сварного шва.
Для дуговой сварки труб, применяемых в газопроводах и насосно-компрессорных трубопроводах (НКТ), подходят электроды марок ОК-46, ЛБ-52 и УОНИ-13/55. Обладают необходимым химическим составом, включающим фосфор, марганец, кремний и серу. Среди них наиболее универсальными считаются электроды ОК-45, которые предполагают рутиловое покрытие. Они особенно удобны для заварки больших зазоров, что делает их полезными в сложных ситуациях.
Электроды LB 52U с основным покрытием выделяются за счет низкого содержания водорода, что обеспечивает высокое качество шва. Эти электроды легко поджигаются, создают стабильную дугу и эффективно проваривают края соединяемых деталей, обеспечивая надежность сварного соединения.
Для сварки особо ответственных участков – поворотные соединения, на углеродистых или низколегированных стальных трубах – специалисты рекомендуют МТГ-01К. Эти электроды дают стабильную дугу с минимальными брызгами, а образующийся шлак легко удаляется, что повышает удобство работы и улучшает конечный результат.
Для сварки отопительных труб оптимально подходят электроды марок Э42А и УОНИ 13/45 диаметром 3 мм. Эффективны с углеродистой сталью благодаря толстому внешнему покрытию. Также хорошие варианты – Э-09Х1МФ и ЦЛ-20, дают прочное соединение труб из термостойкой стали, аналогично электродам Э42А и УОНИ 13/45, за счет толстого покрытия.
Дуговая сварка труб из легированной, углеродистой или нержавеющей стали – идеально подходят ЦЛ-9 с основным покрытием. Благодаря низкому содержанию углерода стрежни обеспечивают надежное и прочное сварное соединение.
При сварке водопровода выбор электродов зависит от материала труб. Для труб из меди наиболее подходят электроды МН-5 и МНЖ-5, для нержавеющей стали – НЖ-13, а для чугунных труб – МНЧ-2.
Если вы планируете самостоятельно выполнять сварочные работы дома с помощью инвертора, у вас трубы из черного металла, то электроды МР-3с будут отличным выбором. Ими можно качественно сварить стыки диаметром 32 мм и толщиной стенок 2,8 мм, при этом высокие значения рабочего тока не требуются.
Для вертикальных швов хорошо подходят электроды МНЧ-2. При использовании нижнего положения электрода для сварки можно использовать электроды ЦЧ-4, как для холодной, так и для горячей сварки.
Важно, чтобы у электродов было защитное покрытие, предотвращающее окисление сварочной зоны. Для дуговой сварки труб предпочтительно выбирать электроды с более толстым покрытием, чтобы повысить качество соединения.
Режим подогрева
Предварительный нагрев – технологический процесс, при котором металлы или сплавы подвергаются нагреву до определенной температуры перед выполнением сварки. Этот режим используется для улучшения сварных соединений, предотвращения дефектов, снижения остаточных напряжений и минимизации риска возникновения трещин.
Зачем нужен предварительный нагрев?
При сварке выполняет несколько функций:
В каких случаях применяется предварительный нагрев?
Стали с высоким содержанием углерода склонны к образованию закалочных структур и трещин при сварке. Предварительный нагрев уменьшает вероятность таких дефектов.
Чем больше толщина свариваемого металла, тем выше риск возникновения термических напряжений. Для таких изделий необходим предварительный нагрев, получается тогда равномерный прогрев металла.
Также если сварочные работы ведутся на морозе, предварительный нагрев позволяет компенсировать резкое охлаждение металла и сохранить требуемое качество соединения.
В конструкциях, подвергающихся значительным механическим нагрузкам или работающих в агрессивных условиях (например, трубопроводы или мосты), применение предварительного нагрева предотвращает появление хрупких дефектов и продлевает срок службы соединений.
Для низкоуглеродистых сталей температура предварительного нагрева может составлять от 100 до 200°C, тогда как для высокоуглеродистых или низколегированных сталей – от 250 до 400°C и выше.
Время выдержки металла при заданной температуре еще варьируется в зависимости от толщины изделия и его теплопроводности. Основной критерий – равномерный прогрев всей зоны сварки.
Что касается способов режима предварительного нагрева, их несколько:
Очень важно точно контролировать температуру в процессе нагрева и сварки. Для этого используются пирометры, термопары и другие измерительные приборы. Отклонение температуры от рекомендованной может привести к снижению качества сварного соединения и появлению дефектов.
Заключение
Мы рассмотрели основные и второстепенные режимы сварки, как РДС, так и полуавтоматической, и аргонодуговой, также контактной, стыковой, газовой, под флюсом и не только. Рассказали о параметрах и их влиянии на сварное соединение. Понимание режимов позволяет выбрать оптимальные условия выполнения сварочных работ, существенно повышает производительность и снижает вероятность возникновения дефектов.
Правильная настройка тока, напряжения, скорости подачи
электрода и других показателей играет ключевую роль в достижении
высококачественного шва. Знание режимов необходимо для безопасности и эффективности
процесса, а также для соответствия конечного изделия необходимым техническим
требованиям.