Сварка для новичков
Содержание статьи:
Сварка – одна из ключевых технологий, которая используется в различных отраслях, от строительства и автомобилестроения до художественной металлургии. Для многих она представляет собой сложный процесс, требующий специальных знаний и навыков. Однако, с правильным подходом и пониманием основ, может стать доступным и увлекательным занятием даже для новичков.
Что нужно знать перед работой – техника безопасности
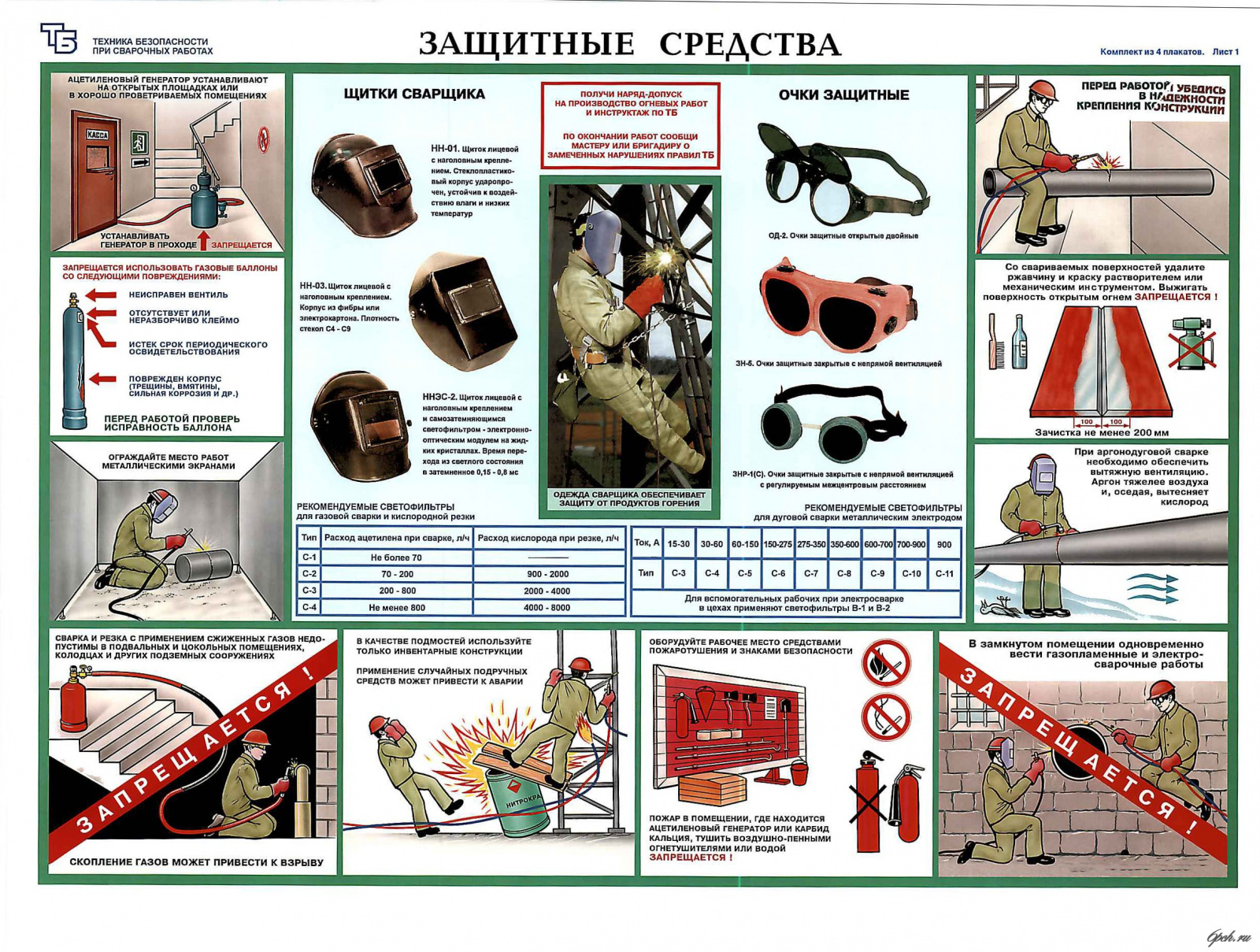
Сварка – это высокоответственный процесс, требующий особого внимания и строгого соблюдения мер безопасности. Данный вид работ несет в себе риски как для сварщика, так и для людей, находящихся поблизости. Компетентная организация рабочего процесса и следование основным правилам безопасности являются залогом предотвращения несчастных случаев и травм.
Рабочее место
Перед началом сварочных работ необходимо тщательно подготовить рабочее место.
Убедитесь, что в рабочей зоне нет горючих и легковоспламеняющихся материалов – бумага, дерево, ткани, масла, бензин и т.д.
Работайте в хорошо проветриваемом помещении, чтобы минимизировать риск вдыхания токсичных газов.
В зоне проведения сварочных работ должны быть доступны огнетушители и средства первой помощи.
Средства индивидуальной защиты
Не обойтись без средств индивидуальной защиты. Что потребуется обязательно:
- Сварочная маска – используйте сварочную маску с подходящими фильтрами для защиты глаз и лица от яркого света и искр. Она может быть с фиксированным или автоматическим затемнением, позволяя сварщику освободить руки и не отвлекаться от процесса. Не забывайте о защитных очках, если работа требует дополнительной защиты.
- Защитная одежа – надевайте специальную сварочную куртку, брюки и перчатки из огнестойких материалов, чтобы защитить кожу от искр и ультрафиолетового излучения.
- Рабочая обувь – должна быть из прочных материалов и иметь металлический носок для защиты ног от ударов и брызг расплавленного металла.
Средствами индивидуальной защиты точно не стоит пренебрегать. Каждый сварщик должен обеспечивать себя всеми необходимыми СИЗ для защиты своего здоровья и жизни. Верный выбор и правильное использование защитных средств не только уменьшают риск получения травм, но и позволяют сварщику сосредоточиться на выполнении своих задач. Создавая безопасные условия на рабочем месте, можно значительно повысить эффективность сварочных процессов и снизить вероятность несчастных случаев.
Проветривание
Поскольку сварка сопровождается выделением токсичных газов, дыма и высоких температур, правильная организация воздухообмена необходима для защиты здоровья сварщика и окружающих.
Есть несколько способов организации вентиляции при сварочных работах:
- Природная вентиляция. Это простейший метод, который основывается на естественном движении воздуха через открытые окна и двери. Хотя способ не всегда эффективен, он может быть достаточным для маломасштабных сварочных работ на улице или в хорошо проветриваемых помещениях.
- Механическая вентиляция. Включает использование вентиляторов и вытяжных систем. Эти системы активно удаляют загрязненные массы и насыщают помещение чистым воздухом. Вытяжные вентиляторы устанавливаются в местах, где происходит сварка, и помогают удалить дым и газы. Приточные вентиляторы отвечают за поступление свежего воздуха в рабочую зону.
- Локальные вытяжные системы. Располагаются непосредственно над сварочной зоной и захватывают дым и газы сразу после их образования. Наиболее эффективный метод, уверенно снижающий концентрацию вредных веществ в воздухе.
Перед началом сварочных работ проведите оценку уровня загрязнения воздуха и выберите подходящий метод вентиляции.
Убедитесь, что все системы воздухообмена работают исправно, регулярно проводите их обслуживание.
Установите датчики контроля уровня токсичных веществ в воздухе, чтобы оперативно реагировать на изменения в концентрации загрязняющих веществ.
Информируйте сотрудников о важности вентиляции и правилах ее организации. Объясните, как использовать оборудование и наладить эффективный воздухообмен.
Внимание к опасностям
Сварка связана с несколькими опасностями, которые необходимо учитывать.
Во-первых, избегайте контакта с влажными поверхностями, используйте изолирующие перчатки и обувь. Убедитесь, что сварочное оборудование заземлено.
Во-вторых, не вдыхайте сварочные газы. При необходимости используйте респираторы.
Держите на расстоянии легко воспламеняющиеся материалы и используйте теплоизоляционные экраны.
Проверка сварочного оборудования
После завершения сварочных работ нужно отключить источник тока от сети. Очистить рабочее место. Убрать все сварочные остатки, инструменты и материалы. Удостовериться, что нет тлеющих предметов.
Осмотрите сварочное оборудование на предмет повреждений и выполните его техническое обслуживание.
Соблюдение техники безопасности – залог здоровья не только сварщика, но и всех, кто находится в зоне работы. Правильная подготовка, использование средств индивидуальной защиты и внимание к потенциальным опасностям помогут избежать травм и обеспечить безопасность в процессе работы. Всегда помните, что безопасность, здоровье – всегда на первом месте, никогда не пренебрегайте мерами предосторожности!
Ручная дуговая
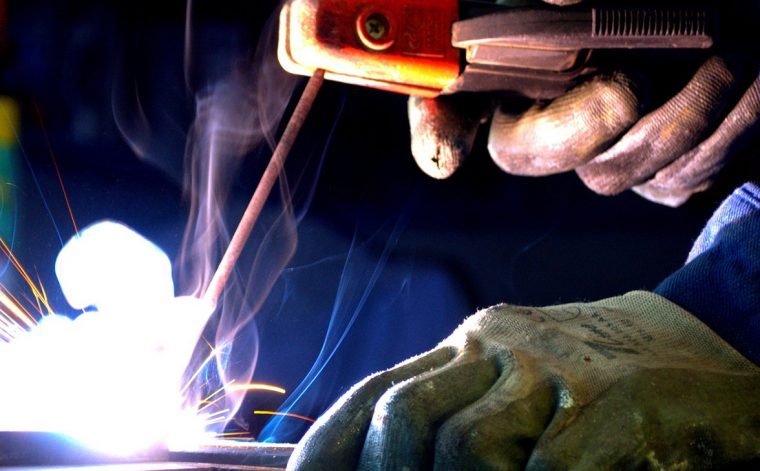
Наиболее распространенный, мобильный и доступный для новичков вариант – РДС – ручная дуговая сварка. Иноязычное обозначение – MMA (Manual Metal Arc), также известная как ручная дуговая сварка покрытым электродом, – одна из самых популярных и универсальных технологий соединения металлов. Этот метод основывается на использовании электрической дуги, которая возникает между электродом и соединяемыми деталями, расплавляя металл и создавая прочное и долговечное соединение.
Процесс осуществляется с использованием плавящегося электрода, покрытого специальным составом, который при нагревании образует шлак и защитный газ, предотвращающий окисление сварочной ванны.
Принцип работы MMA основан на создании дуги между покрытым электродом и свариваемой деталью. При подключении электрода к источнику питания и прикосновении его к металлу образуется электрическая дуга, которая расплавляет металл в точке соприкосновения, а также сам электрод. Покрытие электрода выполняет несколько функций:
- Защита сварочной ванны – при нагревании покрытие сгорает, образуя защитный газ, который изолирует сварочную ванну от воздуха и предотвращает окисление.
- Образование шлака – шлак, возникающий в процессе сгорания напыления, оседает на поверхности сварочного шва и защищает его от негативного воздействия окружающей среды до полного остывания.
- Стабилизация дуги – некоторые компоненты покрытия стабилизируют электродугу, позволяя сварщику более точно контролировать процесс.
После завершения сварки шлак необходимо удалить, чтобы получить чистый и прочный шов.
Для выполнения сварки РДС требуется минимальный набор оборудования. Во-первых, источник тока – сварочный аппарат.
Во-вторых, сварочные электроды – УОНИ 13/55, АНО-21, ОК-46, МР-3 или других марок. Расходный материал выбирается в зависимости от типа свариваемого металла, необходимой прочности шва и условий работы.
В-третьих, средства защиты – сварочная маска, перчатки и спецодежда, защищающие сварщика от брызг металла и интенсивного излучения дуги.
РДС обладает рядом преимуществ, которые делают ее популярной как среди профессионалов, так и среди любителей:
- Универсальность – этот метод можно использовать для сварки различных металлов, включая углеродистую и легированную сталь, чугун, нержавеющую сталь и цветные металлы. Только при правильном подборе электродов.
- Мобильность – оборудование MMA достаточно компактно и легко перемещается, можно без проблем работать как в мастерской, так и на удаленных объектах.
- Работа в различных условиях – РДС может выполняться практически в любых погодных условиях и в труднодоступных местах. Защитное покрытие электрода стабилизирует процесса даже при ветре или высокой влажности.
- Относительная простота – несмотря на то, что процесс требует определенных навыков, освоить его может практически любой человек, что делает этот метод доступным для широкого круга пользователей.
Хотя сварка MMA имеет немало достоинств, у нее также есть и свои ограничения. Например, низкая скорость процесса. По сравнению с полуавтоматической сваркой, в MMA скорость работы ниже. Также необходимость очистки шлака. После завершения каждого прохода требуется удаление шлака, это увеличивает общее время процесса.
Плюс сложность сваривания алюминия и нержавейки. Даже специальными электродами это сделать непросто. Поэтому, когда речь идет о точность и высококачественном шве, в данном случае выбирают другой метод – полуавтоматический или аргонодуговой.
Но все же благодаря доступности сварка MMA находит применение в различных отраслях:
- Строительство – для сварки стальных конструкций, соединения элементов каркасов зданий и мостов.
- Машиностроение – ремонт и сборка машин, а также для изготовления оборудования и деталей.
- Судостроение и нефтегазовая промышленность – работа в ограниченном пространстве и в сложных погодных условиях.
- Бытовые и ремонтные работы – метод идеален для небольших домашних проектов, ремонта сельскохозяйственного инвентаря и оборудования.
Сварка MMA – это надежный и универсальный метод соединения металлов, который благодаря своей простоте, мобильности и возможности работы в различных условиях остается популярным и востребованным. Отлично подходит для ремонта, строительства и производства в самых разных сферах.
Но перед тем как перейти к настройкам и непосредственно к ведению шва электродом с покрытием, новичку важно не ошибиться с выбором источника тока. От него зависит стабильность работы, качество шва, вообще все ключевые параметры процесса, от силы тока, напряжения до продолжительности нагрузки и опций, упрощающих сваривание.
Как выбрать аппарат
Источник тока электрической дуги – сварочный аппарат. Новичку лучше ориентироваться на РДС. При выборе учитывать целый ряд критериев:
- Тип источника;
- Сила тока;
- Род тока;
- Полезные функции;
- Продолжительность включения;
- Условия эксплуатации и защита от перегрева;
- Энергопотребление и совместимость с электросетью.
Итак, тип аппарата – трансформаторный, выпрямитель или инверторный. Сразу скажем, новичкам нужны инверторы. Компактные, просты в настройке, потребляют меньше электроэнергии, чем устаревшие трансформаторы, не нуждаются в сложном и затратном обслуживании. Наиболее популярное решение на рынке также по причине функциональности: поддержка функционала, упрощающего сварку.
Современные трансформаторы – мощные, более подходят для промышленных условий.
Выпрямители – преобразуют переменный ток в постоянный, что отражается на стабильности дуги. Тяжелее инверторов, но легче трансформаторов. Чаще всего выпрямители используются в промышленных условиях, где нужна высокая надежность.
Далее – сила тока. Чем больше ампер выдает аппарат, тем толще металл можно сваривать.
Для бытовых нужд и сварки металлов толщиной до 4-5 мм достаточно источника с диапазоном тока 100–160 А.
Для сварки более толстых металлов (6–10 мм) или в условиях повышенной нагрузки потребуется аппарат на 160–250 А.
Что касается промышленного использования, можно рассмотреть источники мощностью от 250 А.
Род тока – переменный или постоянный. Постоянный (DC) подходит для сварки большинства материалов, особенно тонких и легированных сталей. DC обеспечивает стабильную дугу, позволяет получать качественные швы даже при сварке сложных металлов.
Переменный ток (AC) используется для сварки чугунов и некоторых алюминиевых сплавов, а также при работе на больших токах. Однако дуга менее стабильна, может усложнять работу для новичков.
Важна универсальность – смотрите на модели с переключателем между AC и DC.
Полезные функции в инверторе: Hot Start – увеличивает ток при начале сварки, упрощая поджиг дуги; Anti-Stick – предотвращает прилипание электрода к металлу, автоматически снижая ток, если стержень вот-вот приварится к поверхности; Arc Force – стабилизирует дугу, автоматически увеличивая ток при снижении напряжения, что полезно при работе с толстым металлом или электродами большого диаметра.
Продолжительность включения – параметр, который указывает, сколько времени аппарат может работать без перегрева в течение 10 минут. Чем выше ПВ, тем дольше аппарат выдерживает интенсивные нагрузки.
Условия эксплуатации и защита от перегрева – для работы на улице или при повышенной влажности лучше выбрать аппарат с хорошей защитой от пыли и влаги. Некоторые модели имеют класс защиты IP21 или выше, что гарантирует защиту от попадания пыли и капель воды.
Также важно, чтобы в источнике была реализована система защиты от перегрева. В большинстве современных инверторов присутствуют вентиляторы и датчики, которые отключают оборудование в случае критического повышения температуры.
Энергопотребление и совместимость с электросетью – в условиях бытовой сети выбирают аппарат, способный стабильно работать от стандартной розетки (220 В). Инверторы более экономичны и отлично функционируют при колебаниях напряжения, что особенно важно для сельских или отдаленных районов. Некоторые модели оснащены функцией защиты от перепадов напряжения, что повышает их устойчивость. Для промышленной сети 380 В, в свою очередь, выбирают трехфазный источник.
Электроды
Итак, определились с аппаратом РДС. Теперь переходим на электроды.
Первым и важнейшим фактором является материал свариваемой заготовки. В зависимости от типа металла, который будет подвергаться сварке, выбирают разные электроды:
- Углеродистая сталь – для углеродистых и низколегированных сталей используют электроды общего назначения, например, марки УОНИ, МР-3, АНО.
- Нержавеющая сталь – подходят электроды с высоким содержанием никеля и хрома, например, ОЗЛ-8, ЭА-395/9.
- Чугун – лучше всего подойдут специальные электроды с никелевым покрытием, например, ОЗЧ-2.
- Цветные металлы – требуются специализированных электроды с определенным химическим составом. Например, для меди – КМ-100, МН-5 и АМНц/ЛКЗ-АБ. Для никеля – МЗОК и ХН-1. АФ-4аКр и А-2 – алюминиевые сплавы.
Далее смотрим на диаметр электрода. Зависит от толщины свариваемого металла и мощности сварочного аппарата. Чем больше диаметр, тем более мощный сварочный аппарат потребуется для его плавления. Основные рекомендации таковы:
- Металл толщиной до 3 мм – электрод диаметром 2-2,5 мм.
- Металл толщиной 3-5 мм – электрод 3 мм.
- Металл толщиной более 5 мм – электрод диаметром 4 мм и более.
Диаметр также определяет скорость сварки, глубину проплавления и толщину шва, поэтому важно подобрать его в зависимости от задачи и характеристик металла.
Обязательно учитываем покрытие. Влияет на характеристики сварки – зажигание дуги, защитные свойства, формирование шва и устойчивость к внешним воздействиям. Основные варианты здесь:
- Рутиловое – подходит для универсальных работ, легко зажигается и обеспечивает хорошую стабильность дуги. Создает гладкий шов и легко удаляемый шлак, что особенно удобно при сварке в труднодоступных местах.
- Основное покрытие – подходит для ответственных соединений, так как дает хорошую прочность шва и стойкость к воздействию неблагоприятных условий. Электроды с основным покрытием требуют более мощного источника тока и более опытного сварщика.
- Целлюлозное – глубокое проплавление, сварка трубопроводов и других конструкций, требующих высокого уровня защиты от коррозии.
- Кислое покрытие – легкое зажигание дуги и гладкий шов, но менее устойчиво к коррозии.
В зависимости от положения сварки – горизонтального, вертикального, потолочного или нижнего – электрод может вести себя по-разному. Например:
- Для горизонтальных и нижних положений подходят большинство электродов общего назначения.
- Для вертикального и потолочного – лучше выбирать электроды с рутиловым или основным покрытием, так как они поддерживают более стабильную дугу и легкий контроль сварочной ванны.
Помните, что сварочные стержни необходимо хранить в сухом месте, так как покрытие может впитывать влагу, что приведет к нестабильности дуги, появлению пористости и трещин в шве. Перед сваркой желательно прокалить электроды, если производитель указывает такую необходимость, для удаления излишней влаги и улучшения качества сварки.
Для каждого типа расходника производитель указывает рекомендации по прокаливанию, так что перед использованием изучите инструкцию.
Сила тока
Чтобы начать варить, нужно подключить кабели массы и держателя электрода к источнику тока. Прикрепить массу к заготовке, предварительно ее подготовив. Далее включить аппарат и настроить силу тока.
Выбор силы тока зависит от нескольких факторов.
Первый – диаметр электрода. Обычно существует прямая зависимость: чем больше диаметр электрода, тем больше требуется сила тока для его плавления. Примерные значения:
- 2 мм – 50–70 А
- 2.5 мм – 70–100 А
- 3 мм – 90–130 А
- 4 мм – 120–180 А
- 5 мм – 160–220 А
Производители часто указывают рекомендуемый диапазон силы тока на упаковке электродов, и при выборе стоит ориентироваться именно на их рекомендации.
Второй фактор – толщина свариваемого металла. Тонкие материалы (1–2 мм) – низкий ток, около 40–60 А, чтобы избежать прожигания. Средние по толщине (2–4 мм) – ток 60–120 А. Толстые материалы (более 5 мм) – 120–200 А и выше, в зависимости от толщины и диаметра электрода.
Для тонких металлов важно избегать перегрева, поэтому сварщики используют небольшую силу тока и выбирают электроды меньшего диаметра.
Положение сварки (нижнее, вертикальное, горизонтальное, потолочное) также играет роль при выборе силы тока.
Нижнее положение – более высокий ток, так как сила тяжести помогает удерживать сварочную ванну.
Вертикальное и потолочное – требуют меньшей силы тока. Избыточный ток приведет к стеканию и разбрызгиванию металла, ухудшит качество шва и усложнит управление сварочной ванной.
При сварке в сложных положениях важно настроить ток на нижнюю границу рекомендованного диапазона, чтобы легче контролировать процесс и избежать дефектов.
Как разжечь электрод
Перед тем как приступить к разжиганию электрода, необходимо подготовить рабочее место, оборудование и свариваемые материалы. Это поможет упростить процесс и избежать неприятных ситуаций.
Очистите заготовки от посторонних включений, при необходимости обезжирьте. Надежно закрепите на столе.
Подсоедините сварочные кабели. Один кабель подключается к массе (зажиму, который крепится к свариваемой детали или сварочному столу), а другой – к держателю электрода.
Выберите полярность – для большинства покрытых электродов используется обратная полярность (электрод – «+», масса – «–»), но лучше уточнить эту информацию в инструкции к электродам.
Убедитесь, что электроды сухие и не имеют трещин на покрытии. Если стержень влажный, его можно прокалить согласно рекомендациям производителя. Закрепить электрод на держателе.
Подключите аппарат к сети, настройте ток. Наденьте защитную маску. На черновом металле проверьте шов.
Разжигание электрода – первый этап сварки. Цель – создать стабильную дугу между стержнем и металлом. Есть два основных метода зажигания: метод касания и метод чирканья.
Метод касания заключается в кратковременном прикосновении электрода к металлу:
- Удерживайте электрод под углом 70-80 градусов к поверхности свариваемого металла.
- Коснитесь электродом поверхности и сразу же поднимите его на 1-3 мм. Этот зазор зажжет электродугу и создаст стабильное горение.
Если дуга не зажглась, повторите попытку. Главное – не держите электрод долгое время на одном месте, так как получите залипание.
Метод касания удобен для начинающих, позволяет точно контролировать точку разжигания дуги.
Другой метод – чирканья, напоминает движение зажигания спички:
- Удерживайте электрод под углом 30-45 градусов к поверхности.
- Чиркните концом электрода по металлу, создавая искры, и сразу же поднимите его на высоту 1-3 мм.
- Если дуга зажглась, удерживайте стабильное расстояние для поддержания равномерного горения дуги.
Данный метод подходит для опытных сварщиков, требует точности и умения поддерживать равномерное движение.
Держите руку уверенно: любые колебания или дрожание могут привести к прилипанию электрода или погасанию дуги. Не отрывайте электрод резко: это может привести к прекращению горения дуги. Вместо этого поднимайте плавно. Практикуйтесь: если вы новичок, то немного потренируйтесь на куске металла перед тем, как начать основную работу.
Иногда электрод может прилипнуть к металлу. Это распространенная проблема, особенно у новичков. Чтобы устранить ее, следуйте советам:
- Резко наклоните электрод в сторону.
- Попробуйте аккуратно постучать по стрежню, чтобы сбить остатки шлака и металла. Затем отделите от заготовки, медленно поднимая вверх.
- Проверьте качество электрода – возможно, он влажный или имеет дефекты на покрытии, которые мешают нормальному зажиганию.
Если электрод сильно прилип, выключите сварочный аппарат и аккуратно освободите стержень, плавно двигая его в разные стороны, чтобы избежать серьезного повреждения покрытия.
После того как дуга разожжена, важно поддерживать ее стабильное горение. Для этого нужно правильно управлять расстоянием между электродом и металлом.
Оптимальное расстояние – это 1-3 мм от конца электрода до металла. Если расстояние будет слишком большим, дуга может погаснуть, а если слишком маленьким, электрод прилипнет.
Движение электрода должно быть плавным и контролируемым. Избегайте резких движений, так как это может привести к потере контроля над сварочной ванной и появлению дефектов.
Чтобы сохранить стабильное горение дуги, удерживайте электрод под постоянным углом и следите за тем, чтобы расстояние до металла не колебалось.
Как правильно вести электрод
Угол наклона электрода оказывает значительное влияние на форму и качество сварного шва. Сварку обычно ведут с наклоном стержня на 15–30 градусов в направлении движения (так называемый «угол назад»).
Угол назад защищает сварочную ванну от воздействия кислорода и азота в воздухе, предотвращая образование пор и дефектов на поверхности шва. Если угол слишком велик, сварочная ванна будет чрезмерно глубокой и возникнет риск прожога металла. Слишком малый угол, наоборот, приводит к непровару.
Оптимальный угол наклона равномерно распределяет тепло, стабильно плавится электрод, металл как надо распределяется по поверхности шва.
Скорость движения электрода – один из важнейших параметров, влияющих на форму и качество шва. Слишком высокая скорость – уменьшение глубины провара и образование недостаточно широкой шовной полосы. Как результата слабое соединение.
При слишком низкой скорости ведения шов может получиться слишком широким и высоким, что снижает его прочность и эстетический вид. Оптимальная скорость должна равномерно распределять металл и образовывать гладкую поверхности шва без капель и наплывов.
Правильная длина дуги также критична при сварке MMA. Оптимальная длина дуги зависит от диаметра электрода и типа покрытия, но чаще всего она составляет 1-1,5 диаметра электрода. При увеличении длины выделяется больше тепла, возрастает вероятность прожога металла и образования пор. При слишком короткой дуге электрод может прилипать к металлу, нарушать плавление и ведение сварки.
Следите за звуком дуги – ровный и мягкий шум указывает на правильную длину дуги. Если звук становится слишком громким и прерывистым, это признак того, что электродуга слишком длинная. Если электрод липнет к металлу, дуга слишком короткая.
Специалисты применяют следующие методы ведения электрода:
- Линейный,
- Зигзагообразный,
- Круговой,
- “Восьмерка”,
- Маятниковый,
- Поступательно-возвратный.
Линейный используется при сварке тонколистовых материалов и для выполнения первого прохода при многопроходном режиме. Электрод ведется строго по прямой линии, создавая узкий и глубокий шов. Такой метод позволяет минимизировать тепловложение, избегая прожогов на тонком металле.
Зигзагообразный – предполагает движение электрода в виде зигзага поперек шва. Чтобы увеличить ширину шва и равномерно распределить металл по всей ширине соединения. Актуален при сварке толстых металлов или при необходимости выполнения широких швов.
Зигзагообразным движением плавно распределяют сварочную ванну, а также увеличивают ширину проплавления, этим в конечном итоге повышают прочность соединения.
При круговом методе электрод движется по кругу или овалу вдоль шва. Подходит для заполнения объемных зазоров и равномерно распределяет металл и шлак. Актуален как для горизонтальной, так и для вертикальной сварки. Помогает избежать образования наплывов и трещин.
Круговое движение требует опыта и уверенного контроля электрода, поскольку неправильный диаметр круга может привести к недостаточному провару или образованию наплывов.
Метод «восьмерки» предполагает, что электрод движется в форме цифры восемь. Это сложный, но эффективный способ ведения, который помогает сварщику точно контролировать сварочную ванну и равномерно распределять металл. Метод часто используют для выполнения сложных швов, требующих максимальной прочности и устойчивости к деформациям. Требует навыка, так как слишком быстрые или медленные движения становятся причиной дефектов.
Маятниковый – заключается в движении электрода по ширине шва, при этом каждое новое положение напоминает маятник. Электрод медленно перемещается от одной стороны шва к другой, с небольшими задержками по краям, как результат качественный провар краев и равномерное заполнение шва. Маятниковые движения дают возможность сконцентрировать тепло на краях шва, за счет чего повышается надежность соединения, перегрев центральной части шва не происходит.
Поступательно-возвратный – движение электрода вперед-назад по направлению шва. Сварщик продвигается немного вперед, а затем возвращается назад, и так по всей длине соединения. Метод подходит для создания плотного шва и предотвращения пористости. Но требует внимательности, так как необходимо поддерживать стабильную дугу и аккуратно возвращаться на предыдущий участок, чтобы не образовывались поры и пустоты.
Для начинающим сварщикам лучше начинать с простых соединений и горизонтального положения. Чтобы освоить базовые принципы ведения электрода и привыкнуть к работе с плавящимися электродами. Несколько практических советов:
- Тренируйтесь на металлоломе. Найдите ненужный металл и попробуйте выполнять различные типы швов, корректируя угол, скорость и длину дуги.
- Обратите внимание на звук и визуальные подсказки. Равномерный шум и стабильное состояние сварочной ванны – признаки того, что параметры сварки выбраны правильно.
- Не спешите. Сварка требует терпения и контроля. Ведение электрода должно быть размеренным, а движения – плавными.
Правильное ведение электрода при РДС – основа качественного и прочного шва. Контролируя угол наклона, скорость движения, длину дуги и выбирая подходящий метод ведения, вы сможете получить надежное соединение металлов. Практика и внимательное отношение к каждому из этих параметров – нехитрый секрет профессиональных результатов в сварке!
Рекомендации для новичков
Новичкам рекомендуется начать с инверторного сварочного аппарата для MMA-сварки. Инверторы компактны, легки в управлении и позволяют легко контролировать силу тока, что особенно полезно для начинающих. При выборе аппарата обратите внимание на его мощность и диапазон регулировки тока: для большинства бытовых задач будет достаточно аппарата с максимальной силой тока в пределах 160-200 А.
Электроды для MMA-сварки выпускаются разных диаметров и типов, и каждый из них подходит для определенных условий и материалов. Для начинающих стоит выбрать универсальные рутиловые (например, марки ОК-46). Они дают стабильную дугу, легко зажигаются и образуют меньше шлака. Оптимальный диаметр для первых тренировок — 2,5-3,2 мм, так как они проще в управлении и равномерно проваривают.
Сварка – потенциально опасный процесс, и поэтому важно соблюдать меры безопасности. Для работы потребуются:
- Сварочная маска с автоматическим затемнением, чтобы защитить глаза от яркой дуги.
- Кожаные перчатки и защитная одежда из плотной ткани, чтобы предотвратить ожоги и повреждения.
- Рабочая обувь с закрытым носком для защиты ног от искр.
Одна из самых распространенных ошибок у новичков – недостаточная подготовка металла. Качественный шов возможен только при чистой поверхности, так как грязь, ржавчина и масло могут стать причиной дефектов, пор и слабого соединения.
Удалите грязь, ржавчину и старую краску с помощью металлической щетки, наждачной бумаги или угловой шлифовальной машины.
Используйте растворитель или обезжириватель, чтобы удалить остатки масла и жира.
При сварке толстых материалов края необходимо обработать – сделать фаску для лучшего провара и надежного соединения.
Сила тока – ключевой параметр, влияющий на качество сварки. При слишком низком токе дуга будет нестабильной, а шов – слабым и непроваренным. Слишком высокий ток приводит к разбрызгиванию и прожогам. Оптимальная сила зависит от диаметра электрода и типа металла. Обычно на каждый миллиметр диаметра электрода требуется 30–40 А. Например, для электрода диаметром 3 мм установите силу тока в пределах 90–120 А.
Для стабильного шва необходимо поддерживать правильную длину дуги – расстояние между концом электрода и поверхностью металла. Для новичков оптимально придерживаться длины, равной диаметру электрода. Слишком длинная дуга приводит к разбрызгиванию и образованию пор, а слишком короткая – к залипанию.
Горизонтальная сварка – держите электрод под углом 15–30 градусов к направлению движения. Этот угол способствует равномерному плавлению металла и защите сварочной ванны от окисления. При сварке в вертикальном положении или в труднодоступных местах угол наклона может изменяться, но общее правило остается: избегайте слишком резких углов, чтобы контролировать плавление металла.
В зависимости от условий работы и типа соединения, используют разные методы ведения стержня.
Линейный – подходит для сварки тонких металлов и для первого прохода.
Зигзагообразный – сварка толстых металлов, создание широкого шва.
Круговой – сварка широких зазоров и равномерное распределение металла.
Новичкам лучше всего начать с линейного метода, так как он проще в освоении и позволяет сконцентрироваться на поддержании стабильной дуги и угла наклона.
Поддерживайте равномерную скорость. Слишком медленное ведение приводит к перегреву и образованию широкого шва, тогда как слишком быстрая сварка создает узкий и слабый шов. Найдите скорость, при которой сварочная ванна остается стабильной и равномерной по всей длине.
Во время сварки обращайте внимание на цвет и форму сварочной ванны. Она должна быть ярко-оранжевой и находиться под полным контролем сварщика. Если металл начинает разбрызгиваться или появляется большое количество искр, возможно, ток слишком высок или длина дуги слишком большая.
Перед сваркой ответственных деталей попробуйте выполнить несколько тестовых швов на образцах металла. Отрегулируйте параметры тока и выберите оптимальный метод ведения, набейте руку в процессе.
Чтобы зажечь дугу, наклоняйте электрод под углом и слегка касайтесь металла как при черкании спичкой.
Сварка РДС – доступная и универсальная, ее реально освоить! Соблюдая основные рекомендации и практикуя базовые навыки – установка силы тока, выбор длины дуги и угла наклона электрода – новички смогут быстро овладеть ею и выполнять качественные швы. Помните, что важнейший элемент успеха – это практика, поэтому не бойтесь пробовать и анализировать свои ошибки!
Полуавтоматическая
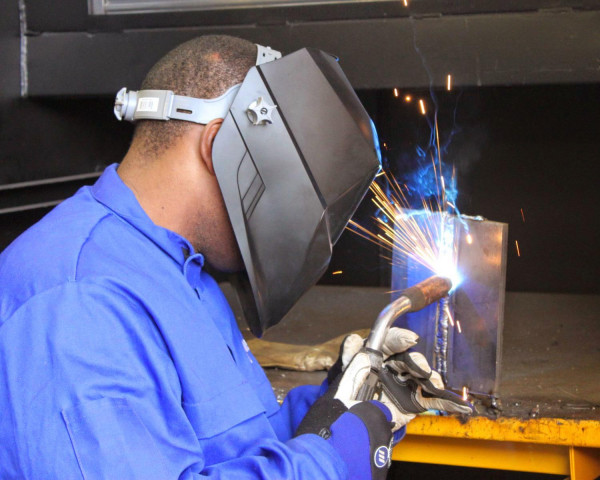
Когда требуется качественная сварка нержавеющей стали, на первом месте будет полуавтоматический метод. Иноязычное обозначение MIG/MAG (Metal Inert Gas / Metal Active Gas) – в среде инертного или активного газа. Электрод в виде проволоки специальным механизмом подается автоматически, а шов ведет, как и в случае РДС, сварщик самостоятельно. Поэтому и такое название – полуавтоматическая. Один из наиболее популярных видов сварки, активно применяемый в машиностроении, металлообработке, строительстве и других областях. Отличается высокой производительностью и качеством соединений.
Основы MIG/MAG
В основе MIG/MAG электрическая дуга, возникающая между электродом и свариваемой деталью. Электрод представляет собой проволоку, которая непрерывно подается к месту сварки, расплавляется и, благодаря этому, формирует сварной шов. Защитный газ подается из сопла горелки, предотвращает окисление и негативное воздействие окружающей среды на зону плавления.
MIG-сварка (Metal Inert Gas) – процесс в защитной среде инертного газа, чаще всего аргона или гелия. Применяется для работы с цветными металлами, например, алюминием и медью, которые требуют инертной среды, чтобы предотвратить окисление.
MAG-сварка (Metal Active Gas) – с использованием активного защитного газа (обычно углекислого или смеси углекислого газа с аргоном). Больше подходит для черных металлов, так как активный газ способствует улучшению механических свойств шва.
Новичкам следует хорошо знать основное оборудование полуавтоматического метода:
- Сварочный аппарат – инверторный или трансформаторный – подает нужный для дуги ток, регулирует параметры процесса: сила тока, напряжения, скорость подачи присадки и т.д.
- Проволока – используется в качестве электрода и плавящегося материала формирования шва. Намотана на катушку и автоматически подается через подающий механизм. Может быть разного диаметра (обычно от 0,8 до 1,6 мм) и материала (сталь, алюминий, нержавеющая сталь и т.д.), в зависимости от типа свариваемого металла. Выбор проволоки напрямую влияет на качество шва, его прочность и устойчивость к коррозии.
- Механизм подачи проволоки – обеспечивает постоянный поток электродной проволоки к месту сварки. Состоит из мотора привода, роликов для протягивания проволоки к горелке, регулятора скорости подачи, который синхронизирован с настройками сварочного аппарата и определяет количество металла, попадающего в сварочную ванну.
- Баллон с газом и редуктор – первый – источник защитной среды, а редуктор поддерживает оптимальное давление газа. Также применяют расходомер – устройство, контролирующее количество газа, поступающего в зону сварки, чтобы создать стабильную газовую защиту. Оптимальный расход важен для качества сварки: недостаток газа может вызвать дефекты в шве, а избыточное потребление приведет к нерациональному расходу ресурсов.
- Горелка – рабочий инструмент сварщика, через нее подаются проволока и газ, образуется сварочная дуга.
Подключение – через кабель-шланговый пакет. Это неотъемлемый компонент полуавтоматического аппарата, который соединяет основные части системы и реализует подачу всех необходимых для сварки ресурсов. Выполняет сразу несколько функций, так как в нем объединены электрические кабели, газовые шланги и механизмы подачи проволоки. Связывает сварочную горелку с основным блоком аппарата и обеспечивает передачу электрического тока, защитного газа, проволоки. Также предполагает сигнальные и управляющие провода – передают сигналы от кнопки горелки к блоку управления аппарата, чтобы запускать и останавливать процесс подачи тока и газа.
Перед началом сварки мастер закрепляет свариваемую деталь и устанавливает настройки на сварочном аппарате. Основные параметры, которые следует выставить:
- Сварочный ток и напряжение – определяют силу и стабильность дуги. Зависят от типа металла, толщины и условий сварки.
- Скорость подачи проволоки – эта настройка влияет на количество материала, подаваемого в сварочную ванну, также на толщину и качество шва.
- Тип и объем защитного газа – для сварки разных металлов применяются разные газы. Для MIG используют инертный газ (аргон или гелий), а для MAG – активный газ (углекислый газ или его смесь с аргоном).
После нажатия на курок сварочной горелки начинается подача сварочной проволоки к месту сварки, подается ток, и возникает электрическая дуга между проволокой и металлом. Дуга – это высокотемпературная область, в которой проволока и кромка детали начинают плавиться. Температура в зоне дуги может достигать 6000 градусов Цельсия, что достаточно для плавления большинства металлов.
В процессе из сопла сварочной горелки непрерывно поступает защитный газ, который окружает сварочную ванну и дугу. Газовая защита предотвращает контакт расплавленного металла с кислородом, азотом и водяными парами, исключает образование пор и дефектов в сварочном шве. Если газовое облако будет нарушено, шов окажется подвержен окислению и потеряет прочность.
Сварочная проволока автоматически подается с катушки к месту сварки с заданной скоростью. Она выполняет сразу две функции:
- Формирование металла шва – плавится и добавляет материал в сварочную ванну, создавая соединение между деталями.
- Электрод – проволока проводит ток, поддерживая электрическую дугу.
Скорость подачи проволоки синхронизирована с силой тока. Если скорость будет слишком низкой, проволока будет не успевать за дугой, что приведет к образованию капель и прерыванию дуги. Если скорость подачи окажется слишком высокой, это вызовет избыточное количество материала и нестабильную дугу.
По мере перемещения горелки вдоль стыка расплавленная сварочная ванна остывает и формирует шов.
В зоне сварки металл проволоки и основного материала смешиваются, образуя однородный шов. Правильно подобранные настройки сварочного аппарата и равномерное перемещение горелки гарантируют прочное, качественное соединение.
После завершения сварки прекращается подача проволоки и защитного газа. Мастер проверяет шов на предмет дефектов и при необходимости проводит шлифовку или другие отделочные операции. Охлаждение обычно происходит быстро, но в некоторых случаях может потребоваться дополнительная термическая обработка для улучшения свойств соединения.
Настройки
Перед сваркой нужно настроить аппарат: выбрать силу тока, напряжение, полярность, скорость подачи проволоки, газ, определиться с его расходом.
Сила тока – определяется в зависимости от толщины свариваемого металла, диаметра проволоки и типа сварного соединения. Чем толще металл, тем выше значение данного параметра. Например, заготовка толщиной 0.5-1 мм – ставим ток 50-80 А, 3 мм – ток 100-130 А. При работе проволокой диаметром 0,8 мм. Но это ориентировочные значения. Обычно производители электродной проволоки указывают рекомендованные диапазоны силы тока для конкретных условий работы, на которые можно ориентироваться.
Напряжение – определяет длину сварочной дуги и влияет на стабильность горения. При слишком высоком электродуга становится длинной и нестабильной, не исключено брызгообразование. При слишком низком напряжении дуга будет короткой, затруднит подачу проволоки и ухудшит качество шва. Напряжение подбирается исходя из силы тока и диаметра проволоки, также есть рекомендуемые диапазоны от производителя проволоки или оборудования. Например, для тока 100-130 А – напряжение 20-22 В.
Полярность – при полуавтоматической сварке используют два варианта: прямую и обратную полярность.
Обратная (положительный электрод) чаще применяется для низкоуглеродистых сталей, на ней хорошо проплавляется металл, электродуга стабильная.
Прямая (отрицательный электрод) используется реже, в основном для тонколистового материала, алюминия и других сплавов, когда нужно снизить тепловложение.
Скорость подачи проволоки – зависит от силы тока и диаметра проволоки. Увеличение скорости повышает силу тока, а уменьшение – снижает. Обычно подбирается опытным путем и регулируется так, чтобы сварочная дуга была стабильной, а сварной шов – равномерным. Слишком большая подача может привести к прожиганию, а недостаточная – к непровару. Примеры для диаметра проволоки 0,8 мм:
Сила тока 80 А – скорость подачи проволоки около 3,5–4,0 м/мин. 100 А – около 4,0–5,0 м/мин. 130 А – около 5,5–6,5 м/мин.
Для диаметра проволоки 1,0 мм скорость подачи увеличивается, так как толщина присадки больше, например: 100 А – скорость подачи около 3,0–3,5 м/мин. Сила тока 140 А – скорость подачи в пределах 4,5–5,0 м/мин.
Что касается газа, выбирается в зависимости от свариваемого металла.
Для углеродистой и низколегированной стали оптимальна смесь 80% аргона и 20% CO₂, либо чистый CO₂, который дешевле, но дает больше брызг.
Для нержавеющей стали часто задействуют смесь аргона и CO₂ в пропорции 98% аргона и 2% CO₂, или добавляют кислород (например, 98% аргона и 2% O₂).
Алюминий и сплавы – чистый аргон.
Оптимальный расход газа зависит от диаметра проволоки и условий работы. Примерные значения:
- Диаметр проволоки 0,8-1,0 мм – расход 8-12 литров в минуту.
- 1,2-1,6 мм –12-16 литров в минуту.
При сварке на улице, при ветре или в сквозняке расход может быть увеличен до 20-25 литров в минуту.
Слишком низкий расход газа приведет к недостаточной защите сварочной ванны, а чрезмерный – к образованию турбулентных потоков, ухудшающих защиту дуги.
Пример настройки для углеродистой стали толщиной 3 мм, проволока 1 мм, в помещении:
- Ток: 130 А.
- Напряжение: 20–22 В.
- Полярность: обратная (электрод положительный).
- Скорость подачи проволоки: 5,0–5,5 м/мин.
- Газ: смесь 80% аргона и 20% CO₂.
- Расход газа: 10-12 литров в минуту.
Эти настройки могут корректироваться в зависимости от конкретного оборудования и условий работы.
Как выбрать сварочную проволоку
Электрод и один из основных расходных материалов полуавтоматической сварки – проволока. При ее выборе учитывают ряд параметров. Отметим основные:
- Диаметр;
- Назначение;
- Структура;
- Состав.
Итак, диаметр – в зависимости от толщины свариваемого металла. 0,6-0,8 мм подходит для тонколистовой стали (до 3 мм), кузовного ремонта и работ, требующих высокой точности. 1,0-1,2 мм – более толстые материалы (3–12 мм). 1,6 мм и выше – для сварки габаритных изделий и промышленных объектов.
Назначение – для стандартных сварочных операций обычно используют проволоку марки СВ, которая универсально подходит ко всем видам стали. Другой вариант – проволока НП, оптимальная для наплавочных работ.
Когда речь идет о сварке в условиях с особыми требованиями – например, при соединении сложных сплавов, работе с чугуном, сварке под водой или в других специфических средах – подход к выбору материала значительно меняется. В таких случаях важно подобрать присадочный материал, химически и физически совместимый с основным металлом. Чтобы избежать несовместимости материалов, повысить прочность и надежность шва, а также минимизировать риски возникновения дефектов и коррозии, особенно в агрессивных или нестабильных средах.
Структура – по этому параметру справедливо выделить проволоку сплошную, порошковую и активированную.
Сплошная – наиболее распространена, представляет собой металлический сердечник одинакового диаметра по всей длине. Производится из меди, алюминия, титана и различных марок стали, что позволяет ее применять для сварки черных и цветных металлов. Демонстрирует высокую производительность и стабильное качество шва при работе в защитной среде с использованием инертных или активных газов. Находит широкое применение в промышленном и производственном сварочном оборудовании, где требуется высокая скорость сварки и ровный шов.
Порошковая – представляет собой тонкостенную металлическую трубку, заполненную порошковым составом с металлическими добавками. При горении дуги порошок внутри образует шлаковую оболочку и углекислый газ, которые создают защитный барьер вокруг сварочной ванны. Этот защитный эффект предотвращает окисление плавящегося металла, повышая качество и прочность шва. Доля порошкового наполнителя может варьироваться от 15 до 40% массы проволоки, в зависимости от требований к шву и свойств металла. Порошковая проволока идеально подходит для сварки в условиях повышенной влажности или при работе на открытом воздухе, так как она не требует дополнительного защитного газа.
Активированная – также имеет трубчатую структуру, но содержит меньший процент порошкового наполнителя – не более 7%. Этот тип проволоки включает в состав раскислители, которые ускоряют поджиг дуги и улучшают качество шва. В качестве раскислителей применяются такие вещества, как щелочные карбонаты, оксиды кремния (Si), титана (Ti), магния (Mg), а также фторид кальция. Для корпуса этой проволоки используют низкоуглеродистую сталь, например, Св-08Г2С. Поддерживает высокую стабильность горения дуги и прочность соединения.
Активированная проволока востребована в тех случаях, когда требуется быстрая и стабильная дуга, например, при сварке конструкций в промышленных масштабах. За счет содержащихся в составе раскислителей демонстрирует хорошие свойства при сварке конструкционных сталей, позволяет получать ровный и плотный шов с минимальным уровнем пористости и дефектов.
Теперь о составе, или материале.
Для достижения качественного и долговечного соединения необходимо внимательно подбирать сварочную проволоку, ориентируясь на ее химический состав, чтобы он соответствовал свариваемому металлу.
Углеродная сталь – наиболее распространенный тип сварочной проволоки. Состоит в основном из железа и углерода, а содержание последнего обычно варьируется от 0,05% до 2,0%. Применяется для сварки различных конструкций, в том числе строительных и машиностроительных. Может быть как обыкновенной, так и легированной, в зависимости от добавок, улучшающих ее характеристики.
Легированная сварочная проволока, в свою очередь, содержит легирующие элементы – хром, никель, молибден и другие, улучшающие механические свойства свариваемого соединения. Часто используется для сварки стали, обладающей высокой прочностью или коррозионной стойкостью.
Проволока из нержавеющей стали содержит хром (обычно более 10,5%) и никель, они придают ей отличные антикоррозийные свойства. Решение для сварки конструкций, подвергающихся воздействию влаги или коррозионных агентов. Нержавеющая проволока – аустенитная или ферритная, в зависимости от структуры и характеристик.
Алюминиевая – используется для сварки алюминиевых деталей и конструкций. Она обладает легким весом и высокой коррозионной стойкостью, идеальна для применения в авиационной и автомобильной отраслях. В зависимости от содержания магния, кремния и других легирующих элементов, алюминиевая проволока может иметь различные механические свойства.
Порошковая – состоит из металлического порошка, который в процессе сварки расплавляется и образует сварочный шов. Она может быть изготовлена из различных металлов и сплавов, включая сталь и алюминий. Такой вид присадки дает более высокую производительность и качество, а также снижает количество брызг.
Что касается маркировки, разберем примеры.
Итак, СВ-08Г2С:
- СВ – стальная проволока.
- 08 – содержание углерода (0,08%).
- Г2 – содержание легирующих добавок, например, марганца и никеля.
- С – легированная проволока.
СВ-08Х18Н10Т:
- СВ – стальная проволока.
- 08 – содержание углерода (0,08%).
- Х – наличие хрома.
- 18 – содержание никеля (18%).
- Н10 – 10% содержания никеля.
- Т – легированная проволока с добавлением титана.
Понимание маркировки и основ подбора сварочной проволоки имеет решающее значение для достижения высококачественных сварных соединений. Неверный выбор материала может привести к снижению прочности соединений, возникновению трещин и другим недостаткам, что в конечном итоге скажется на надежности всей конструкции.
Как заправить проволоку
Процесс заправки сварочной проволоки – наиважнейший этап в подготовке к работе полуавтоматом, который требует внимательности и точности. Чтобы при сваривании не возникали перебои, следуйте рекомендациям, изложенным в инструкции по эксплуатации.
Мы же выделим основные моменты:
- Подключение горелки. Начните с подключения горелки к полуавтоматическому аппарату. Убедитесь, что соединение надежное, чтобы избежать сбоев в работе.
- Удаление компонентов. Снимите газовое сопло и контактный наконечник. Это нужно, чтобы правильно установить проволоку и минимизировать риск повреждения этих элементов.
- Установка катушки. Установите катушку сварочной проволоки на специальный кронштейн в корпусе аппарата. Закрепите ее с помощью резьбового соединения, чтобы она надежно удерживалась на месте и не раскручивалась во время работы.
- Настройка подающего ролика. Проверьте, чтобы канавки на подающем ролике соответствовали диаметру сварочной проволоки. Неправильный размер канавок может привести к заеданию проволоки и, как следствие, к неэффективной сварке.
- Заправка проволоки. Убедитесь, что заправка проволоки в подающий механизм происходит с минимальными перегибами и правильным прижатием. Эта информация, как правило, указана в инструкции или на механизме затяжки. Корректной заправкой избегают повреждения проволоки и настраивают надежную подачу.
- Бестоковая заправка. Активируйте кнопку бестоковой заправки, чтобы продвинуть проволоку через адаптер и вывести ее на горелку. Не используйте кнопку управления на горелке для протяжки проволоки, так как это может привести к неправильной подаче.
- Установка контактного наконечника и газового сопла. Закрепите контактный наконечник на горелке и установите газовое сопло на место. Убедитесь, что наконечник соответствует диаметру используемой проволоки: например, если диаметр проволоки составляет 0,8 мм, то отверстие в наконечнике должно быть также 0,8 мм.
Включите сварочный полуавтомат и проверьте работу механизма подачи. Убедитесь, что проволока подается равномерно и без заеданий. Если заедает, возможно, нужно отрегулировать натяжение роликов.
После успешной заправки проволоки и проверки подачи не забудьте установить защитный кожух на место.
Какой выбрать защитный газ
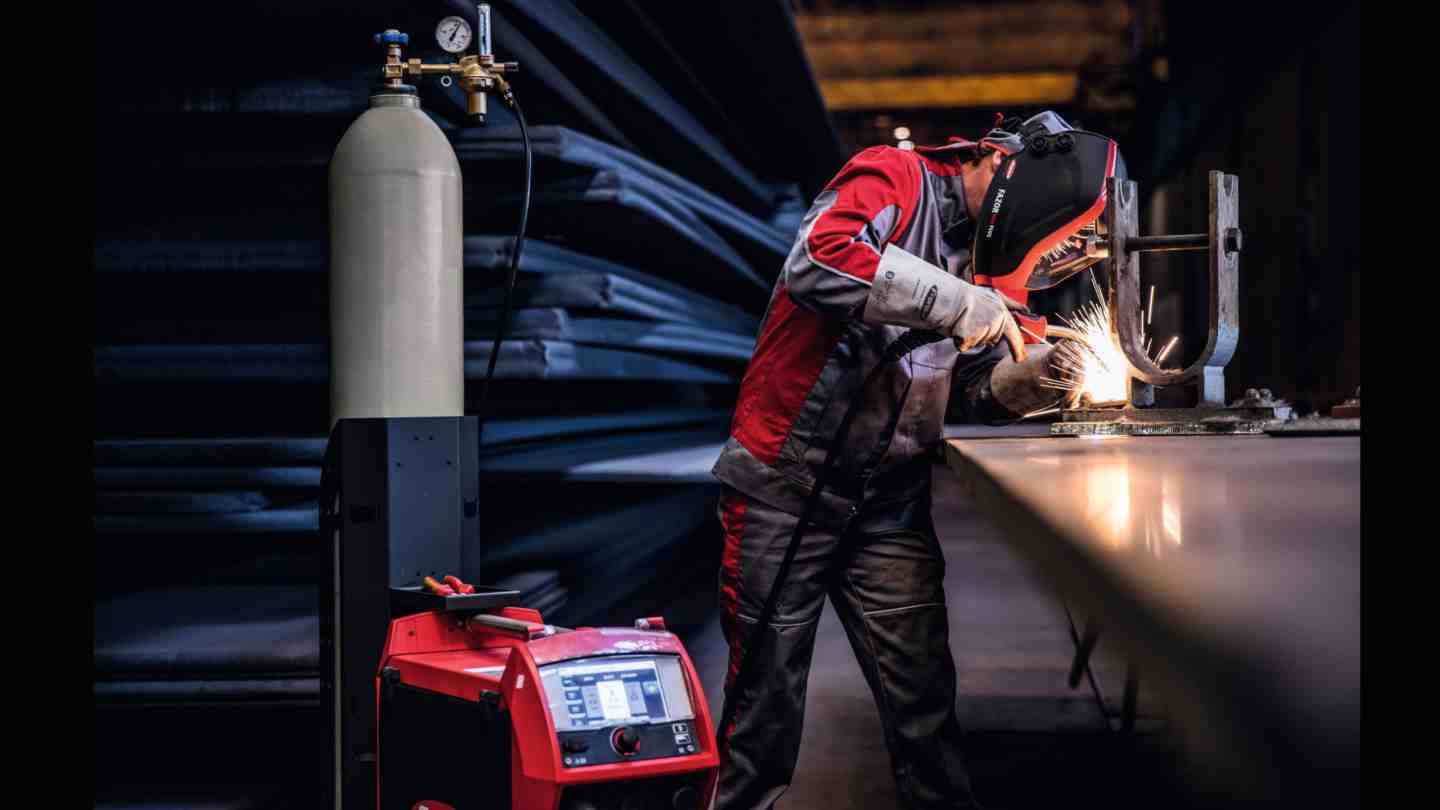
Составляющая полуавтоматической сварки – газ, инертный или активный. Первый (MIG сварка) не вступает в химические реакции с металлом. Пример – аргон.
Активные газы (MAG сварка) – способны взаимодействовать с металлом, улучшая некоторые характеристики сварного соединения. Например, углекислый газ и кислород.
Так что же выбрать?
Чистый углекислый газ – наиболее распространенный для сварки низкоуглеродистых и низколегированных сталей. Активизирует глубокое проплавление, что особенно полезно для сварки толстой стали. Прост в использовании для сварщиков разного уровня. При этом избыточное выделение тепла приводит к повышенному образованию брызг, что требует дополнительной обработки шва. Еще чистый углекислый газ создает более жесткую дугу, способен затруднять сварку тонколистовых материалов.
Аргон – инертный газ, который применяется для сварки цветных металлов (например, алюминия, меди, нержавеющей стали) и других материалов, чувствительных к окислению. Поддерживает стабильную и мягкую дугу, снижает образование брызг и повышает контролируемость процесса. Позволяет создать аккуратный, гладкий шов с минимальными дефектами, особенно на тонких материалах. В то же время сам по себе аргон не дает глубокого проплавления при сварке стали, так как не создает химической реакции, вырабатывающей дополнительное тепло. Высокая стоимость аргона может увеличить общие затраты на сваривание.
Другой вариант – смесь аргона и углекислого газа (Ar+CO₂). Один из самых универсальных для углеродистой и низкоуглеродистой стали. Соотношение газа варьируется: обычно используется смесь 80% аргона и 20% CO₂ – оптимальные условия качественного шва. Минимизирует брызги и способствует стабильной дуге. Гарантирует более глубокое проплавление по сравнению с чистым аргоном. Позволяет сварщику лучше контролировать форму и структуру шва.
Введение кислорода в смесь (до 5%) стабилизирует дугу и улучшает плавление металла. Эта комбинация подходит для сварки низкоуглеродистой и низколегированной стали.
Гелий иногда используется в сочетании с аргоном при сварке алюминия и меди. Высокая температура дуги, которую дает газ, помогает создать глубокий и прочный шов.
Углеродистая и низколегированная сталь – для этих материалов можно использовать чистый CO₂, если важна экономия и доступная очистка шва от брызг. Смесь Ar+CO₂ (например, 80% Ar и 20% CO₂) подходит для более аккуратного шва с минимальным количеством брызг.
Нержавеющая сталь – подойдет смесь Ar+CO₂+O₂. Например, 98% аргона и 2% кислорода. Как результат – отличное проплавление и прочный, устойчивый к коррозии шов.
Алюминий и медь – берем на вооружение чистый аргон или его смесь с гелием. Смесь аргона и гелия ведет к увеличению глубины проплавления, это актуально при работе с толстыми алюминиевыми изделиями.
Выбор газа для MIG/MAG сварки – это баланс между требованиями к качеству, стоимостью процесса и характеристиками сварочного оборудования. Для углеродистых сталей подходит как CO₂ (дешево и эффективно), так и смеси с аргоном, чтобы получить улучшенный шов. Нержавеющая сталь требует смеси с добавлением кислорода, а для сварки алюминия и меди лучше использовать аргон или смеси с гелием – здесь на первом месте стабильное горение дуги и глубокое проплавление.
Как варить полуавтоматом
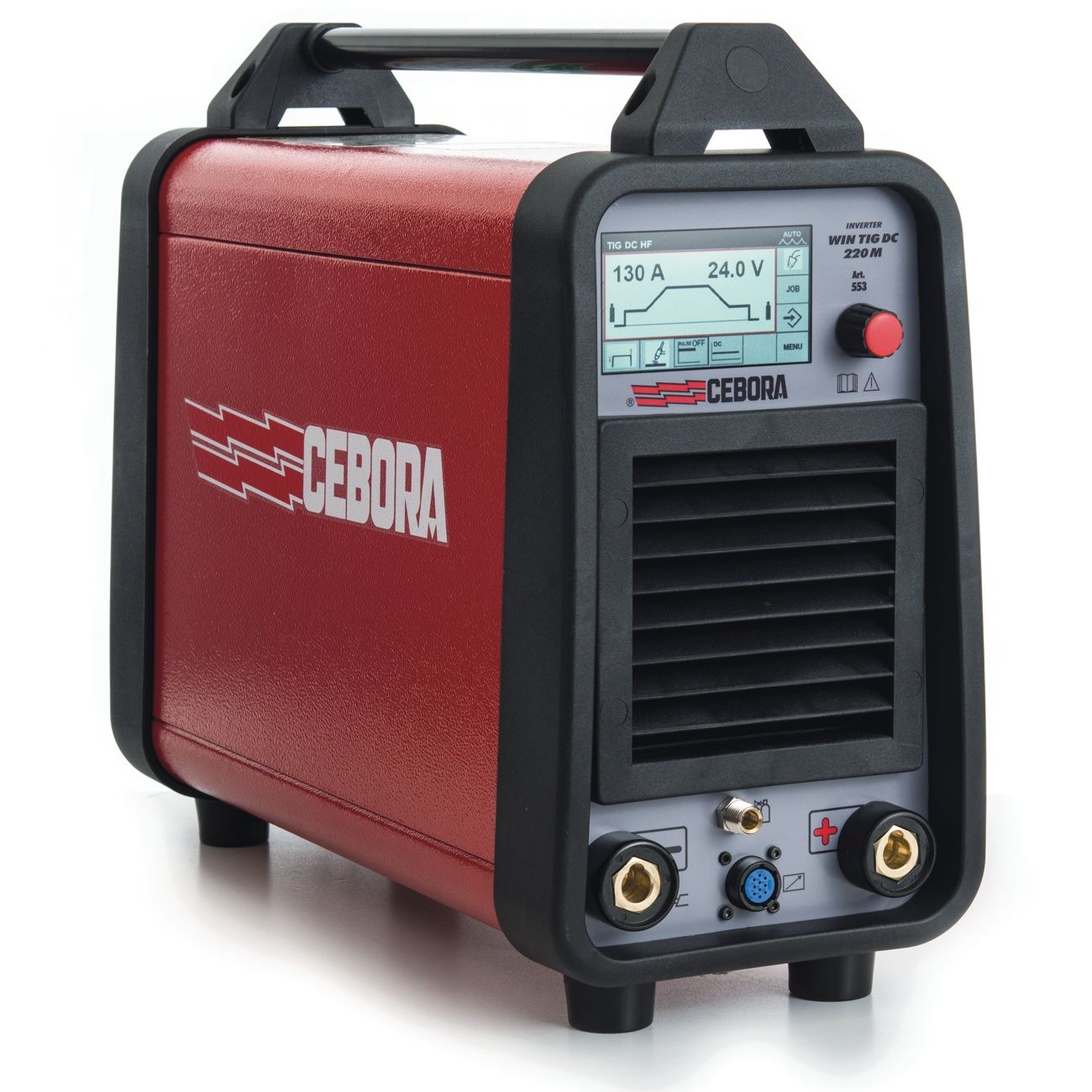
Для начала необходимо подготовить сварочный аппарат. Убедитесь, что все кабели подключены правильно: соедините кабель массы и кабель от горелки с аппаратурой. Затем установите редуктор на газовый баллон, обычно с углекислым газом или его смесью с аргоном, и поставьте катушку с проволокой. Проволока, которая служит электродом, должна подаваться свободно и плавно. После этого закрепите верхний прижимной ролик и проведите присадку через механизм протяжки. Теперь нужно установить токовый наконечник соответствующего диаметра, а затем и сопло, которые будут поддерживать правильную подачу газа и плавление проволоки.
Перед началом сварки подготовьте сами детали. Металлические поверхности обязательно очищают от краски, ржавчины, масла и любых других загрязнений. Это важно для того, чтобы шов получился прочным и долговечным, так как загрязнения могут вызвать поры и трещины. После этого разместите детали как можно ближе друг к другу, чтобы минимизировать зазор между ними. Закрепите с помощью зажимов или магнитных фиксаторов, чтобы заготовки не смещались во время сварки. Если деталь длинная, лучше зафиксировать ее по всей длине, чтобы избежать деформаций.
Ведение шва
Когда все готово, можно приступать непосредственно к сварке. Начинайте вести шов, перемещая горелку не по центру, а немного сбоку от линии шва, особенно при работе на краях деталей. Это поможет избежать прожогов, которые часто возникают при высокой температуре в пограничных зонах металла. Держите кончик электрода, то есть проволоку, на расстоянии примерно 6–10 мм от поверхности — так вы сможете контролировать процесс плавления и защитить зоны сварки газом. Направляйте электрод под углом 30–45 градусов к заготовке, чтобы тепло равномерно распределялось по металлу и снижался риск перегрева.
Ведите электрод по прямой линии, стараясь избегать остановок, так как равномерное движение – залог ровного и прочного шва. Остановки или задержки на одном месте могут привести к перегреву, прожогу или излишнему накоплению металла, снизят качество шва. Периодически следите за температурой металла: если участок перегревается, можно делать короткие паузы, чтобы дать ему остыть.
Если вы работаете с длинными заготовками, избегайте деформации деталей, предварительно сделав точечные прихватки. Сначала сделайте небольшие прихватки каждые 5–10 см, чтобы зафиксировать положение деталей, и только после этого заварите оставшееся пространство. Этот метод помогает избежать смещения заготовок и сохранить их форму.
Когда приближаетесь к завершению шва, важно постепенно снижать силу тока и уменьшать скорость подачи проволоки. Слишком резкое завершение может привести к образованию кратеров или пор, негативно отразится на прочности соединения. Постепенное снижение тока способствует более плавному переходу от зоны сварки к основе металла.
Замедление движения горелки
В конце шва рекомендуется плавно замедлить движение горелки. Это позволит избежать резкого обрыва дуги и улучшит качество окончания шва. Замедляя движение, вы дадите металлу возможность равномерно остыть и заполнить зону сварки без образования пустот и трещин.
Заполнение кратера
Когда дуга затухает, может образоваться углубление (кратер), которое часто становится слабым местом шва. Чтобы избежать этого, перед тем как полностью завершить сварку, сделайте несколько круговых или зигзагообразных движений в конце шва, постепенно убирая горелку. Чтобы плавно заполнить кратер расплавленным металлом и выровнять шов по всей его длине.
Постепенное отведение горелки
Отключив дугу, не убирайте горелку резко. Поднимите ее медленно, удерживая защитный газ над зоной сварки еще пару секунд. Это создаст защиту для шва от воздуха, предотвратив его окисление в горячем состоянии. Особенно важно придерживаться этого правила при работе с материалами, склонными к окислению, например, алюминием или нержавеющей сталью.
Охлаждение и обработка
После завершения дайте шву остыть естественным образом. Не охлаждайте его водой или воздухом, так как резкие перепады температуры могут вызвать деформацию и появление трещин. После полного остывания зачистите конец шва шлифовальным кругом или напильником, если требуется более эстетичное или гладкое соединение.
Контроль качества
В завершении проверьте качество окончания шва, он должен быть ровным и аккуратным, без трещин, кратеров и пор. В случае, если вы заметили дефекты, можно аккуратно подвести к этому участку горелку и слегка подварить зону. Делать это нужно с минимальным нагревом, чтобы не перегреть конец шва и избежать лишнего напряжения в металле.
Правильное завершение при полуавтоматической сварке – залог надежности и долговечности соединения. Уделяя внимание плавному снижению дуги, заполнению кратера и контролю качества, вы сможете добиться профессионального результата и избежать дефектов. Практика и внимание к деталям помогут выполнять швы, которые будут прочными и эстетически привлекательными!
Аргонодуговая
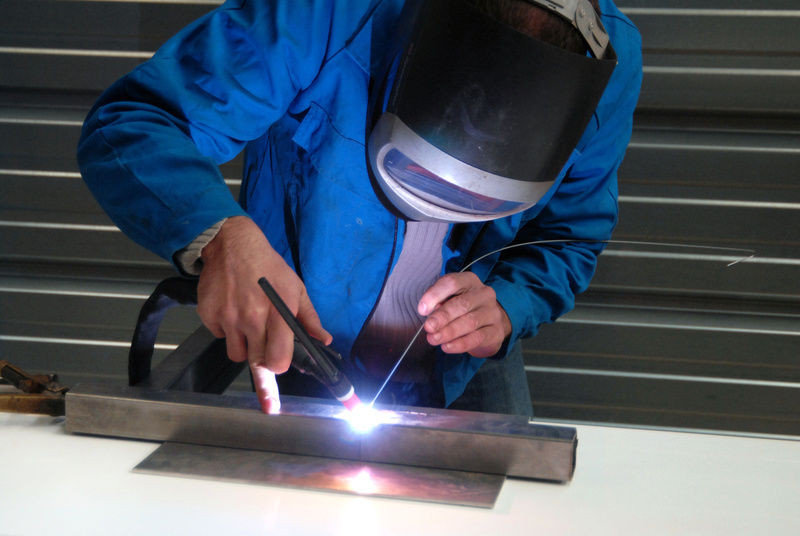
Один из самых точных и высококачественных методов сваривания, который широко используется в различных отраслях, от аэрокосмической и автомобилестроительной до производства ювелирных изделий. С помощью аргонодуговой (TIG-сварки) создают прочные и эстетически привлекательные швы, соединяя нержавеющую сталь, алюминий и магний, с минимальным количеством загрязнений. Выделяется своей точностью, возможностью работы с тонкими и легированными металлами, а также высокой степенью контроля процесса.
Для новичков TIG-метод довольно-таки сложный из-за необходимости подключения газа, использования неплавящегося электрода и навыков управления дугой. Однако, с пониманием основных принципов и правильным подходом, освоение этого метода становится вполне доступным и открывает широкие возможности для работы с различными материалами.
Суть метода
Аргонодуговая сварка заключается в использовании электрической дуги, образующейся между вольфрамовым электродом и свариваемым материалом. Главная особенность этого процесса – формирование шва неплавящимся электродом, а сварочную ванну и зоны плавления от воздействия внешней среды защищает инертный газ, чаще всего аргон. Именно его характеристики работают на стабильность дуги и высокое качество шва.
Сварка TIG получила свое название благодаря использованию вольфрамового электрода (Tungsten Inert Gas), где "Tungsten" – это вольфрам, а "Inert Gas" – инертный газ (чаще всего аргон или гелий), который предотвращает окисление металла и способствует чистоте сварного шва.
Процесс аргонодуговой сварки можно разделить на несколько основных этапов:
- Формирование дуги. Сначала сварщик устанавливает вольфрамовый электрод в горелку и включает сварочный аппарат. Когда горелка приближается к поверхности материала, создается электрическая дуга между электродом и металлом. В процессе дуга нагревает металл до температуры плавления.
- Подача инертного газа. Одновременно с дугой через горелку подается инертный газ (аргон или гелий), который образует защитный экран вокруг зоны плавления. Этот газ защищает сварочную ванну от воздействия кислорода и азота воздуха, предотвращая окисление металла и загрязнение шва.
- Плавление и соединение. Металл плавится в точке контакта с дугой, и сварщик, используя электрод, плавит заготовку. Таким образом формируется сварной шов. В случае необходимости добавляют проволоку, которая способствует образованию прочного соединения.
- Остывание и охлаждение. После окончания сварки шов постепенно остывает. При этом аргон продолжает поступать до полного завершения процесса, защищая уязвимое соединение от кислорода.
Основной принцип заключается в точечном нагреве свариваемых материалов и их соединении с помощью плавящегося металла, при этом важную роль играет использование инертного газа для защиты зоны сварки.
Оборудование
Сварочный источник питания – это центральный элемент оборудования аргонодуговой сварки, который подает необходимое напряжение и ток для формирования сварочной дуги. Источник питания должен давать стабильное напряжение, регулируемое питание, возбуждающее и поддерживающее электродугу с постоянным или переменным током, в зависимости от типа металла.
Постоянный ток (DC) используется для сварки черной, нержавеющей стали, чугуна.
Переменный – для алюминия и его сплавов, так как эффективно очищает материал от окислов благодаря чередованию полярности.
Современные сварочные инверторы, как правило, оснащены функцией регулировки тока и напряжения, дают возможность точно настроить параметры под конкретные задачи.
Не обойтись без рабочего инструмента сварщика – горелки. Фиксирует вольфрамовый электрод и подает на него ток, формирует сварочную дугу. Направляет в зону плавления защитный инертный газ. Также это компонент управления сварочным процессом – его началом и остановкой.
Обязателен еще баллон с инертным газом. Чтобы отрегулировать и стабилизировать подачу аргона, к баллону подключают редуктор. Регулятор расхода – контролирует поток аргона через горелку.
Для создания дуги используется вольфрамовый электрод, который не плавится в процессе сварки. Доступен различных типов:
- Чистый вольфрам (WT) – используется для сварки материалов, не требующих добавки других элементов.
- Торийсодержащие электроды (например, WT20) – вольфрам с добавлением тория улучшает стабильность дуги, повышает рабочие характеристики и увеличивает срок службы электрода.
- Лантаносодержащие – с добавлением лантана, такие электроды имеют хорошие характеристики стабильности дуги и могут использоваться при сварке различных материалов, в том числе алюминия и сплавов.
Когда необходимо добавить дополнительный металл в сварочную ванну, чтобы соединение было надежным, используют проволочную или порошковую присадку.
Проволока – из того же материала, что и основная заготовка или из материала, подходящего для сварки с ним. Обычно от 0,8 до 3 мм диаметром, в зависимости от толщины материала и типа сварного шва. Стальная, из нержавейки, алюминия, меди, титана и т.д. – подбирается в зависимости от сварочного материала. Подается вручную обычно в том месте, где уже образуется расплавленный металл, сварщик контролирует процесс.
Порошковая присадка используется реже. Представляет собой порошок из металла или легирующих элементов, который плавится в зоне действия электродуги и помогает создавать качественный шов. Обычно задействуется в ситуациях, где требуется специфическое изменение химического состава или улучшение механических свойств соединения.
Возвращаясь к оборудованию, не обойтись без кабель-шлангового пакета. Это кабель массы, подключения горелки к источнику тока, газовые шланги. Без кабель-шлангового пакета невозможна полноценная работа оборудования, так как он подает все необходимые ресурсы для сваривания.
Настройка
Перед началом сварки важно подготовить оборудование и материалы. Для этого нужно:
- Проверить состояние аппарата – убедиться, что все элементы – горелка, кабели, вентилятор охлаждения – находятся в исправном состоянии.
- Подготовить защитное оборудование: маску, перчатки, защитную одежду, а также систему вентиляции.
Далее – настройка источника тока.
Основной параметр при настройке аппарата аргонодуговой сварки – это правильный выбор тока. Это зависит от типа и толщины материала, а также от диаметра электрода.
Для сварки сталей и большинства сплавов используется постоянный ток (DC), а для алюминия или магниевых сплавов – переменный (AC).
Для большинства металлов сила тока рассчитывается по таблицам или может быть вычислена по формуле: для постоянного тока – 1 ампер на 0,1 мм толщины материала, для переменного – на 0,2 мм.
Регулировка тока выполняется через панель управления на аппарате, где есть возможность настройки в амперах. Для тонких материалов (например, до 1 мм) выбирается меньший ток, для более толстых – больший.
Что касается диаметра тугоплавкого электрода, зависит от толщины свариваемого материала.
Тонкие материалы (до 2 мм) – используют электроды диаметром 1,6-2,4 мм.
Для более массивных изделий (толщиной от 2 до 6 мм) – электроды диаметром 3,2 мм.
Помимо диаметра смотрят на цвет стержня.
Зеленый электрод (маркировка WP) представляет собой чистый вольфрам, который используется преимущественно для сварки алюминия, магния и их сплавов. Предназначен для работы с переменным током (AC). Чистый вольфрам дает стабильность дуги и хорошую защиту от окисления, что особенно важно при работе с металлами, склонными к образованию оксидных пленок.
Серый электрод (WC) – универсальный и подходит как для работы на постоянном, так и на переменном токе. Применяется для соединения различных материалов, включая углеродистую и нержавеющую сталь, бронзу и другие сплавы.
Красный (WT) – содержит диоксид тория, что придает стержню повышенную стойкость и улучшенные характеристики при высоких температурах. Эти электроды идеально подходят для сварки стали, нержавеющей стали и цветных металлов. Они обеспечивают высокую стабильность дуги, хорошо себя показывают на постоянном токе. Предотвращают образование дефектов на шве и повышают долговечность сварного соединения.
Темно-синий электрод (WY) предназначен для сварки титана, меди и легированных сталей. Эффективен на постоянном и переменном токе.
Белый (WZ) покрыт оксидом циркония, что делает его идеальным для сварки с переменным током. Эти электроды подходят для работы с медью и алюминием, улучшая стабильность дуги и предотвращая ее разрушение, что важно при сварке материалов, склонных к окислению.
Синие и золотистые (WL) содержат лантан, который значительно улучшает стабильность дуги и ее стойкость к разрушению. Эти электроды подходят для сварки как на постоянном, так и на переменном токе. Лантановые электроды идеально подходят для работы с такими материалами, как алюминий, медь и нержавеющая сталь, обеспечивая высокое качество и точность сварки.
Теперь о защитной среде.
Аргон является основным газом, используемым для защиты сварочной дуги. Газ подается через горелку и должен быть чистым, без примесей влаги и кислорода. На аппарате аргонодуговой сварки настраивают расход аргона в литрах в минуту. Оптимальная величина зависит от диаметра горелки и силы тока, но обычно составляет от 6 до 15 литров в минуту.
Важно, чтобы расход газа был стабильным на протяжении всей сварки, так как это влияет на качество шва и безопасность работы. Избыточное количество газа может привести к повышенному расходу, а недостаток – к слабой защите дуги.
Горелка для аргонодуговой сварки играет ключевую роль, обеспечивая не только подачу газа, но и удобство работы. Важно установить ее под правильным углом и в правильном положении относительно заготовки.
Угол наклона – должен быть в пределах 10-15° по отношению к поверхности сварки, а также направлен в сторону подаваемого материала.
Расстояние от горелки до материала – должно быть минимальным, но не настолько, чтобы дуга касалась металла. Обычно это расстояние составляет около 3-5 мм.
Правильный режим дуги также имеет большое значение. Есть несколько способов контроля:
Сварка с предварительным поджигом – в этом случае дуга зажигается в момент включения сварки, без необходимости дополнительного контакта электрода с поверхностью.
Сварка с мягким стартом – начало процесса с пониженной мощностью, помогает избежать образования дефектов на начальной стадии сварки.
Регулировка времени газа (пред- и постгаз) – настройка параметров сварочного процесса, которые определяют время подачи защитного газа перед и после сварки. Предгаз используется для создания среды инертного газа перед сваркой, чтобы исключить попадание воздуха в зону. Постгаз – защита газом во время угасания дуги, предотвращает окисление поверхности шва.
Правильная настройка аппарата аргонодуговой сварки – залог успешного выполнения сварочных работ с высоким качеством. Каждая деталь, от выбора тока до настройки горелки и газа, влияет на конечный результат. Важно следить за параметрами, проводить регулярное обслуживание оборудования и работать в соответствии с инструкциями, чтобы процесс был безопасным, а его результаты – отличные!
Ведение шва
Перед началом сварки важно тщательно подготовить материал. Металл необходимо очистить от ржавчины, масла, пыли и других загрязнений, которые могут повлиять на качество шва. Наиболее подходящими инструментами здесь выступают металлическая щетка и обезжириватели. Для алюминия требуется дополнительная подготовка – удаление окисной пленки, что можно сделать с помощью ацетона или специального очистителя.
Обычно используют вольфрамовые электроды, которые подбирают в зависимости от типа и толщины металла. Для работы с тонкими металлами предпочтительно использовать электроды малого диаметра (1–2 мм), а для более толстых – более крупные (3 мм и больше).
Ток и напряжение также настраиваются с учетом характеристик металла. Например, для алюминия требуется переменный ток (AC), а для большинства других металлов используется постоянный (DC). Правильная настройка параметров сварки поможет добиться стабильной дуги и качественного шва.
Для ведения шва очень важно правильно расположить электрод. Стандартный угол наклона около 15–20 градусов относительно поверхности металла. Это поможет стабилизировать дугу и избежать излишнего нагрева металла.
Электрод должен быть расположен максимально близко к материалу, но при этом не касаться его, иначе дуга будет нестабильной. Важно также соблюдать равномерную дистанцию и угол, чтобы шов был однородным.
Техника ведения шва зависит от типа соединения и материала. Есть несколько основных методов ведения, каждый из которых имеет свои особенности.
Самая простая техника – это прямолинейный шов. Она используется для соединения прямых участков. В данном случае электрод ведется вдоль линии шва ровным и медленным движением. Не задерживаться на одном месте, чтобы избежать перегрева и деформации металла.
Круговые движения (спиралевидный шов) – эта техника подходит для более сложных соединений и обеспечивает лучшее проплавление. Круговыми движениями равномерно распределяют тепло и избегают пор. Ведут электрод по небольшим кругам, чтобы избежать деформации и перегрева.
При работе с тонкими металлами или в сложных местах, где возможна деформация, часто используют точечную сварку. Осуществляется серией точек, позволяет минимизировать воздействие тепла. После каждого прохождения дают металлу остыть, а затем переходят к следующей точке.
Скорость ведения шва – ключевой фактор в аргонодуговой сварке. Слишком высокая скорость может привести к недостаточному проплавлению, а низкая – к перегреву металла и образованию дефектов. Оптимальная скорость зависит от толщины металла и параметров сварочного аппарата. При этом важно контролировать температуру – в случае перегрева дайте металлу остыть.
Для предотвращения перегрева можно периодически останавливать сварку и задействовать воздушное охлаждение, если это возможно для используемого материала.
Присадочную проволоку подают под углом примерно 15–20 градусов к месту сварки, но так, чтобы она находилась в зоне дуги и хорошо проплавлялась. Важно не перекрывать дугу проволокой, чтобы не затруднять подачу аргона и не провоцировать дефекты шва.
Скорость подачи проволоки также играет значимую роль: слишком быстрая подача приведет к образованию комков, а слишком медленная – к недостаточному наполнению шва.
Аргонодуговая сварка – это сложный, но эффективный процесс, требующий точности и аккуратности. Ключевыми моментами, обеспечивающими качественный результат, являются правильный выбор и подготовка материала, правильное положение и ведение электрода, соблюдение скорости и температуры, а также подача присадочной проволоки. С опытом и соблюдением этих правил можно достичь ровного и прочного шва, который будет служить долгие годы.
Какие ошибки часто допускают новички
Аргонодуговая сварка (TIG) привлекает многих начинающих сварщиков своей универсальностью и возможностью создания качественных, прочных швов на различных металлах. Однако эта технология требует особых навыков, и на начальном этапе обучения новички часто допускают ряд ошибок, которые значительно ухудшают результат.
Многие новички недостаточно готовят металл перед началом сварки, оставляя на нем грязь, ржавчину, масло или оксидную пленку. Эти загрязнения препятствуют качественному соединению, приводят к образованию пор, трещин и других дефектов.
Металл необходимо тщательно очистить перед сваркой. Для этого можно использовать металлическую щетку, ацетон или специальные очистители для удаления окислов и загрязнений. Особенно важно удалять оксидную пленку при сварке алюминия, так как она ухудшает качество шва.
Использование неподходящего электрода – распространенная ошибка. Новички часто не понимают, какой диаметр и тип электрода лучше подойдет для конкретного материала и толщины металла. В результате сварка может быть нестабильной или шов получится некачественным.
Электроды для аргонодуговой сварки чаще всего делают из вольфрама, но их диаметр и тип зависят от материала и задачи. Например, для алюминия обычно используют электроды с добавлением оксида тория или циркония и переменный ток (AC). Для стали подойдут стержни с оксидом лантана или церия, работающие на постоянном токе (DC).
Один из самых важных аспектов аргонодуговой сварки – это правильный угол наклона электрода. Новички часто либо держат электрод под прямым углом к металлу, либо наклоняют его слишком сильно, что нарушает защиту аргона и делает дугу нестабильной.
Оптимальный угол наклона электрода составляет около 15–20 градусов к поверхности металла. При таком угле дуга будет стабильной, а шов – ровным и прочным. Если угол будет слишком большим, дуга будет нестабильной, в результате неравномерный нагрев и дефекты.
Неправильно подобранные настройки сварочного аппарата – сила тока, напряжение и скорость подачи аргона – приводят к перегреву, недостаточному проплавлению или образованию брызг.
Начинающим сварщикам следует заранее ознакомиться с рекомендациями по настройке источника для разных типов металлов. Сила тока подбирается в зависимости от толщины металла и диаметра электрода. При работе с тонкими листами требуется низкий ток, а для толстых деталей – более высокий. Поток аргона обычно настраивают в пределах 6–15 литров в минуту в зависимости от диаметра электрода и условий работы.
Новички могут не контролировать постоянную подачу аргона, особенно если держат рукоятку неправильно. В результате сварочная зона теряет защиту от воздуха, что приводит к окислению и образованию пор в шве.
Следите за тем, чтобы поток аргона был стабильным и покрывал зону сварки. Если вы чувствуете, что газовая защита недостаточна, проверьте настройки подачи аргона и герметичность оборудования. Сварочная горелка должна находиться на достаточном расстоянии от материала, чтобы поток аргона распространялся равномерно и защищал металл от контакта с воздухом.
Многие новички неправильно вводят присадочную проволоку, что мешает стабильности дуги и ухудшает качество шва. Они либо вводят ее слишком быстро, либо слишком медленно. Тогда нарушается проплавление, не избежать дефектов.
Присадочная проволока должна подаваться плавно и равномерно, чтобы шов был качественным. Вводите ее под углом около 15–20 градусов, поддерживая плавное движение. Важно также не перекрывать дугу проволокой, чтобы аргон мог свободно циркулировать в зоне сварки.
Некоторые новички ведут шов слишком быстро или медленно. Если шов ведется слишком быстро, металл не успевает прогреваться и проплавляться, и соединение будет ненадежным. При слишком медленной сварке металл перегревается и деформируется.
Поддерживайте равномерную скорость, ориентируясь на размер и тип соединяемых деталей. Обычно рекомендуется вести шов ровными движениями, без остановок, чтобы получился равномерным. Со временем у вас появится чувство оптимальной скорости, которая даст качественное проплавление без перегрева.
Еще часто не учитывают важность контроля температуры металла. Перегрев может вызвать деформацию, окисление и нежелательное воздействие на свойства металла.
Старайтесь поддерживать температуру металла на оптимальном уровне. Если заметили, что металл начал перегреваться, можно сделать паузу, чтобы он успел остыть. Для более толстых деталей можно использовать воздушное охлаждение, но делать это аккуратно, чтобы не вызвать трещин.
Неопытные сварщики часто не уделяют должного внимания технике безопасности, пренебрегая средствами защиты или работая в непроветриваемом помещении. Это может привести к ожогам, повреждению глаз и отравлению продуктами сгорания.
Обязательно используйте защитные очки, перчатки и специальную маску для сварки, которые защитят вас от ультрафиолетового излучения и брызг. Работайте в хорошо проветриваемом помещении или с вытяжкой, чтобы предотвратить вдыхание вредных газов.
Освоение аргонодуговой сварки требует времени и внимания к деталям, и на начальном этапе неудачи неизбежны. Однако, понимая и избегая распространенных ошибок, вы сможете повысить качество своей работы, обеспечить безопасность, быстрее научиться создавать ровные и прочные соединения.
Полезные советы для начинающих
Аргонодуговая, или TIG-сварка (от английского Tungsten Inert Gas), привлекает сварщиков возможностью работать с разными металлами, включая алюминий, нержавеющую сталь, медь и их сплавы, и получать качественные, чистые швы. Однако, несмотря на преимущества, освоение данного метода требует терпения, практики и соблюдения технических нюансов.
Выберите подходящее оборудование и расходные материалы.
Для аргонодуговой сварки используют вольфрамовые электроды. Их тип зависит от металла и типа тока. Например:
- Для нержавеющей стали используйте электроды с добавками оксидов лантана, церия или тория, которые обеспечивают стабильную дугу на постоянном токе (DC).
- Для алюминия выбирают электроды с добавками циркония или чистый вольфрам, так как сварка алюминия проводится на переменном токе (AC).
Присадочная проволока должна соответствовать материалу заготовок. Для сварки нержавеющей стали выбирают присадку с аналогичным химическим составом, а для алюминия используют специальные алюминиевые присадочные сплавы. Не используйте дешевую или некачественную проволоку, так как это может привести к образованию дефектов в шве.
Аргон – это инертный газ, который защищает сварочную зону от окисления и загрязнений. Для TIG-сварки рекомендуется использовать аргон высокой чистоты (99,9% и выше). Оптимальный расход аргона составляет 6–15 литров в минуту в зависимости от диаметра электрода и условий работы.
Подготовьте металл перед сваркой! Металлические поверхности должны быть чистыми. Наличие загрязнений, окислов или масляных пятен приводит к образованию пор, трещин и других дефектов. Для очистки используют металлические щетки, ацетон или специальные очистители.
Особое внимание уделите алюминию – на его поверхности быстро образуется окисная пленка, которую нужно удалять перед сваркой.
Установите правильные параметры!
Подбор силы тока зависит от толщины металла и диаметра электрода. Для тонких металлов выбирают низкий ток, а для более толстых – более высокий. Например, для тонкой нержавеющей стали достаточно тока 50–70 ампер, а для толстого алюминия – до 200 ампер.
Для алюминия обычно выбирают переменный ток (AC), а для большинства других металлов – постоянный ток (DC). Соблюдение этих параметров важно для создания стабильной дуги и равномерного шва.
Оптимальный поток аргона зависит от диаметра электрода и условий работы. Если поток слишком низкий, зона сварки может окислиться; если слишком высокий – дуга станет нестабильной, и металл будет недостаточно защищен. Настраивайте расход газа так, чтобы поток равномерно защищал сварочную зону, особенно при работе на открытом воздухе.
Электрод должен быть наклонен под углом 15–20 градусов относительно поверхности металла. Это даст стабильность дуги и поможет предотвратить перегрев. При наклоне под таким углом дуга остается стабильной, улучшает качество шва.
Присадочная проволока также должна подаваться под углом к металлу – обычно 15–20 градусов. Важно, чтобы проволока находилась в зоне дуги, но не перекрывала ее, иначе аргон не будет защищать металл от кислорода.
Практикуйте технику ведения шва!
Правильная техника ведения – один из ключевых факторов для получения качественного результата. Начинающим рекомендуется начинать с прямолинейного движения вдоль линии шва, поддерживая стабильный угол наклона и расстояние до поверхности.
Основные методы ведения шва:
- Линейное движение – подходит для прямых швов, обеспечивает равномерное проплавление.
- Круговые – подходит для толстых металлов, помогает равномерно распределить тепло и получить качественное проплавление.
- Точечная сварка – используется для тонких металлов, снижает риск деформации и перегрева.
Начните с линейного движения, постепенно осваивая более сложные техники.
Контролируйте скорость и температуру.
Скорость ведения шва оказывает существенное влияние на качество соединения. Если шов ведется слишком быстро, металл не успеет расплавиться, это приведет к плохому проплавлению и низкой прочности. Если слишком медленно – перегреется, и шов получится неровным, с дефектами и окислами.
Обратите внимание на температуру заготовки – при перегреве делайте паузы, чтобы металл успел остыть. Особенно это важно при сварке тонких деталей, которые склонны к деформации от перегрева.
Работайте в удобной позе и не торопитесь!
Для качественной сварки важно поддерживать стабильность и уверенность движений. Удобное положение поможет избежать случайных ошибок и обеспечит точность работы. Начинающим рекомендуется заранее продумать и занять удобную позу, которая позволит легко контролировать движения рук.
Также не стоит торопиться. Осваивайте процесс постепенно, начиная с более простых швов, чтобы наработать практические навыки.
Соблюдайте технику безопасности!
Аргонодуговая сварка выделяет сильное ультрафиолетовое излучение. Чтобы защититься от ожогов и раздражения глаз, надевайте сварочную маску, защищающие перчатки и плотную одежду с длинными рукавами. Работайте в хорошо проветриваемом помещении или используйте вытяжку, так как сварочные пары крайне вредны для здоровья.
Заключение
Сварка – это сложный и многогранный процесс, требующий не только навыков, но и понимания основ физических и химических процессов, которые происходят при взаимодействии металлов под воздействием высоких температур. Для новичка, решившего освоить сварочное дело, важно осознать, что это не просто соединение металлов, но и искусство, в котором каждый элемент процесса влияет на конечный результат.
Прежде всего, ключевым элементом безопасной работы является соблюдение техники безопасности, ведь сварка сопряжена с рисками – высокая температура, ультрафиолетовое излучение, искры и разлетающиеся капли расплавленного металла. Только используя соответствующую защитную экипировку и следуя правилам, можно обезопасить себя и окружающих.
Для начинающих сварщиков полезно начать с освоения ручной дуговой сварки, так как этот метод один из самых доступных и понятных. Полуавтоматическая сварка, в свою очередь, подходит для тех, кто хочет работать с более тонкими металлами или стремится повысить скорость и точность сварочных работ. Важно также понимать, что выбор защитного газа при полуавтоматической сварке существенно влияет на качество шва и устойчивость дуги. Подобрав правильный газ для нужного типа металла и задачи, сварщик может добиться оптимальных результатов.
Аргонодуговая сварка – более сложный метод, который требует дополнительной подготовки и навыков, но предоставляет возможность создавать высококачественные швы на таких материалах, как алюминий и нержавеющая сталь. Освоение этого метода откроет для новичка доступ к более сложным и специализированным работам.
Каждый из методов имеет свои особенности, и понимание их помогает сделать правильный выбор в зависимости от задачи. Осваивая сварочные процессы, новички также начинают понимать важность правильной подготовки поверхностей, регулировки силы тока и скорости подачи проволоки или электрода.
Сварка – это навык, который можно развивать и совершенствовать бесконечно. Начав с основ, любой новичок со временем может стать опытным мастером, создавая надежные и эстетически привлекательные соединения. Пусть этот путь будет для вас источником новых знаний, опыта и профессионального роста!