Сварка электродами для новичков
Содержание статьи:
Сварка электродами – популярный и доступный метод соединения металлов. Этот процесс, хоть и требует определенных навыков и знаний, остается привлекательным даже для начинающих. Использование классической РДС в домашних условиях или для мелких ремонтных работ позволяет прочное соединять металлы без применения тяжелого и дорогостоящего оборудования.
Несмотря на кажущуюся простоту, сварка требует аккуратности в выборе материалов, правильной настройки оборудования и соблюдения техники безопасности. Качество работы зависит в том числе от умения контролировать процесс: от держания электрода до регулировки сварочного тока. Даже несложные на первый взгляд операции могут привести к дефектам, если не учитывать нюансы.
Значение электродов в сварочном процессе
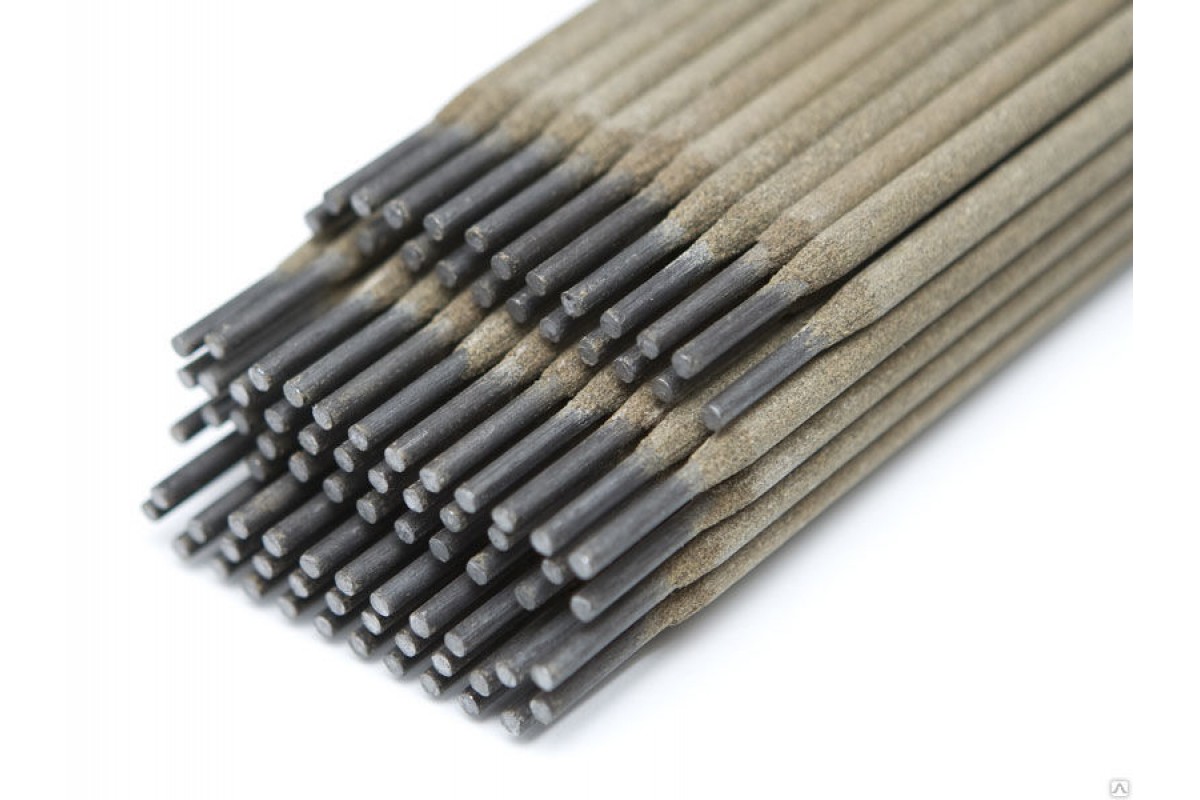
Ручная дуговая сварка (РДС) – один из самых популярных и востребованных методов соединения металлов, использующий плавящиеся электроды. Именно благодаря электродам этот процесс отличается высокой эффективностью и универсальностью, позволяя сваривать как тонкие, так и массивные металлоконструкции. Электроды в процессе РДС играют ключевую роль, оказывая влияние на качество сварного шва, удобство работы и долговечность соединения.
Что такое электроды для РДС?
Электрод – главный расходный материал ручной луговой сварки, металлический стержень, покрытый специальным защитным слоем (обмазкой). Во время сварочного процесса он не только создает дугу для расплавления металлов, но и сам плавится, формируя шов и обеспечивая его защиту от окисления и других внешних воздействий. Покрытие электрода оказывает важное влияние на процесс сварки: защищает зону плавления от окружающей атмосферы, стабилизирует дугу и улучшает механические характеристики шва.
Состав
Основной материал электрода – это металл, который в процессе сварки плавится и добавляется в шов. Чаще всего для стержня используют углеродистые стали или легированные сплавы, в зависимости от требуемых характеристик шва (например, его прочности и коррозионной стойкости). Важно, чтобы металл стержня обладал хорошей электропроводностью и стабильностью при высоких температурах, возникающих в процессе сваривания.
Покрытие, или обмазка, – это слой материала, который наносится на стержень электрода и играет важную роль в процессе сварки. Оно защищает сварочную ванну от воздействия воздуха, способствует стабилизации дуги, улучшает плавление и удаляет шлак из зоны сварки. Состав покрытия может значительно различаться в зависимости от типа электрода. Основные компоненты покрытия включают:
ul>Состав электрода напрямую влияет на его характеристики и поведение в процессе сварки. Например, рутиловые стержни интересны легким зажиганием и стабильным горением дуги, удобны для сварки в любых положениях. Электроды с основным покрытием образуют шов, более устойчивый к внешним воздействиям, и лучше подходят для сварки ответственных конструкций. Тип покрытия определяет свойства шва – его прочность, стойкость к коррозии, а также внешний вид. Важно правильно выбрать электрод в зависимости от материала свариваемой детали и условий эксплуатации.
Функции электродов
Конечно, это создание дуги. Электроды формируют электрическую дугу, которая образуется между их концом и поверхностью металла. Под действием высокой температуры металл и электрод расплавляются, создавая сварное соединение.
Помимо электродуги стоит отметить и такие функции:
- Формирование сварного шва. При плавлении электрод образует сварочную ванну – расплавленный металл, который, затвердевая, создает сварной шов. От качества материала и покрытия электрода зависит прочность и надежность соединения.
- Защита зоны сварки. Покрытие электрода при его плавлении выделяет газы, которые образуют защитное облако вокруг сварочной ванны. Это предотвращает попадание кислорода и азота из воздуха, снижает вероятность образования пор, трещин и других дефектов в шве.
- Стабилизация дуги. Различные компоненты покрытия работают на стабильное горение дуги, уменьшают разбрызгивание и улучшают качество шва. Особенно ценны при сварке сложных конструкций, где требуется высокий уровень контроля.
- Формирование шлака. При плавлении покрытия образуется шлак, который всплывает на поверхность сварочной ванны. Шлак защищает металл во время его кристаллизации, предотвращая нежелательные химические реакции. После остывания он легко удаляется, оставляя гладкий и ровный шов.
Неотъемлемый элемент РДС – электроды. Они не только обеспечивают стабильную работу дуги и защиту сварного шва, но и существенно влияют на свойства самого соединения, от которых зависят надежность, прочность и долговечность конструкции!
Виды и марки электродов РДС
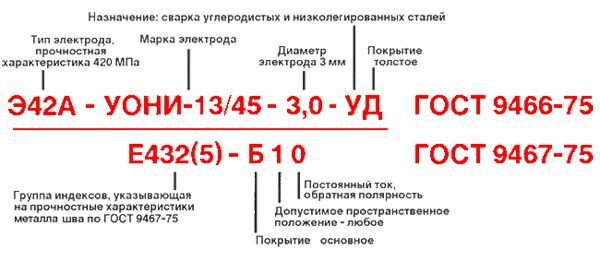
Ручная дуговая сварка – востребованный метод соединения металлов, применяемый как в промышленных масштабах, так и в частных мастерских. Благодаря своей универсальности и сравнительно низкой стоимости оборудования РДС позволяет выполнять широкий спектр сварочных задач, от ремонта металлоконструкций до сложных монтажных работ. Основой процесса выступают сварочные электроды – расходные материалы, которые проводят ток к свариваемому металлу и участвуют в формировании прочного, долговечного шва.
Электроды отличаются по химическому составу, характеристикам покрытия, диаметру, конструктивным особенностям и не только. Параметры изделий влияют на важные аспекты процесса сварки – стабильность дуги, глубина проплавления, форма шва и защита расплавленного металла от окисления. Выбрать подходящий расходник – значит добиться оптимальных характеристик шва для конкретного типа металла и условий работы. Но для этого нужно разбираться в разновидностях данных компонентов сварки.
Обмазка
Покрытие, или обмазка электрода, представляет собой комбинацию различных порошкообразных веществ, которые наносятся на стальной сердечник стержня. Играет ключевую роль в процессе сварки, так как защищает сварочную ванну от попадания вредных примесей, а также регулирует характеристики дуги и способствует улучшению качества шва. В зависимости от состава и назначения, покрытия выполняют дополнительные функции, от защиты от окисления до повышения прочности сварного соединения.
Отметим четыре основных типа покрытий:
- Рутиловое (Р) – состоит в основном из диоксида титана (рутил), придает электроду особые характеристики. Обладает высокой стабильностью дуги, позволяет выполнять сварку как постоянным, так и переменным током. Способствует созданию качественного шва с минимальным количеством брызг и шлаков. Легко очищается после завершения работы. Оно подходит для сварки углеродистых и низколегированных сталей, но не является идеальным для работы с материалами, требующими высокой прочности соединений.
- Основное (Б) – применяется для сварки особо ответственных конструкций, включая нержавеющие стали, легированные и жаропрочные металлы. Отличается способностью образовывать защитную газовую оболочку, помогает предотвратить окисление металла при высоких температурах. Эффективно устраняет шлаки и снижает их количество на поверхности шва. Электроды с основным покрытием подходят для сварки в неблагоприятных условиях, например, высокая влажность или низкие температуры. Чаще всего используются в ответственных конструкциях, требующих высоких эксплуатационных характеристик, например, в судостроении, нефтехимической отрасли и в энергетике.
- Кислое покрытие (А) – в основном состоит из кислых флюсов – кремнезем и железистые компоненты. Идеально подходит для сварки низкоуглеродистых сталей, а также для восстановления различных металлоконструкций, подвергшихся коррозии. Благодаря своей способности растворять оксиды на поверхности металла улучшает качество сварного соединения. Однако кислая обмазка требует более тщательной подготовки металла, так как может оставлять следы, которые сложнее удалить, чем шлак от других типов покрытия. Также важно соблюдать строгие температурные режимы, чтобы избежать образования пор и трещин в шве.
- Целлюлозное покрытие (Ц) – интересно высоким содержанием органических веществ, целлюлозы, образует защитный газообразный слой в процессе сваривания. Обладает уникальной способностью работать в трудных условиях – низкие температуры, высокая влажность и сварка в труднодоступных местах. Эффективно использует низкое содержание водяных паров в воздухе для защиты сварочного шва от загрязнений и окисления. Целлюлозные электроды поддерживают хорошую дугу и создают минимум брызг. Широко применяются в строительстве и ремонте трубопроводов, а также в других отраслях, где важна высокая производительность и стойкость к внешним воздействиям.
Каждое из покрытий выполняет свои задачи в зависимости от условий сварки и свойств материалов. От правильного выбора в данном случае зависит не только качество сварного шва, но и долговечность соединения, а также безопасность выполнения работ.
Для какого материала – буквенное обозначение
Сварочные электроды маркируются буквенными обозначениями, которые указывают на их предназначение и свойства в зависимости от типа металла и условий эксплуатации. Буква помогает сварщикам выбрать оптимальный расходный стержень, учитывая механические свойства, термостойкость, коррозионную устойчивость и другие характеристики материалов. Вот основные типы электродов и их особенности:
- «У» – для углеродистых и низкоуглеродистых сталей. Эти электроды разработаны для работы с металлами, предел прочности которых при растяжении не превышает 600 МПа. Они обеспечивают хорошее качество шва при работе с углеродистыми сталями, применяемыми в строительстве и машиностроении, где нет необходимости в повышенных требованиях к прочности и устойчивости к высоким температурам или коррозии.
- «Л» – конструкционные и легированные стали. Электроды этой категории подходят для работы с металлами, также имеющими предел прочности на разрыв до 600 МПа, но с добавлением легирующих элементов. Легированные стали обладают улучшенными характеристиками по сравнению с углеродистыми аналогами, например, большей износостойкостью и ударной вязкостью, что делает электроды «Л» востребованными при создании конструкций с повышенными механическими требованиями.
- «Т» – термостойкие легированные стали. Эти электроды предназначены для сварки металлов, которые подвергаются высоким температурам в процессе эксплуатации, как в энергетическом оборудовании или в химической промышленности. Легирующие элементы в таких сталях повышают их термостойкость, сопротивление окислению и жаропрочность, что требует соответствующего состава электродного покрытия для создания надежных швов, устойчивых к температурным деформациям.
- «В» – для высоколегированных сталей. Высоколегированные стали содержат значительное количество хрома, никеля, молибдена и других элементов, что наделяет их особыми свойствами — коррозионной стойкостью, жаропрочностью или прочностью при экстремальных нагрузках. Электроды с маркировкой «В» специально разработаны для сварки таких материалов, позволяя получить швы с высокой устойчивостью к агрессивной среде и воздействию высокой температуры.
- «Н» – для наплавки. Наплавочные электроды используются для нанесения защитного или восстанавливающего покрытия на поверхность деталей. Такие электроды позволяют упрочнить изношенные поверхности, улучшить их износостойкость, стойкость к коррозии или восстановить исходные размеры деталей. Наплавка востребована в ремонтных и восстановительных работах, а также при производстве деталей, нуждающихся в повышенной износостойкости, например, для горнодобывающей или металлургической отраслей.
В зависимости от назначения, сварочные электроды делятся на плавящиеся и неплавящиеся. Плавящиеся расплавляются под действием дуги, добавляя металл в сварной шов, в то время как неплавящиеся, из вольфрама, не изменяют свою форму и используются для создания дуги при сварке инертным газом. Электроды для наплавки представляют собой отдельную категорию, так как их основная задача – формирование защитного слоя на поверхности, а не соединение деталей.
Толщина покрытия
Электроды классифицируются по толщине покрытия, которая оказывает значительное влияние на процесс сварки, защиту шва и качество соединения. В зависимости от этого параметра выделяют четыре основные группы, каждая из которых маркируется определенной буквой и предназначена для выполнения специфических задач:
- «М» – тонкое покрытие. Электроды с маркировкой «М» имеют минимальную толщину покрытия. Ее образует устойчивой защитной среды вокруг сварочной дуги, поэтому шов получается с меньшей степенью защиты от внешних воздействий. Электроды с тонким покрытием используются преимущественно для сварки в условиях, где защита шва не является приоритетной, например, при проведении ремонтных работ с небольшими нагрузками.
- «С» – средняя толщина покрытия. Эта группа электродов универсальна и подходит для большинства сварочных задач, так как обеспечивает приемлемый уровень защиты зоны сварки от окружающей среды. Средняя толщина покрытия создает стабильную дугу и уменьшает количество брызг, улучшает качество шва. Электроды с маркировкой «С» используются для широкого спектра сварочных работ, где требуется баланс между эффективностью защиты и экономичностью.
- «Д» – толстое покрытие. Электроды с толстым покрытием выделяются высокими защитными свойствами. В процессе сварки они создают плотную защитную атмосферу, предотвращая попадание кислорода и других газов в зону дуги. Это снижает риск образования пор и других дефектов в шве. Такие расходники часто применяются при работе с металлами, подверженными коррозии и требующими высокой прочности соединения, например, в машиностроении и строительстве.
- «Г» – особо толстое покрытие. Эта категория имеет самое мощное покрытие, которое максимально защищает шов. В процессе плавления образует плотную шлаковую корку, предотвращающую взаимодействие расплавленного металла с окружающей средой. Электроды с особо толстым покрытием востребованы для сварки высоколегированных и ответственных сталей, особенно в агрессивных средах, где требования к прочности и долговечности соединения чрезвычайно высоки.
Толщина покрытия определяется соотношением диаметра покрытия (D) к диаметру стержня (d) и влияет на устойчивость дуги, защиту шва и скорость сварки. Выбор типа покрытия зависит от условий эксплуатации, типа металла и требований к прочности и надежности сварного соединения.
Пространственное положение
Теперь электроды в зависимости от пространственного положения при ведении шва. Маркируются цифрами, каждая из которых указывает на допустимые позиции для сварки:
- «1» – электроды, подходящие для сварки в любом положении. Они универсальны и позволяют выполнять качественные швы в различных пространственных положениях – вертикальное, горизонтальное, нижнее и потолочное. Такой тип расходников особенно востребован в промышленности и строительстве, где часто встречаются труднодоступные участки и нестандартные позиции для сварки.
- «2» – для ведения шва в любом положении, за исключением направленного сверху вниз. Надежное соединение при снизу вверх, горизонтальной и нижней позициях. Ограничение на ведение сверху вниз связано с трудностью поддержания стабильной дуги в этом положении, особенно на больших толщинных металлах.
- «3» – вертикальная сварка (включая движение снизу вверх), а также для горизонтального и нижнего положения. Они оптимальны для соединений, требующих прочного вертикального шва, и применяются в ситуациях, когда необходимо поддерживать стабильный контроль сварочной дуги при работе в вертикальном положении. Также подходят для горизонтальной сварки и в нижнем положении, что делает их универсальными для различных работ в этих позициях.
- «4» – электроды для сварки в нижнем положении, включая технику «лодочка». Этот тип используется в основном для создания крепких швов в нижней позиции, где контроль дуги и шва достигается за счет поддержки самого изделия. Техника «лодочка» помогает сварщику аккуратно распределять металл, исключая разбрызгивание и минимизируя дефекты. Ценны при работе с толстыми материалами и соединениями, требующими высокой прочности.
Выбор сварочных электродов, подходящих для конкретного положения и типа соединения, оказывает большое влияние на конечный результат. Знание особенностей маркировки и правильный подбор являются залогом качественной и эффективной сварки, что в свою очередь гарантирует прочность и долговечность сварных соединений в самых различных областях промышленности и строительства.
Свариваемый материал
Углеродистые и низколегированные стали, как правило, имеют относительно низкую устойчивость к термическим нагрузкам и склонны к образованию трещин при неправильном выборе сварочного метода и материалов. Сварка таких сталей требует стабильности сварочного процесса и минимизации дефектов в шве. Для этого наиболее эффективно подходят электроды с рутиловой, основной или смешанной обмазкой.
Есть ряд марок, которые идеальны для сварки углеродистых и низколегированных сталей. Оптимальный баланс между простотой использования, качеством сварного шва и прочностью соединения. Например:
- АНО-4 и АНО-6 – электроды с рутиловым покрытием, широко используемые для сварки углеродистых сталей, хорошо подойдут для работ в условиях переменного тока, обеспечивая стабильность дуги и гладкость шва. Для соединения деталей средней толщины и создания швов, не требующих высокой термостойкости.
- МР-3 и МР-3С – с рутилово-основным покрытием, которые используются для сварки как углеродистых, так и низколегированных сталей. Они позволяют получать швы с высокими механическими характеристиками и могут использоваться в различных положениях.
- ОЗС-6 – универсальные электроды с основным покрытием, предназначенные для сварки ответственных конструкций, где требуется высокая прочность шва. Часто используются в сварке труб и других металлических конструкций, подвергающихся сильным механическим и термическим нагрузкам.
- УОНИ 13/45 и УОНИ 13/55 – с основным покрытием, предназначенные для сварки низколегированных и углеродистых сталей, которые могут подвергаться воздействиям высоких температур и агрессивных сред. Обеспечивают отличную прочность шва и устойчивость к различным механическим и термическим нагрузкам.
Что касается нержавеющей стали, используют марки ЦЛ-11, ОЗЛ-6 и НЖ-13. Эти материалы способствуют созданию прочных сварных швов с отличной стойкостью к коррозии, что делает их подходящими для соединения нержавеющих конструкций, эксплуатируемых в агрессивных средах. Гарантируют не только высокое качество соединений, но и долговечность швов, способных противостоять воздействию влаги и химически активных веществ.
Если предстоит работать с алюминием, выбирают алюминиево-кремниевые стержни с щелочно-солевым покрытием. Например, ОЗАНА-2, ОЗАНА-1.
Постоянный ток
Сварка постоянным током с обратной полярностью является одним из наиболее распространенных методов для соединения тонкостенных изделий из различных материалов. С помощью нее получают более стабильный и аккуратный шов, так как реализуется качественная плавка и контролируемая динамика дуги, особенно на тонких металлических поверхностях. Применение постоянного тока особенно эффективно для работы с хромоникелевыми и жаростойкими сталями, где требуется высокая прочность шва и высокая устойчивость к агрессивным условиям эксплуатации.
На упаковке расходных материалов всегда приводятся рекомендуемые параметры силы тока, что позволяет оптимизировать процесс сварки и избежать перегрева или недонаплавления материала. Важно учитывать специфику материала и толщину свариваемых элементов, чтобы правильно выбрать нужные параметры.
К основным маркам электродов, используемым для сварки постоянным током, можно отнести следующие:
- ЦЛ-11 – стержни диаметром 3 мм, в составе которых присутствуют хром, никель и молибден. Эти электроды оптимальны для сварки конструкций, предназначенных для эксплуатации в агрессивных средах при температурных режимах до 450 °С. Они обладают высокой коррозионной стойкостью и сохраняют прочностные характеристики в условиях воздействия химически активных веществ.
- НЖ-13 – с высоким коэффициентом наплавки, для сварки емкостей, выполненных из хромоникелемолибденовой пищевой стали. Такие изделия используются для хранения и транспортировки пищевых продуктов, где необходимо сохранять не только механические свойства материала, но и его стойкость к повышенным температурам, часто превышающим 500 °С.
- НИИ-48Г – электроды, предназначенные для сварки высокомарганцовистых и аустенитных хромоникелевых жаростойких сталей. Применяются в условиях интенсивного воздействия агрессивных химических сред, например, в химической, нефтехимической и энергетической промышленности. Электроды NИИ-48Г обеспечивают качественное соединение таких металлов, сохраняя их высокие эксплуатационные характеристики при воздействии высоких температур и химических веществ.
Процесс прокалки электродов перед сваркой важен для достижения оптимальных свойств. Прокалка, проводимая в течение 1 часа при температуре 320–350 °С, помогает избежать появления дефектов на сварном шве, таких как трещины или поры, и улучшает проходимость дуги, особенно на сложных и ответственных участках.
Переменный ток
Для сварки нержавеющих сталей при переменном токе применяются различные марки электродов, в том числе:
- ЛЭЗ-8 – комбинированные электроды с рутиловой обмазкой, подходящие для работы как при постоянном, так и при переменном токе. Они хорошо зарекомендовали себя при сварке хромоникелевых сплавов и различных нержавеющих материалов. Эти электроды образуют шов с хорошей механической прочностью и устойчивостью к коррозии, что делает их идеальными для различных промышленных применений, включая строительство и судостроение.
- ОЗЛ-14 – рутиловые электроды, предназначенные для работы с нержавеющими хромоникелевыми сплавами, где качество шва не является критическим. Эти электроды дают хорошие результаты при сварке менее требовательных конструкций, в том числе при изготовлении простых конструктивных элементов, где основные требования — это адекватная механическая прочность и устойчивость к коррозии.
- ОЗЛ-14А – с рутиловой обмазкой, предназначенные для сварки с постоянным током обратной полярности, но также допустимо их использование на переменном токе. Данными расходниками формируют сварной шов, устойчивый к межкристаллитной коррозии, что особенно важно при эксплуатации в условиях высоких температур (до 650 °С). Такие электроды могут использоваться в пищевой промышленности, в энергетике и в химическом оборудовании.
- ЦТ-50 – рутиловые электроды с металлическим стержнем, содержащие около 22% хрома и до 10% никеля. Подходят для сварки высоколегированных нержавеющих сталей, которые должны выдерживать воздействие фтористых соединений, кислот и других агрессивных химических веществ. Этот тип электродов обладает высокой стойкостью к химическому воздействию и высокому температурному нагрузкам.
- Н-48 – с основным покрытием, предназначенные для сварки конструкций, работающих в агрессивных неокислительных средах при температуре до 300 °С. Особенно эффективны при соединении трубопроводов и других конструкций, подвергающихся химическому воздействию, где важна стойкость к коррозии и механическая прочность шва.
- АНВ-36 – стержни с основным покрытием, которые используются для сварки материалов, работающих при температурах до 500 °С. Для деталей, подвергающихся воздействию высоких температур и агрессивных химических сред, например, в промышленном оборудовании переработки нефтехимических продуктов.
Сварка переменным током – эффективный метод, широко используемый в различных отраслях промышленности. Потому создает потребность в большом ассортименте расходных стержней, которые подходят для самых разных применений – от строительства до высокотехнологичных сфер, таких как химическая и нефтехимическая промышленность. Точный подбор расходных материалов и корректная настройка сварочных параметров – залог высокого качества и долговечности соединений, надежности эксплуатации в любых условиях.
Новичкам и профессионалам: техника безопасности при дуговой сварке электродами
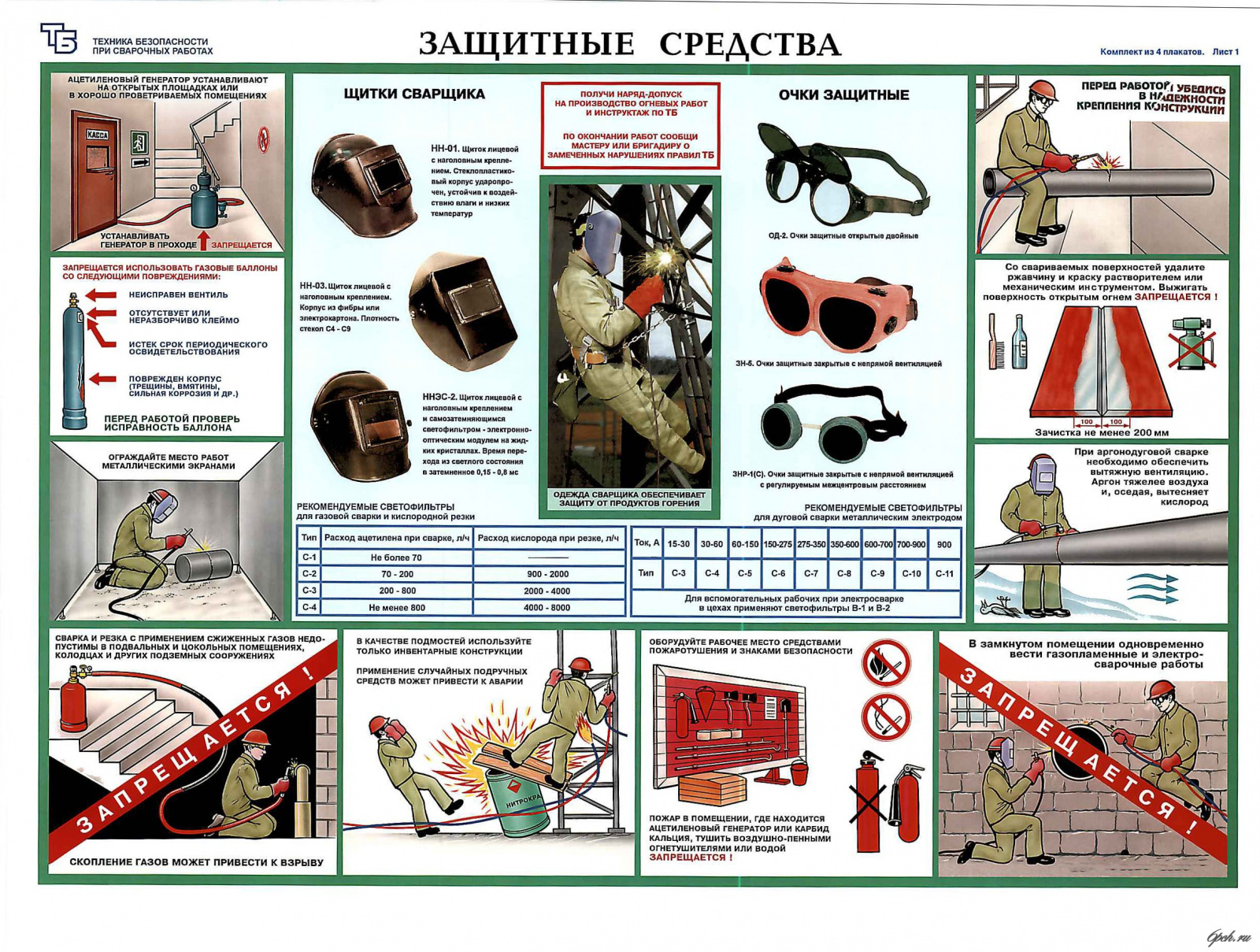
Дуговая сварка электродами – один из самых распространенных методов соединения металлических деталей. Этот процесс требует высокой температуры и сопровождается выделением яркого света, брызгами раскаленного металла, токсичными парами и дымом. Нарушение ТБ может привести к тяжелым травмам и профзаболеваниям, потому знание и соблюдение правил – обязательное условие для всех, кто работает с дуговой сваркой. Это касается как новичков, так и профессионалов. Изучите ТБ и соблюдайте все нормы, прежде чем приступать к работе!
Потенциальные опасности
Температура сварочной дуги, достигающая 6000°C и выше, приводит к плавлению металла, сопровождающемуся разлетом искр и раскаленных капель. Эти частицы способны мгновенно вызвать тяжелые ожоги и привести к пожарам. Недостаточная защита сварщика или ненадежная подготовка рабочего места повышают риск серьезных травм и возгораний.
Сварочная дуга испускает мощное ультрафиолетовое (УФ) и инфракрасное (ИК) излучение. Воздействие УФ-лучей вызывает ожоги кожи и глаз, а также конъюнктивит и кератит («сварочную болезнь») – воспаление роговицы.
При сварке металлов выделяются вредные газы – оксиды азота, угарный и углекислый газы, а также пары тяжелых металлов, содержащих марганец, хром и никель. Эти вещества становятся причиной головокружения, отравления, а при длительном воздействии – хронических заболеваний дыхательных путей.
Сварочное оборудование работает под напряжением, и при недостаточной изоляции или неправильном подключении не исключено поражение электрическим током, особенно если источник тока неисправен или рабочее место влажное.
Еще одна потенциальная опасность – механические травмы. Работа со сварочным оборудованием может привести к порезам, ушибам, переломам при падении тяжелых предметов или при неправильном использовании инструментов. Для снижения механических травм важно применять защитные перчатки и каски, а также соблюдать все составляющие технической безопасности.
Использование средств индивидуальной защиты (СИЗ)
СИЗ – это первый и важнейший рубеж защиты от всех опасностей, связанных со сваркой. Каждое средство защиты подбирается с учетом конкретных рисков:
- Сварочная маска с автоматическим светофильтром. Маска должна обеспечивать полную защиту лица и глаз от искр, УФ и ИК излучения. Светофильтр следует подбирать в зависимости от силы сварочного тока: чем выше ток, тем темнее должен быть фильтр. Оптимальный уровень затемнения обычно указывается в инструкции к оборудованию.
- Защитная одежда. Сварочный костюм должен быть из огнестойкого материала, например, плотной кожи или специальных тканей, устойчивых к воздействию тепла и искр. Одежда должна закрывать все участки тела, включая шею, руки и ноги. Одежда из синтетических тканей недопустима, так как она легко плавится и может вызвать серьезные ожоги.
- Сварочные перчатки. Перчатки – обязательно из термостойкого материала, надежно оберегающие от ожогов и механических повреждений. Лучше всего подходят из кожи с утепленной подкладкой.
- Средства защиты дыхательных путей. Респираторы или маски с фильтрами защищают от токсичных паров, выделяющихся при сварке. В условиях ограниченного пространства или при продолжительной работе – использовать принудительную вентиляцию.
Целостный подход к применению средств индивидуальной защиты значительно снижает риски, сопровождающие сварочные работы, и надежно оберегает от различных угроз: ожогов, травм глаз, повреждений органов дыхания и слуха. Подбор СИЗ должен основываться на особенностях условий и характера работы, с обязательной регулярной проверкой их состояния и строгим соблюдением всех норм безопасности.
Рабочее место
Правильная организация рабочего пространства – ключевой элемент безопасной работы со сварочным оборудованием. Здесь стоит обратить внимание на следующее:
- Вентиляция и вытяжка. При сварочных работах в помещении необходимо использование вытяжной вентиляции или локального проветривания, чтобы избежать накопления вредных газов. Принудительная вентиляция особенно важна в замкнутых пространствах и при сварке металлов, содержащих свинец или цинк, которые выделяют особо опасные пары.
- Очистка зоны от горючих материалов. Рабочее место необходимо освобождать от легковоспламеняющихся предметов – древесина, ткань, бумага и жидкости. В радиусе не менее 5 метров от сварочной зоны не должно быть горючих материалов. Помните, даже малейшая искра может стать причиной возгорания!
- Ограждение сварочного места. Сварочная дуга создает яркий свет, который серьезно вредит зрению людей, находящихся рядом. Для защиты окружающих и предотвращения случайного попадания искр используются ограждения, сварочные шторы или экраны, которые предотвращают рассеивание света и брызг электродного металла за пределы рабочего пространства.
- Организация удобного доступа к инструментам и оборудованию. Рабочее место должно быть организовано так, чтобы все необходимое оборудование, инструменты и материалы находились в удобной зоне досягаемости. Чтобы меньше отвлекаться на поиск инструментов, минимизировать вероятность споткнуться или случайно повредить оборудование. Сконцентрироваться на работе.
- Надежное закрепление заготовок. Все обрабатываемые детали должны быть прочно закреплены перед началом сварки. Неподвижные заготовки предотвращают возможные травмы, связанные с их случайным смещением или падением, и позволяют более точно контролировать сварной шов.
- Освещение рабочего места. Сварочные работы требуют хорошего освещения, особенно если они проводятся в помещении или в условиях ограниченной видимости. Минимальная освещенность на рабочем месте сварщика должна составлять не менее 200 люкс. В помещениях, где выполняется разметка, визуальная оценка сварки или работа с мелкими деталями – не менее 300 люкс. Правильное освещение снижает нагрузку на глаза, помогает точно оценивать детали и швы и повышает общее качество сварки.
Грамотно организованное рабочее пространство для сварки – залог безопасности и эффективности. Надежная вентиляция, удаление горючих материалов, ограждение зоны, удобное расположение инструментов и качественное освещение – чтобы процесс сварки был безопасным и комфортным, а производительность повышалась!
Обслуживание и настройка сварочного оборудования
Правильное техническое обслуживание оборудования – важное условие безопасности. Что в связи с этим нужно сделать:
- Регулярный осмотр оборудования. Перед началом работы проверяются целостность кабелей, изоляции, держателя электродов, а также надежность подключения заземления. Изношенные или поврежденные части могут привести к короткому замыканию или поражению током.
- Заземление аппарата. Сварочный источник должен быть надежно заземлен для предотвращения электротравмы. Необходимо избегать работы на влажной поверхности, чтобы уменьшить вероятность поражения током.
- Настройка силы тока. Сила тока настраивается в зависимости от типа металла и толщины свариваемого изделия. Слишком высокая – может привести к перегреву и увеличению числа брызг, а слишком низкая – к нестабильной дуге.
- Чистка и замена расходных материалов. Периодическая очистка блока охлаждения, корпуса, внутренних составляющих, держателей, контактов от пыли, шлака и окалины способствует стабильной работе оборудования, продлевает срок его службы. Важно своевременно менять изношенные детали – электроды, проволоку при необходимости, электрододержатель, зажим массы и т.д., поскольку напрямую влияют на качество сварного шва и безопасность процесса.
- Проверка исправности вентиляции. Охлаждающие системы и вентиляционные отверстия – регулярно проверять и очищать от загрязнений. Это предотвращает перегрев оборудования и снижает вероятность выхода из строя в критический момент.
- Контроль уровня изоляции. Изоляционные материалы должны быть целыми и неповрежденными, так как это одна из главных мер защиты от случайного поражения током. В случае обнаружения повреждений изоляцию следует незамедлительно восстановить или заменить.
Качественное ТО сварочного оборудования – не только основа безопасности, но и стабильность, качество сварки. Регулярные проверки, точная настройка параметров, надежное заземление и своевременный уход за оборудованием позволяют избежать аварий, продлить срок службы техники и поддерживать приемлемые условия безопасности работы.
Пожарная безопасность
Огнеопасность – одна из главных угроз при дуговой сварке, поэтому будьте здесь внимательны!
В зоне сварки должны находиться огнетушители, подходящие для тушения металлов (тип D) и жидкостей (тип B). Также полезно иметь под рукой огнеупорное покрытие или песок.
После окончания работ следует тщательно осмотреть рабочую зону, чтобы убедиться в отсутствии тлеющих искр и остатков, которые могут вызвать пожар после завершения сварочных работ.
Пожарная безопасность – это основа защиты не только для сварщика, но и для всего рабочего пространства. В дополнение к размещению огнетушителей классов D и B полезно оборудовать зону сварки огнеупорными ширмами, чтобы искры и брызги не разлетались за пределы рабочего места.
После завершения сварочных работ рекомендуется выделить время на проверку всей территории вокруг зоны сварки, включая труднодоступные места, чтобы убедиться в отсутствии даже малейших признаков тления. Также важно предусмотреть наблюдение за рабочей зоной в течение некоторого времени после окончания сварки, особенно если работы проводились рядом с горючими материалами.
Придерживаясь этих правил, минимизируют риск возникновения пожара и поддерживают безопасность для всех участников рабочего процесса.
Организация безопасного рабочего положения
Безопасное рабочее положение сварщика – это не просто рекомендация, а важная составляющая качественного и продуктивного труда. Правильно организованное рабочее место обеспечивает защиту здоровья и повышает эффективность работы, снижая риски травматизма. Сварочные работы всегда связаны с рядом потенциальных угроз: от термического воздействия и искр до повышенной усталости из-за неудобных поз.
Ключевые аспекты организации безопасного рабочего положения сварщика:
- Правильная эргономика. Расположение оборудования, зажимов и самого рабочего места должно соответствовать потребностям сварщика. Важно принимать устойчивое положение и не перенапрягать мышцы. Как результат – меньше лишней физнагрузки, сохранение здоровья позвоночника.
- Использование защитных средств. Каждое рабочее место должно быть оборудовано средствами защиты: сварочной маской, перчатками, специальной одеждой, обувью. Кроме того, особенно важна защита органов дыхания, так как во время сварки выделяются вредные вещества.
- Оптимальное освещение и вентиляция. Хорошая видимость зоны сварки – точное выполнение работы без грубых ошибок. Правильная вентиляция, в свою очередь, стабильно отводит вредные газы и частицы, защищая сварщика от их негативного воздействия.
- Устойчивость рабочей поверхности. Для предотвращения возможного смещения или падения, оборудование и заготовки должны быть надежно закреплены. Устойчивое положение сварочного аппарата, рабочего стола и других вспомогательных элементов снижает риск нештатных ситуаций.
- Регулярные перерывы и смена позиций. Для профилактики усталости и напряжения в мышцах важно регулярно делать перерывы, а также чередовать положение тела. Это дает возможность избежать перенапряжения и повысить продуктивность работы.
- Чистота и порядок на рабочем месте. Зачастую игнорируемый, но очень важный аспект. Чистота рабочей зоны уменьшает риски споткнуться, упасть или случайно повредить оборудование. Каждому инструменту – свое место! Работа ускоряется, а вероятность получения травм уменьшается.
Организация безопасного рабочего положения – продуманный процесс, где каждая деталь имеет значение. От правильной планировки рабочего места до применения защитных средств – все направлено на защиту здоровья и создание условий, при которых сварщик может выполнять свои задачи максимально эффективно и безопасно!
Как варить электродами новичку
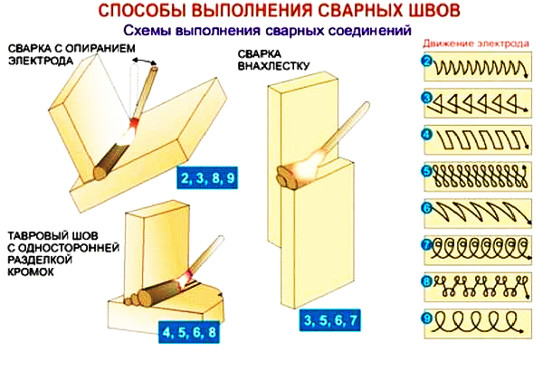
Сварку электродами – РДС – можно смело назвать одним из самых распространенных способов соединения металлов, несложным для освоения. Однако для успешного старта важно разобраться в основах: от выбора электродов и оборудования до базовых приемов и завершения. В этой части статьи шаг за шагом пройдем через весь процесс, начиная с подбора технических средств и расходников, и заканчивая практическими советами для первых попыток. Уверены, с нашими рекомендациями сможете уверенно приступить к сварке и постепенно развить свои навыки в этом непростом, но увлекательном мастерстве!
Выбор источника тока
Каким сварочным аппаратом варить новичку, делать первые попытки? Оптимальное и современное решение – инверторный источник питания дуги. Сначала в первичном низкочастотном выпрямителе сетевое переменное напряжение преобразует в постоянное, которое затем подает на инвертирующий блок. Тот, в свою очередь, преобразует постоянное напряжение частотой 50 Гц в переменное, но гораздо более высокой частоты, обычно в десятки килогерц. На следующем этапе высокочастотный трансформатор снижает напряжение и одновременно увеличивает ток, который может достигать значительных значений, что критично для сварочных процессов. В последующем вторичный выпрямитель снова преобразует переменное напряжение в постоянное, дроссель подает на электрод стабильный постоянный ток сварки.
Так работает инвертор. Компактнее трансформаторов и выпрямителей, устойчивый к перепадам напряжения, эффективный и удобный в использовании. Настройка сварочных параметров – одним движением! В нашем случае нужен инвертор MMA – ручной дуговой сварки электродами. Обязательно учитываем его параметры:
- Сила тока – отражает максимальную мощность, которую сварочный инвертор способен обеспечить в процессе работы. Этот параметр, измеряемый в амперах (А), определяет верхнюю границу тока, с которым аппарат может выполнять сварку. Например, если у инвертора максимальный ток 200 А, он подходит для материалов толщиной до 10 мм, в зависимости от техники и используемых расходников. Чем выше максимальная сила тока, тем больше возможностей для работы с более толстыми металлами и сложными условиями сварки.
- Питающая сеть – бытовая однофазная, с напряжением 220 В, или промышленная трехфазная 380 В.
- Продолжительность нагрузки – этот параметр указывает на то, как долго сварочный аппарат может работать на максимальном токе, прежде чем перегреется и потребует перерыва для охлаждения. Измеряется в процентах от времени работы при максимальном токе на протяжении 10 минут. Например, если инвертор с продолжительностью нагрузки 60% при 200 А, это значит, что на максимальном токе 200 А аппарат может работать 6 минут, после чего ему нужен отдых в 4 минуты для охлаждения.
- Класс изоляции – насколько хорошо сварочный инвертор защищен от перегрева и электрических замыканий. Определяет безопасность устройства при эксплуатации в различных условиях. Например, класс изоляции F или H (в зависимости от модели). F означает, что изоляция выдерживает температуры до 155 °C, а класс H – до 180 °C.
- Защита от перегрева – датчики отслеживают нагрев внутренних компонентов устройства. Мониторят температуру транзисторов, диодов и других ключевых элементов схемы. Когда температура достигает критического значения, срабатывает защита, источник автоматически отключается или снижается его мощность, чтобы предотвратить повреждение внутренних компонентов и продлить срок их службы. Световые или звуковые индикаторы предупреждают оператора о проблемах с перегревом. Дают возможность оперативно принять меры – прекратить работу или улучшить вентиляцию.
- Дополнительные функции – улучшаю и упрощают сварочный процесс. Например, Антиприлипание (Anti-Stick) – защищает электрод от прочного приваривания к поверхности материала, автоматически снижая ток, если есть вероятность прилипания. Горячий старт (Hot Start) – увеличенный стартовый ток при начале сварки, помогает легко зажигать дугу. Или функция форсажа дуги (Arc Force) – технология, которая помогает поддерживать стабильность электродуги путем временного увеличения тока в момент, когда капля расплавленного металла отделяется от электрода и попадает в сварочную ванну. Предотвращает прерывание дуги и прилипание электрода к материалу, способствуя созданию ровного и качественного сварного шва без сбоев.
Для новичков инверторы значительно облегчают сваривание. Простая настройка тока регулятором, автоматическое отключение в случае перегрева, горячий старт, антиприлипание и форсаж дуги – эти передовые решения делают процесс более удобным и предсказуемым, а швы – чистыми и качественными. Интуитивно понятные настройки и точная регулировка параметров помогают новичкам быстро освоить РДС и достигать отличных результатов с минимальными усилиями!
Выбор электродов
Электрод – металлический стержень со специальной обмазкой, расходный материал, ключевой элемент процесса ручной дуговой сварки, поскольку именно он отвечает за формирование качественного сварного шва. Во время сварки электрический ток, проходя через этот стержень, создает дугу, он плавится, как и металл, формируя прочное соединение. Покрытие электрода защищает сварочную ванну от окисления и повышает стойкость шва. Неправильно подобранный расходник может стать причиной дефектов – трещин, пористости, пониженной прочности, а иногда даже приводит к разрушению соединения при нагрузках.
Чтобы избежать подобных проблем, важно учитывать ряд факторов при выборе: это химический состав и толщина металла, который предстоит сваривать, пространственное положение шва, будущие условия эксплуатации изделия, а также тип и параметры сварочного оборудования. Правильно подобранный электрод – залог надежности и долговечности сварного соединения!
Итак, при выборе электродов учитываем следующие моменты:
- УОНИ-13/55 – с основным покрытием, которые подходят для сварки конструкционных сталей и ответственных элементов, работающих под высокими нагрузками. Помогают формировать высокопрочные швы, устойчивые к трещинам.
- АНО-21 – с рутил-целлюлозным покрытием, для углеродистых сталей, выполнения угловых, стыковых и нахлесточных соединений на металле толщиной от 1 до 5 мм. Стабильны как на переменном, так и на постоянном токе, в различных условиях работы.
- ОЗС-12 – для работы с углеродистыми и низколегированными сталями, имеющими временное сопротивление разрыву 490 Н/мм². Оснащены рутилово-основным покрытием, способствуют высокой прочности сварного шва и надежно защищают от коррозии.
- ЦЛ-11 – с основным покрытием, предназначены для конструкций из коррозионностойких хромоникелевых сталей – 12Х18Н10Т, 12Х18Н10 и 09Х18Н12Б. Такие расходники применяют в условиях агрессивной среды, где металл сварного шва должен обладать высокой устойчивостью к межкристаллитной коррозии.
Правильный выбор электродов РДС – неотъемлемая составляющая прочности и надежности соединений. При этом необходимо учитывать такие факторы, как тип основного металла, его толщину, положение во время сварки и условия эксплуатации готового изделия. Глубокое знание классификации и свойств покрытий поможет определять наилучший вариант для каждой конкретной задачи, создавать качественные и долговечные сварные швы!
Подготовка
Ознакомились с основами процесса, техникой безопасности, выбрали сварочный аппарат, электроды. Что дальше? Подготавливаем рабочее место, затем настраиваем источник сварочной дуги.
Что касается рабочего места, идеальным вариантом будет просторное помещение, оборудованное системой вентиляции. В процессе дуговой сварки выделяются вредные пары и газы, которые должны эффективно удаляться из рабочей зоны. Рекомендуется использовать вытяжные системы, которые будут захватывать вредные испарения непосредственно на месте их образования.
Рабочее место следует располагать вдали от горючих материалов. Для предотвращения возгорания для пола и стен желательно реализовать огнезащиту. Можно использовать металлические листы, кирпич, керамическую плитку или асбестовые покрытия.
Сварочные работы требуют хорошего освещения, чтобы точно позиционировать детали и контролировать сварочный шов. Рабочая зона должна быть освещена таким образом, чтобы свет не искажал видимость сварочной дуги и не слепил оператора. Лучше всего подходит мягкий рассеянный свет, дополненный локальными осветительными приборами.
Стол для сварки должен быть устойчивым и огнестойким. Стальная или металлическая рабочая поверхность идеальна. Высота стола должна быть удобной для работы в положении стоя или сидя, в зависимости от предпочтений сварщика и характера выполняемых задач.
Необходимо реализовать надежное заземление рабочего стола. Защищает сварщика и снижает риск повреждения оборудования.
На рабочем месте сварщика должны быть все необходимые инструменты:
- Сварочные электроды,
- электрододержатель,
- Молоток для отбивания шлака,
- Щетка для очистки сварочных швов,
- Различные вспомогательные приспособления (струбцины, зажимы, угольники и т. д.).
Желательно расположить инструменты так, чтобы доступ к ним был быстрым и удобным, а также предусмотреть место безопасного хранения.
Обязательно подготовить СИЗ! О них мы говорили выше.
При выполнении сварочных работ в условиях производства или на стройплощадке необходимо оградить рабочую зону, чтобы предотвратить случайный доступ к сварочному посту. Также важно установить предупреждающие знаки о проведении сварочных работ, чтобы коллеги знали о потенциальной опасности.
Проверьте, что рядом с рабочим местом нет легковоспламеняющихся жидкостей или других материалов, которые могут загореться от искр. Также убедитесь, что нет лишних предметов, о которые можно споткнуться или которые могут помешать свободному перемещению вокруг рабочего места.
Для своевременного устранения возможных возгораний необходимо, чтобы рядом с рабочим местом был огнетушитель, а также другие средства пожаротушения, например, ящик с песком. Убедитесь, что все присутствующие знают, как ими пользоваться.
Проверьте проводку, сварочный аппарат, соединения. Поврежденные кабели могут стать причиной короткого замыкания или даже возгорания.
Теперь о настройке сварочного инвертора.
Сила тока – основной параметр, который настраивается в зависимости от толщины металла и диаметра электрода. Обычно на упаковке электродов указаны рекомендуемые значения. Например, для расходников диаметром 3 мм рекомендуемый ток составляет около 90-120 А.
Полярность – некоторые инверторы позволяют менять полярность – прямую или обратную. Прямая (электрод к минусу) используется чаще, так как на ней качественно провариваются распространенные металлы.
В большинстве инверторов напряжение дуги устанавливается автоматически в зависимости от силы тока, но некоторые модели позволяют его настраивать. Более высокое напряжение обеспечивает более стабильную дугу, но может привести к сильному разбрызгиванию металла.
При необходимости активируйте полезные функции. Напомним, Hot Start – временное увеличение тока в момент зажигания дуги, облегчает начальное расплавление электрода. Полезно при сварке трудно воспламеняющихся материалов.
Arc Force – регулирует подачу тока при контакте электрода с металлом, предотвращает залипание электрода. Увеличение этого параметра делает дугу более жесткой и стабильной.
Anti-Stick – функция автоматического снижения тока при залипании электрода, упрощает его отсоединение от детали.
Выбор электродов также важен для качественной настройки. Низкоуглеродистые стали – смело используем рутиловые или основные электроды, например, марки МР-3 или УОНИ-13/55.
Среднелегированные типа 15ГС, 18Г2С, 25Г2С – электроды Э60А марки УОНИ-13/65.
Высоколегированные стали – Э-04Х20Н9 (ЦЛ-11), вариант для коррозионностойких хромоникелевых сталей.
Цветные металлы – ОЗАНА (для алюминия), АНЦ/ОЗМ (медь), ОЗЛ-32, НС-1 и НР-1, П-2Н4 (никель).
Подключение – сварочные инверторы подключаются к электрической сети с учетом их мощности и типа:
- 220 В – если аппарат рассчитан на питание от однофазной сети (обычно 220 В), подключите его через стандартную розетку, соответствующую мощности устройства. Источник тока мощностью более 3-4 кВт – рекомендуется использовать розетку с заземлением.
- 380 В – для мощных сварочных аппаратов, работающих от трехфазной сети, потребуется соответствующий подключающий кабель. Обязательно соблюдайте схему подключения фаз и нейтрали.
Помимо питания сварочный аппарат оснащен двумя основными проводами: электродным кабелем и кабелем заземления.
Один конец электродного кабеля подключается к сварочному аппарату, а другой – к держателю электрода.
Кабель заземления – подключается к сварочному аппарату и к металлической поверхности, которая будет свариваться. Или на которой лежит заготовка.
Перед тем как начать сварку, обязательно проконтролируйте, чтобы все подключения были надежными. Убедитесь, что кабели не повреждены, надежно изолированы. Проверьте наличие заземления. Убедитесь, что аппарат настроен правильно и нет коротких замыканий.
После всех подключений включите аппарат и проверьте работу устройства на холостом ходу (без сварки). Чтобы убедиться, что все подключено правильно, и источник готов к работе.
После настройки параметров проверьте дугу на пробной заготовке. Должна быть стабильной, а металл – плавно переноситься на шов без излишнего разбрызгивания.
Каждый инвертор имеет свои особенности, чтобы более точно настроить, ознакомьтесь с рекомендациями, указанными в инструкции к аппарату.
Ведение шва
Сварочный процесс подразумевает множество факторов, влияющих на конечный результат, и одним из таких выступает траектория движения электрода. Она может изменяться не только по углу наклона, но и по направлению, позволяя компенсировать погрешности при корректировке угла. Основные методы ведения сварочного электрода можно детально разделить на три группы, каждая из которых имеет свою область применения, исходя из толщины металла, условий сварки и типа шва.
Итак, варианты ведения, то есть формирования шва:
- Круговые и эллипсоидные движения. Такие траектории универсальные и широко используемые в сварке, особенно когда требуется равномерно прогреть кромки металла. Актуальны при создании вертикальных швов на сложных материалах, где необходимо избежать перегрева или недостаточного прогрева в определенных участках. Круговые движения помогают равномерно распределить теплоту по шву, металл стабильно плавится. Эллипсоидными траекториями, в свою очередь, более точно контролировать скорость охлаждения и температуру расплава, что критично для предотвращения появления трещин и дефектов в шве.
- Зигзагообразные и ломаные линии. Этот метод эффективен при сварке заготовок небольшой толщины – до 6 мм – в нижнем положении, когда требуется аккуратно соединить детали, например, встык. Зигзагообразные движения электрода создают условия равномерного прогрева сварочной ванны, таким образом избегают образования пустот или чрезмерной пористости в шве. При этом удается получить стабильное и качественное соединение, даже если кромки не были подготовлены. Зигзагообразной траекторией получают равномерную температуру на всей длине шва, а это особенно важно при сварке деталей с тонкими стенками, где необходимо избежать перегрева.
- Треугольник. Актуален на неповоротных стыках труб, где толщина металла также не превышает 6 мм. В отличие от предыдущих методов треугольная траектория предполагает движение электрода с переходами по трем точкам, с тщательной проработкой корня шва. В результате металл проплавляется глубоко, соединение надежное даже в местах с повышенными требованиями к прочности шва, например, на трубопроводах или других металлических конструкциях, подвергающихся высокому механическому напряжению.
Кроме того, есть ряд других техник, которые влияют на стабильность сварочного процесса. Например, простейшее поступательное движение. Помогает поддерживать стабильную длину дуги и постоянную скорость сварки. Поступательные движения могут быть использованы для различных типов сварки, особенно при необходимости точного контроля.
Прямолинейное движение – детальный контроль угла наклона и продолжительности расплава металла, что в свою очередь влияет на степень его проникновения и качественное формирование шва.
Когда сварщик делает амплитудные движения поперек шва, направленные под углом 45 градусов, он добивается оптимального прогрева кромки, существенно улучшает качество соединения. Этот метод используется для многослойных стыков, корневых швов, где важна тщательная проработка каждого слоя металла, а также для швов, которые подвергаются высоким термическим и механическим нагрузкам.
Еще варианты:
- Полумесяцем вперед – используется для стыковых швов с кромочными скосами и угловых соединений с катетом менее 6 мм. В любом положении с электродами диаметром до 4 мм.
- Полумесяцем назад – оптимальна для нижнего положения, вертикальных и потолочных швов с выпуклой наружной поверхностью. Помогает достичь равномерного прогрева и предотвращает образование дефектов.
- Треугольник с задержкой электрода в корне шва – применяется для толстостенных конструкций, глубоко проплавляется корневая часть шва, гарантируя прочность соединения.
- Петлеобразные движения – усиленный прогрев кромок, особенно при сварке высоколегированных сталей. При этом электрод задерживается на краях шва, предотвращая прожог в центре и вытекание металла, актуально для вертикальных соединений.
Правильное ведение влияет на внешний вид шва, но главное, определяет его долговечность и прочность, снижая вероятность дефектов и способствуя формированию качественного соединения!
Завершение
Чтобы соединение было прочным и долговечным, необходимо не только правильно вести сварочный процесс, но и корректно завершить его. Правильное завершение – финальный штрих, который влияет на прочность, внешний вид и устойчивость шва.
Для плавного завершения дуга должна быть стабильной. Прерывистая может оставить в шве пустоты или неровности, а всплески тока способны повредить материал и вызвать непровары.
Перед завершением сварки рабочую зону следует тщательно очистить от грязи, окалины и влаги.
Существует несколько распространенных техник завершения шва, каждая из которых имеет свои особенности. Выбор техники зависит от материала, типа соединения и условий работы.
Вот рабочие варианты:
- Остановка в шве. Этот метод часто применяется при выполнении коротких швов, когда задача состоит в том, чтобы просто прекратить подачу дуги в конце соединения. За несколько миллиметров до конца сплавления слегка уменьшите силу тока и замедлите движение электрода. Остановите стержень и потушите дугу прямо в шве, слегка отводя его от поверхности металла. Не будет резких перепадов температуры и обширного, глубокого кратера.
- Метод обратного движения – один из самых надежных способов завершения сварки, предотвращает образование кратера на финальной точке шва и способствует равномерному распределению тепла. Подходя к концу шва, уменьшите скорость ведения электрода, чтобы металл успел заполнить пространство. Проведите стержень назад по только что пройденному участку шва (примерно 5–10 мм), как бы возвращаясь к уже наплавленному металлу. Потушите дугу в конце шва, мягко убирая электрод под небольшим углом. Так заполните концевую часть и сформируйте прочное соединение.
- Заполнение кратера. Если в конце шва все же образовался кратер, важно не оставлять его пустым, так как ослабит шов. Заполнение кратера поможет сделать завершение более прочным. Замедлите движение электрода и немного задержитесь на месте. Постепенно уменьшайте силу тока, мягко отводя электрод от шва. Заполнение снизит вероятность образования дефектов.
После завершения сварки шов нуждается в плавном охлаждении, особенно при работе с материалами, подверженными образованию трещин (например, высокоуглеродистыми сталями). Быстрое охлаждение приведет к неравномерному распределению напряжений и вызовет трещины. Оставьте металл охлаждаться постепенно, не подвергая его воздействию холодного воздуха или воды.
При работе с чувствительными к трещинам металлами перед завершением сварки можно предварительно подогреть зону шва, чтобы избежать резкого перепада температуры.
После завершения и охлаждения обработайте и осмотрите соединение, чтобы удостовериться в его качестве и отсутствии дефектов.
Удалите шлак с помощью металлической щетки или молотка.
Осмотрите шов на наличие пор, трещин, кратеров или неровностей. Обратите внимание на структуру и равномерность поверхности – качественный шов должен быть ровным и без видимых пустот.
Если шов будет подвергаться визуальному осмотру или важен для эстетики конструкции, его можно отшлифовать для придания более гладкой и аккуратной формы.
Некоторые ошибки при завершении сварки, которые встречаются у новичков:
- Резкое отрывание электрода. Резкий отрыв часто приводит к образованию кратера, пор и микротрещин. Чтобы этого избежать, следует плавно ослаблять дугу и аккуратно убирать стержень.
- Чрезмерное охлаждение. Особенно это актуально при сварке толстых деталей или высокоуглеродистых сталей. Резкое охлаждение может привести к образованию трещин и деформации металла.
- Незаполненный кратер. Оставленный в конце шва кратер ослабляет соединение и делает его менее устойчивым к нагрузкам.
Правильное завершение ручной дуговой сварки электродами – ключевой этап получения качественного и надежного соединения. Аккуратное управление дугой, плавное заполнение кратера, контроль охлаждения и тщательная обработка – все это помогает избежать дефектов и работает на долговечность шва!
Полезные советы при сварке электродами
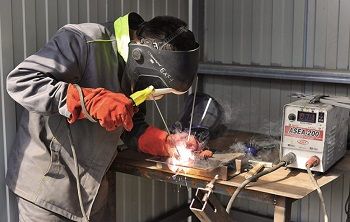
Главная настройка – сила тока. Влияет на глубину проплавления, структуру и надежность шва. Недостаточный ток приведет к слабому соединению, а избыточный может прожечь металл. Умножьте диаметр электрода на коэффициент 30-40, чтобы определить нужную силу тока.
Малый ток – для тонких листов, чтобы избежать прожога.
Средний и высокий ток – для толстых металлов.
Начинайте сварку с немного меньшего тока, чем требуется, и постепенно увеличивайте его, пока не получите ровный, чистый шов.
Тип и диаметр электрода играют решающую роль в качестве шва. Подбирая расходник, учитывайте тип металла, его толщину и условия сварки. Наиболее часто применяются рутиловые и основные электроды, каждый из которых имеет свои особенности:
- Рутиловые – подходят для работы с углеродистыми сталями, легко поджигаются, поддерживают стабильность как в нижнем положении, так и в случае вертикальных швов.
- Основные электроды (например, УОНИ-13/45) – для формирования высокопрочного соединения, устойчивого к механическим и термическим нагрузкам, но требуют повышенного внимания к подготовке и сухому хранению.
Перед началом сварки удостоверьтесь, что электроды сухие. Влажные расходники создадут проблемы, возможно, станут причиной пор и других дефектов.
Следите за положением электрода! Обычно рекомендуется держать его под углом 15-20° к направлению сварки – так лучше контролируется плавление, проще управлять сварочной ванной.
Для горизонтальных швов – угол слегка наклонен вниз, чтобы сварочная ванна не стекала.
Для вертикальных – электрод направляют перпендикулярно, чтобы металл не оседал вниз.
Потренируйтесь в удержании угла перед началом основной работы. Тренировки помогут добиться плавности и точности движений, необходимых для равномерного шва.
Качество сварки напрямую зависит от состояния поверхности металла. Ржавчина, краска, масло или грязь вызывают дефекты и снижают прочность соединения. Очистите поверхность перед началом работы, чтобы гарантировать надежность шва.
Для удаления загрязнений используйте металлическую щетку, шлифовальную машинку или абразивный круг. Чем лучше подготовлен металл, тем качественнее будет шов.
Обратите внимание еще на это:
- Длина дуги влияет на температуру и стабильность плавления металла. При ручной дуговой сварке рекомендуется поддерживать короткую дугу, примерно равную диаметру электрода. НО здесь важен баланс. Слишком длинная – вызывает разбрызгивание металла и поры, а слишком короткая – залипание электрода. Постарайтесь удерживать дугу стабильно на уровне, позволяющем контролировать процесс и избегать лишних брызг. Хорошо видимая сварочная ванна – знак, что длина электродуги выбрана правильно.
- Постоянный темп движения. Скорость движения электрода непосредственно влияет на внешний вид и качество шва. Слишком медленное движение может привести к избыточному наплавлению металла и образованию наплывов, а слишком быстрое – к узкому шву с недостаточной глубиной провара. Попробуйте поддерживать постоянный темп, варьируя его в зависимости от изменения толщины металла и температуры сварочной ванны. Ровный шов обычно является результатом стабильного и продуманного движения.
- Использование защитного оборудования. Сварка сопровождается выделением яркого света, искр и вредных паров, поэтому соблюдение правил безопасности – залог сохранения здоровья. При сварке обязательно используйте сварочную маску с затемненным стеклом, защитные перчатки и одежду, чтобы избежать ожогов от раскаленных брызг и дуги, респиратор или вентиляцию, если работаете в закрытом помещении. Выбирайте маску с хорошей степенью затемнения (DIN 9–13), подходящей для дуговой сварки, и удобную одежду, защищающую от искр.
- Проверка шва и устранение дефектов. После завершения тщательно осмотрите сварной шов. Поры, трещины или неровности негативно сказываются на надежности соединения и становятся местами потенциального разрыва. Регулярная проверка позволяет своевременно исправить недочеты. Если вы обнаружили дефекты, срежьте их шлифовальной машиной и проварите участок заново. Важно не оставлять некачественные места, особенно при сварке ответственных конструкций!
Ручная дуговая сварка электродами – метод, доступный и универсальный, но требует внимания и аккуратности. Следуя указанным советам, вы сможете добиться прочного и эстетически привлекательного шва. Освоение основных принципов и навыков поможет вам уверенно начать, развиваться, в дальнейшем справляться с все более сложными сварочными задачами!
Заключение
Ручная дуговая сварка штучными электродами с покрытием – метод, доступный для новичков, однако к нему нужен комплексный подход.
Во-первых, ознакомиться с техникой безопасности. Во-вторых, понимать, что такое источник сварочного тока, как происходит сварка. В-третьих, грамотно подготовиться к процессу, выбрать подходящие электроды, корректно настроить аппарат. Плавно начать. Научиться вести электрод, сначала делать простейшие швы, а потом переходить к более сложным. Завершить сварку должным образом, чтобы минимизировать риск образования дефектов.
Об этом мы подробно рассказали в нашей статье. Надеемся, она станет полезным руководством для начинающих сварщиков, поможет избежать распространенных ошибок и ускорить процесс обучения. Овладение даже основами ручной дуговой сварки требует времени и терпения, но при комплексном подходе, последовательности и практических тренировках каждый сможет достичь определенных вершин.
Сварка – не только полезный навык, это еще и увлекательно, особенно, когда получается! С каждым новым опытом раскрывает свои тонкости.
Желаем успехов и безопасной работы, уверенности при любой сварочной задаче, удовольствия от процесса и результата!